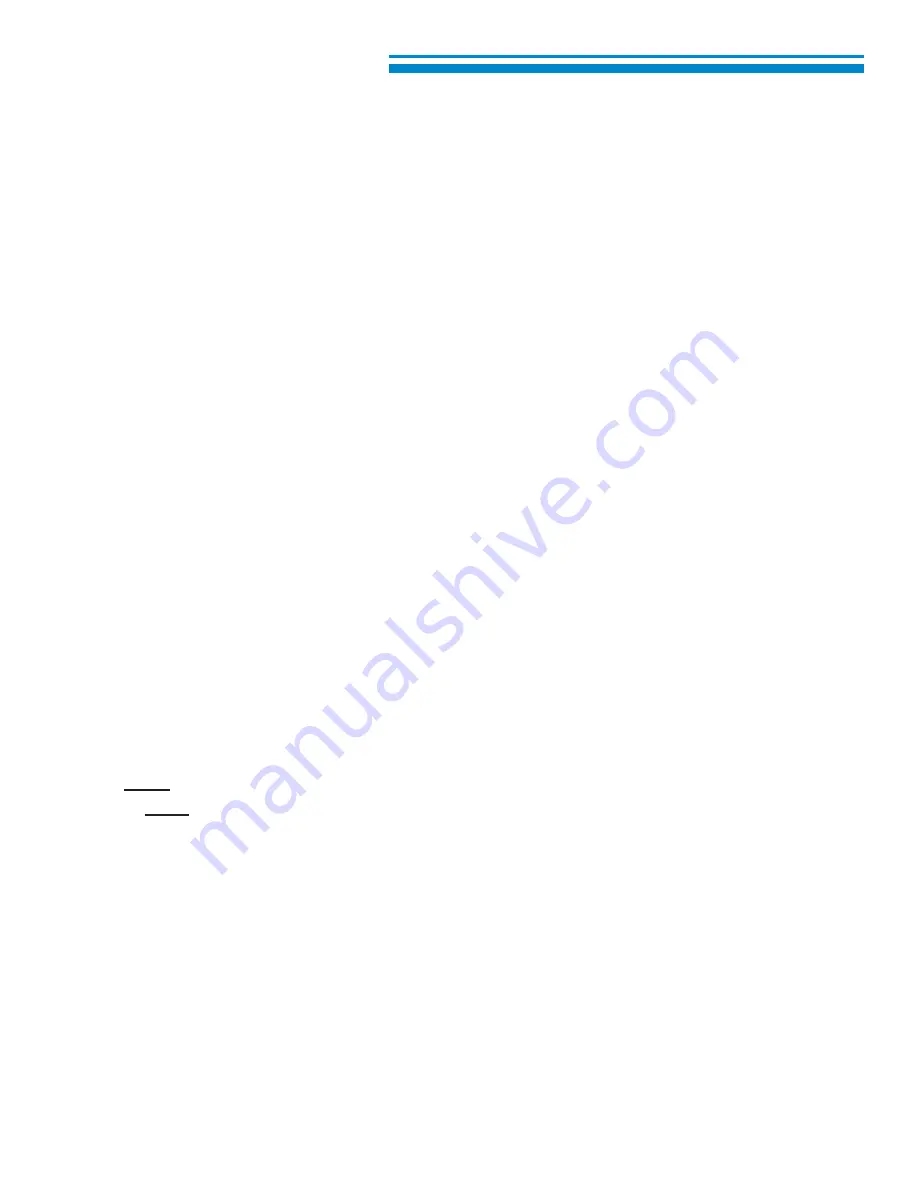
7
HUB-SPINDLE SUB-ASSEMBLY
8. Turn
hub (1G)
over, onto its spindle. Place
bearing cone (1F)
down, onto
spindle
(1A)
in
hub (1G)
and, using tool (T-146588), press
bearing cone (1F)
into hub.
9.
Place tanged
washer (1H)
over the end of
spindle (1A)
.
10.
Place
lockwasher (1J)
over the end of
spindle (1A)
.
11.
Spray
locknut (1K)
with “Primer T”. Allow 2-3 minutes’ drying time.
NOTE: The Loctite to be used in the next step in an anaerobic adhesive. Once out of
contact with the air, it begins to set.
Read over steps 12A-16A and 12B-15B before doing them.
- If you have a locknut wrench, do steps 12A to 16A.
- If you do NOT have a locknut wrench, do steps 12B to 15B: field rolling torque procedure.
12A.
Apply “Loctite 277” to
locknut (1K).
13A.
Place
locknut (1K)
over the end of
spindle (1A)
and tighten a little by hand.
Summary of Contents for SPICER Torque-Hub S6B
Page 1: ...Torque Hub Assembly Disassembly Manual S6B ...
Page 20: ...15 TOOL LIST T 130717 ASSEMBLY PRESSING TOOL FOR BEARING CUP 1E ...
Page 21: ...16 TOOL LIST T 156792 ASSEMBLY PRESSING TOOL FOR CUP 1C ...
Page 22: ...17 TOOL LIST T 156766 AN_18 LOCKNUT WRENCH ...
Page 23: ...18 TOOL LIST T 156799 ASSEMBLY PRESSING TOOL FOR SEAL 1B ...
Page 24: ...19 TOOL LIST T 146588 ASSEMBLY PRESSING TOOL FOR BEARING CONE 1F ...