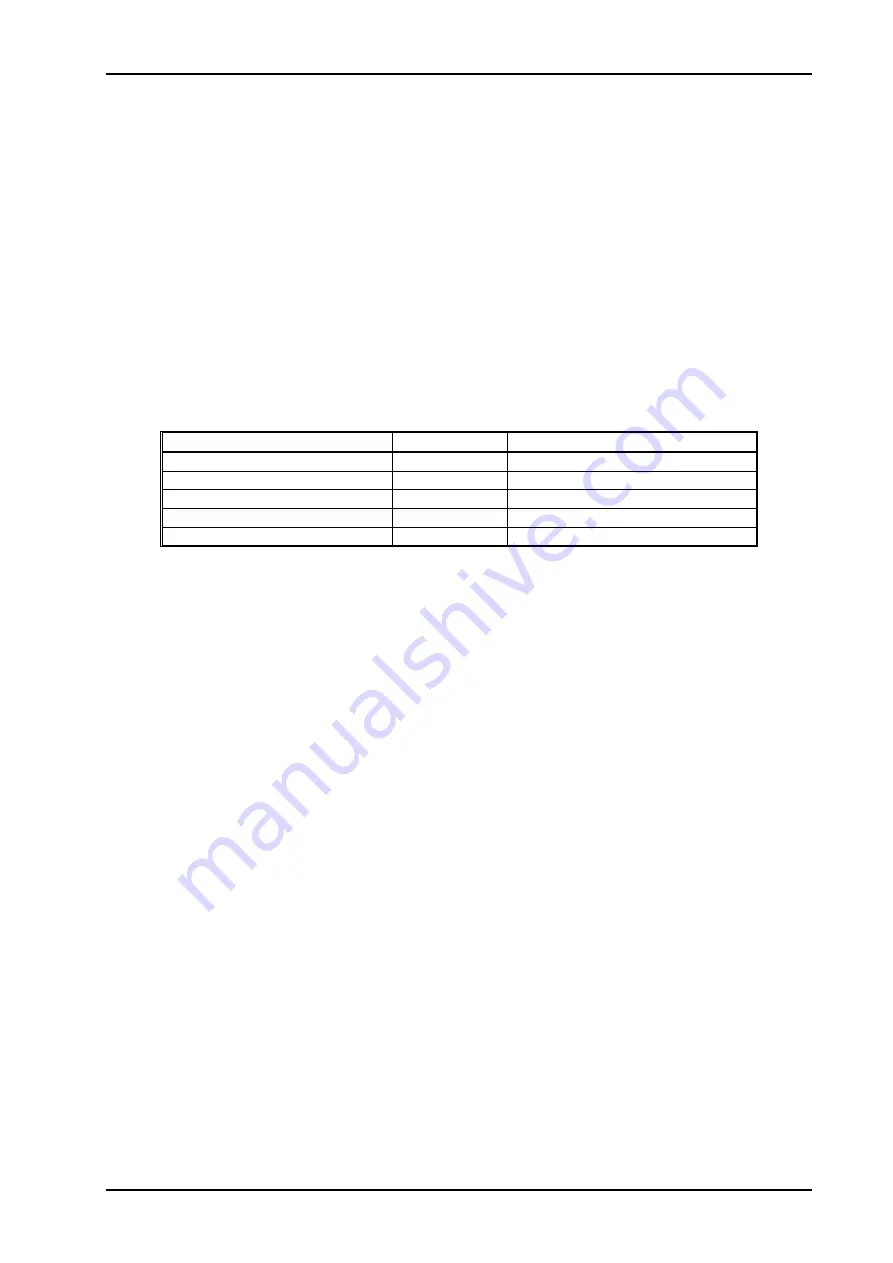
Danaher Motion Kollmorgen Speciality Electronics
System Startup
SERVO
STAR
CD-LITE User Manual
11
Feedback
The SERVO
STAR
provides a motor position output to you in the form of quadrature encoder
signals eliminating the need for an additional position feedback device. The outputs are
differential line drivers. There is an associated DC common output (C4: pin 3) which can connect
to your port to keep common mode noise and voltage spikes minimized for device protection.
Because there are normally differences of potential between your controller and the drive,
connection is recommended (if ground loops occur, disconnect and retest).
The source of the Encoder Equivalent Output (EEO) signals depends on the type of motor
feedback device:
This section describes the various feedback types and how they function beginning with firmware version
0.1.8.
Type MENCTYPE
Comments
Incremental A/B/Z/Halls
0
Incremental A/B/H
6
Resolver NA
Halls only w/ sinus commutation
5
Defined in
MOTIONLINK
Hall only w/ six step commutation
10
Defined by setting DIP switch 2 to ON
Incremental Encoder
The output signal is the actual encoder feedback signal that is pre-configured (MENCRES) in the
drive’s motor parameters. It can be scaled down by multiples of two (ENCOUTO: 1, 2, 4, 8, 16)
and has a maximum frequency limit of 3 MHz.
The SERVO
STAR
can use encoder feedback to monitor the motor shaft position. As opposed to
a resolver, which is an absolute position feedback device, the encoder is an incremental device
that indicates changes in position. The encoder resolution of the SERVO
STAR
(and therefore
the drive’s encoder equivalent output) is fixed because it is a hardware characteristic of the
encoder device. The encoder interface includes three groups of wires:
1.
A/B (and complements) lines make up the encoder quadrature signals. The signals are
received differentially through line receivers before being passed through a wire-break
detection circuit.
2.
The narrow Index pulse normally appears once per revolution and indicates a known
physical position of the shaft. This pulse is received differentially through a line receiver
before being passed through a wire-break detection circuit. This signal is hardware-
capturable.
3.
Hall signals provide information representing the approximate absolute location of the
motor shaft. From this information, the motor can sinusoidally commutate forward until
the index signal is detected - at which time, true position is known. These signals are
isolated by an opto-coupler and can be differential or open-collector type signals.
Artisan Technology Group - Quality Instrumentation ... Guaranteed | (888) 88-SOURCE | www.artisantg.com