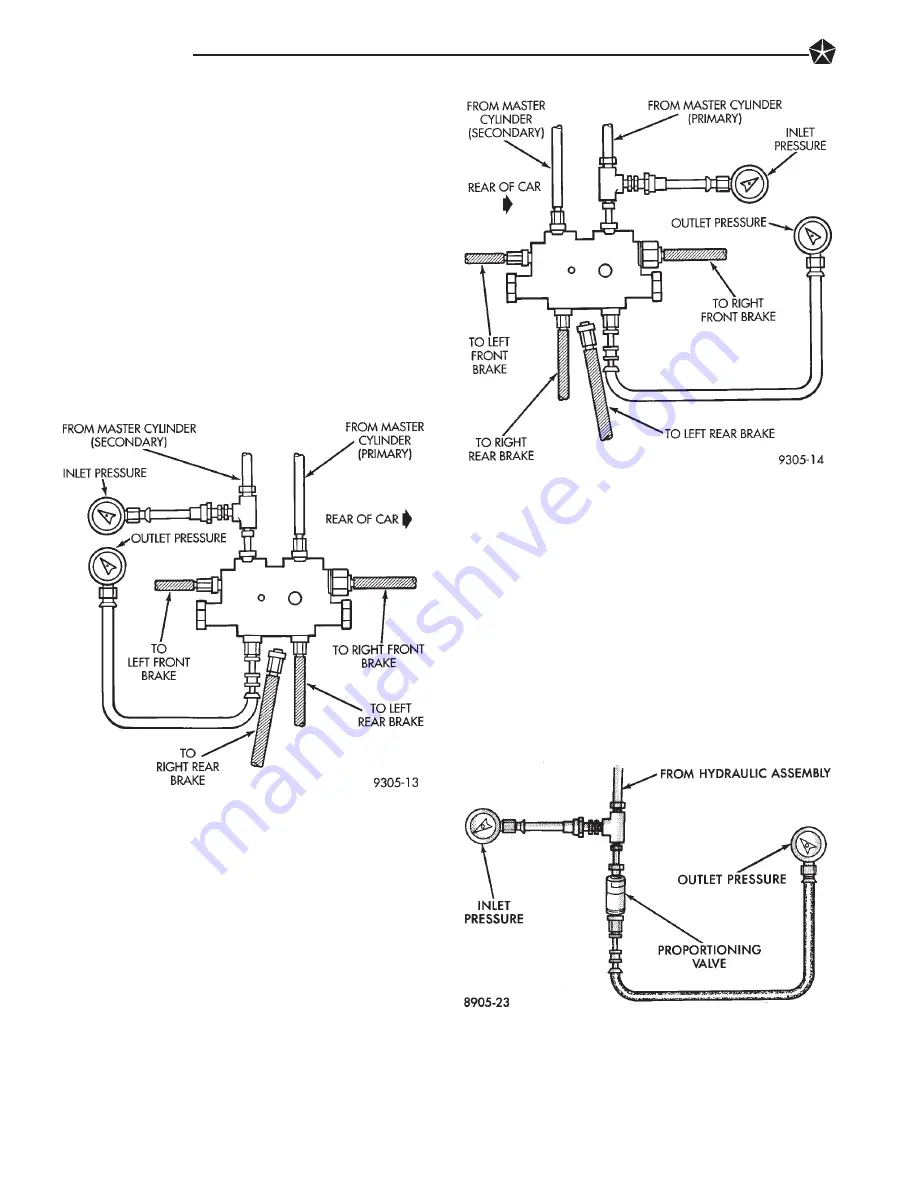
To test the proportioning valve when the right rear
wheel slides first, leave the front brakes connected to
the valve, and proceed as follows:
(1) Install one gauge and (TEE) of set C-4007-A
between the brake line from the master cylinder sec-
ondary port and the brake valve assembly (Fig. 1).
(2) Install the second gauge of set C-4007-A to the
right rear brake outlet port (Fig. 1). Gauge to be
attached using an adapter tube, made from a short
piece of brake tube and (1) 3/8 x 24 tube nut, and (1)
M10x1 tube nut. Connect the hose to the valve. Bleed
the hose and gauge.
(3) Have a helper exert pressure on the brake pedal
(holding pressure) to get a reading on the valve inlet
gauge and check the reading on the outlet gauge. If
the inlet and outlet pressures do not agree with the
values on the following chart, replace the valve.
LEFT REAR WHEEL SLIDES FIRST
To test the proportioning valve when the left rear
wheel slides first, leave the front brakes connected to
the valve, and proceed as follows:
(1) Install one gauge and (TEE) of set C-4007-A
between brake line from master cylinder primary port
and brake valve assembly (Fig. 2).
(2) Install the second gauge of set C-4007-A to the
left rear brake outlet port (Fig. 2). An adapter tube,
made up from a M12x1 tube nut, a short piece of
brake tube and 3/8 x 24 tube nut, will be required to
connect hose to valve. Bleed the gauge and hose.
(3) Have a helper exert pressure on the brake
pedal. Hold pressure steady to get a reading on the
valve inlet gauge and check the reading on the outlet
gauge. If the inlet and outlet pressures do not agree
with the values on the following chart, replace the
valve.
TESTING ABS PROPORTIONING VALVES
All ABS components use an ISO type tubing flare.
Use the correct adapters with ISO type tubing flares
when installing gauges to test ABS proportioning
valves.
(1) Install one gauge and (TEE) between the hy-
draulic assembly and the male end (Inlet) of the
valve.
(2) Install the second gauge at the female end (Out-
let) of the valve (Fig. 3).
(3) Have a helper exert pressure on the brake pedal
(holding pressure) to get a reading on the valve inlet
gauge.
(4) Check the reading on the outlet gauge. If the
inlet and outlet pressures do not agree with the fol-
Fig. 1 Tube Connection For Right Rear Skidding
Fig. 2 Tube Connection For Left Rear Skidding
Fig. 3 Tube Connections for ABS
5 - 26
BRAKES
Summary of Contents for LH New Yorker 1994
Page 19: ......
Page 21: ...Fig 1 L H Platform Front Suspension 2 2 SUSPENSION AND DRIVESHAFTS...
Page 22: ...SUSPENSION STEERING DIAGNOSIS FRONT WHEEL DRIVE SUSPENSION AND DRIVESHAFTS 2 3...
Page 24: ...Fig 2 L H Platform Front Suspension SUSPENSION AND DRIVESHAFTS 2 5...
Page 41: ...Fig 1 Front Stabilizer Bar And Stabilizer Bar Mounting 2 22 SUSPENSION AND DRIVESHAFTS...
Page 60: ...SUSPENSION STEERING DIAGNOSIS FRONT WHEEL DRIVE SUSPENSION AND DRIVESHAFTS 2 41...
Page 66: ...Fig 1 L H Platform Driveshaft Components SUSPENSION AND DRIVESHAFTS 2 47...
Page 73: ...Fig 1 L H Platform Fully Independent Rear Suspension 2 54 SUSPENSION AND DRIVESHAFTS...
Page 103: ...BRAKE SYSTEM DIAGNOSTICS 5 12 BRAKES...
Page 104: ...BRAKE SYSTEM DIAGNOSTICS BRAKES 5 13...
Page 105: ...BRAKE SYSTEM DIAGNOSTICS BRAKE SYSTEM DIAGNOSTICS 5 14 BRAKES...
Page 143: ...FIG 2 PARKING BRAKE CABLE ROUTING 5 52 BRAKES...
Page 195: ......
Page 197: ...COOLING SYSTEM DIAGNOSIS 7 2 COOLING SYSTEM...
Page 198: ...COOLING SYSTEM DIAGNOSIS COOLING SYSTEM 7 3...
Page 199: ...COOLING SYSTEM DIAGNOSIS 7 4 COOLING SYSTEM...
Page 200: ...COOLING SYSTEM DIAGNOSIS COOLING SYSTEM 7 5...
Page 201: ...COOLING SYSTEM DIAGNOSIS 7 6 COOLING SYSTEM...
Page 202: ...COOLING SYSTEM DIAGNOSIS COOLING SYSTEM 7 7...
Page 217: ...SPECIFICATIONS TORQUE COOLING SYSTEM CAPACITY 7 22 COOLING SYSTEM...
Page 219: ......
Page 224: ...Fig 7 Battery Diagnostics BATTERY STARTING CHARGING SYSTEMS DIAGNOSTICS 8A 5...
Page 235: ...Fig 14 Starter Relay Tests 8A 16 BATTERY STARTING CHARGING SYSTEMS DIAGNOSTICS...
Page 238: ...Fig 1 Charging Diagnostics BATTERY STARTING CHARGING SYSTEMS DIAGNOSTICS 8A 19...
Page 241: ...Fig 6 Generator Diagnostic Trouble Codes 8A 22 BATTERY STARTING CHARGING SYSTEMS DIAGNOSTICS...
Page 242: ...Fig 7 Check For Inadequate Low Charging BATTERY STARTING CHARGING SYSTEMS DIAGNOSTICS 8A 23...
Page 243: ...Fig 8 Check For Overcharging 8A 24 BATTERY STARTING CHARGING SYSTEMS DIAGNOSTICS...
Page 257: ......
Page 293: ...Fig 24 Instrument Panel Breakdown 8E 8 INSTRUMENT PANEL AND GAUGES...
Page 294: ...Fig 25 Instrument Panel Breakdown New Yorker INSTRUMENT PANEL AND GAUGES 8E 9...
Page 301: ...AM FM STEREO CASSETTE TAPE 8F 2 AUDIO SYSTEM...
Page 302: ...AM FM STEREO CONTINUED AUDIO SYSTEM 8F 3...
Page 303: ...AM FM STEREO CONTINUED AM FM STEREO CONTINUED 8F 4 AUDIO SYSTEM...
Page 304: ...INFINITY AUDIO SYSTEM 8F 5...
Page 305: ...INFINITY CONTINUED 8F 6 AUDIO SYSTEM...
Page 306: ...INFINITY CONTINUED AUDIO SYSTEM 8F 7...
Page 307: ...INFINITY CONTINUED 8F 8 AUDIO SYSTEM...
Page 308: ...INFINITY CONTINUED AUDIO SYSTEM 8F 9...
Page 309: ...INFINITY CONTINUED 8F 10 AUDIO SYSTEM...
Page 310: ...Fig 1 Radio Connector Circuits AUDIO SYSTEM 8F 11...
Page 319: ...Fig 2 Horn Diagnosis 8G 2 HORNS...
Page 321: ......
Page 324: ...Fig 4 System Diagnosis VEHICLE SPEED CONTROL SYSTEM 8H 3...
Page 325: ...Fig 5 System Diagnosis Continued 8H 4 VEHICLE SPEED CONTROL SYSTEM...
Page 333: ......
Page 336: ...Fig 5 Wiper Motor Runs Diagnosis WINDSHIELD WIPER AND WASHER SYSTEMS 8K 3...
Page 337: ...Fig 6 Wiper Motor Will Not Run Diagnosis 8K 4 WINDSHIELD WIPER AND WASHER SYSTEMS...
Page 350: ...Fig 6 Headlamp Bubble Level Calibration Fig 5 Fog Lamp Alignment Screen LAMPS 8L 5...
Page 368: ...Fig 4 Fog Lamp Alignment Screen LAMPS 8L 3...
Page 381: ...Fig 9 Instrument Panel Components 8M 6 RESTRAINT SYSTEMS...
Page 382: ...Fig 10 Instrument Panel Components New Yorker RESTRAINT SYSTEMS 8M 7...
Page 387: ......
Page 391: ......
Page 401: ......
Page 404: ...Fig 4 Seat Track Removal POWER SEATS 8R 3...
Page 405: ......
Page 408: ...ELECTRICAL GROUP INDEX IGNITION SYSTEM 8D LAMPS 8L WIRING DIAGRAMS 8W ELECTRICAL 8A 1...
Page 414: ......
Page 421: ...Fig 11 Symbol Identification WIRING DIAGRAMS 8W 7...
Page 422: ...Fig 12 Controller and Module Locations 8W 8 WIRING DIAGRAMS...
Page 423: ...Fig 13 Wiring Harness Routing WIRING DIAGRAMS 8W 9...
Page 424: ...Fig 14 Ground Identification Chart 8W 10 WIRING DIAGRAMS...
Page 425: ...Fig 15 Power Distribution Center Identification WIRING DIAGRAMS 8W 11...
Page 426: ...Fig 16 Junction Block Identification 8W 12 WIRING DIAGRAMS...
Page 428: ...Fig 1 Deck Lid Wiring Fig 2 Trunk Area Wiring 8W 14 WIRING DIAGRAMS...
Page 429: ...Fig 3 Body Wiring Right Rear Fig 4 Body Wiring Left Rear WIRING DIAGRAMS 8W 15...
Page 430: ...Fig 5 Body Wiring Right Front Fig 6 Body Wiring Left Side 8W 16 WIRING DIAGRAMS...
Page 431: ...Fig 7 Body Wiring Left Side Fig 8 ABS System Wiring Rear WIRING DIAGRAMS 8W 17...
Page 434: ...Fig 13 Steering Column Wiring Fig 14 Door Wiring Rear 8W 20 WIRING DIAGRAMS...
Page 435: ...Fig 15 Door Wiring Front Fig 16 Engine Compartment Wiring Right Front WIRING DIAGRAMS 8W 21...
Page 437: ...Fig 19 Engine Compartment Wiring Left Rear Fig 20 Generator Wiring WIRING DIAGRAMS 8W 23...
Page 438: ...Fig 21 Battery Wiring Fig 22 Starter and Transmission Wiring 8W 24 WIRING DIAGRAMS...
Page 439: ...Fig 23 Engine Wiring 3 3L WIRING DIAGRAMS 8W 25...
Page 440: ...Fig 24 Engine Wiring 3 5L 8W 26 WIRING DIAGRAMS...
Page 441: ...Fig 25 Underhood Lamp Wiring WIRING DIAGRAMS 8W 27...
Page 442: ...8W 28 WIRING DIAGRAMS...
Page 444: ...Fig 1 Deck Lid Splices Fig 2 Trunk Area Splices 8W 30 WIRING DIAGRAMS...
Page 445: ...Fig 3 Body Splices Left Side Fig 4 Headliner Splices WIRING DIAGRAMS 8W 31...
Page 446: ...Fig 5 Door Splices Fig 6 HEVAC Splices 8W 32 WIRING DIAGRAMS...
Page 447: ...Fig 7 Instrument Panel Splices Fig 8 Instrument Panel Splices WIRING DIAGRAMS 8W 33...
Page 448: ...Fig 9 Transmission Splices Fig 10 Engine Compartment Splices Right Front 8W 34 WIRING DIAGRAMS...
Page 450: ...Fig 13 Engine Compartment Splices Left Rear Fig 14 Engine Splices 3 3L 8W 36 WIRING DIAGRAMS...
Page 451: ...Fig 15 Engine Splices 3 5L WIRING DIAGRAMS 8W 37...
Page 452: ...8W 38 WIRING DIAGRAMS...
Page 460: ......
Page 461: ......
Page 462: ......
Page 463: ......
Page 464: ......
Page 465: ......
Page 466: ......
Page 467: ......
Page 468: ......
Page 469: ......
Page 470: ......
Page 471: ......
Page 472: ......
Page 473: ......
Page 474: ......
Page 475: ......
Page 476: ......
Page 477: ......
Page 478: ......
Page 479: ......
Page 480: ......
Page 481: ......
Page 482: ......
Page 483: ......
Page 484: ......
Page 485: ......
Page 486: ......
Page 487: ......
Page 488: ......
Page 489: ......
Page 490: ......
Page 491: ......
Page 492: ......
Page 493: ......
Page 494: ......
Page 495: ......
Page 496: ......
Page 497: ......
Page 498: ......
Page 499: ......
Page 500: ......
Page 501: ......
Page 502: ......
Page 503: ......
Page 506: ......
Page 507: ......
Page 508: ......
Page 509: ......
Page 510: ......
Page 511: ......
Page 512: ......
Page 513: ......
Page 514: ......
Page 515: ......
Page 516: ......
Page 517: ......
Page 518: ......
Page 519: ......
Page 520: ......
Page 521: ......
Page 522: ......
Page 523: ......
Page 524: ......
Page 525: ......
Page 526: ......
Page 527: ......
Page 528: ......
Page 529: ......
Page 530: ......
Page 531: ......
Page 532: ......
Page 533: ......
Page 534: ......
Page 535: ......
Page 536: ......
Page 537: ......
Page 538: ......
Page 539: ......
Page 540: ......
Page 541: ......
Page 542: ......
Page 543: ......
Page 544: ......
Page 545: ......
Page 546: ......
Page 547: ......
Page 548: ......
Page 549: ......
Page 550: ......
Page 551: ......
Page 552: ......
Page 553: ......
Page 554: ......
Page 555: ......
Page 556: ......
Page 557: ......
Page 558: ......
Page 559: ......
Page 560: ......
Page 561: ......
Page 562: ......
Page 563: ......
Page 564: ......
Page 565: ......
Page 566: ......
Page 567: ......
Page 568: ......
Page 569: ......
Page 570: ......
Page 571: ......
Page 572: ......
Page 573: ......
Page 574: ......
Page 575: ......
Page 576: ......
Page 577: ......
Page 578: ......
Page 579: ......
Page 580: ......
Page 581: ......
Page 582: ......
Page 583: ......
Page 584: ......
Page 585: ......
Page 586: ......
Page 587: ......
Page 588: ......
Page 589: ......
Page 590: ......
Page 591: ......
Page 592: ......
Page 593: ......
Page 594: ......
Page 595: ......
Page 596: ......
Page 597: ......
Page 598: ......
Page 599: ......
Page 600: ......
Page 601: ......
Page 602: ......
Page 603: ......
Page 604: ......
Page 605: ......
Page 606: ......
Page 607: ......
Page 608: ......
Page 609: ......
Page 610: ......
Page 611: ......
Page 612: ......
Page 613: ......
Page 614: ......
Page 615: ......
Page 616: ......
Page 617: ......
Page 618: ......
Page 619: ......
Page 620: ......
Page 621: ......
Page 622: ...1994 New Yorker LHS Concorde Intrepid Vision Publication No 81 270 4140 TSB 26 04 95 June 1995...
Page 623: ......
Page 624: ......
Page 626: ......
Page 632: ...ENGINE DIAGNOSIS PERFORMANCE 9 6 ENGINE...
Page 633: ...ENGINE DIAGNOSIS MECHANICAL ENGINE 9 7...
Page 661: ...ENGINE SPECIFICATIONS 3 3L ENGINE 9 35...
Page 662: ...ENGINE SPECIFICATIONS CONT 9 36 3 3L ENGINE...
Page 663: ...ENGINE SPECIFICATIONS CONT 3 3L ENGINE 9 37...
Page 664: ...ENGINE SPECIFICATIONS CONT 9 38 3 3L ENGINE...
Page 665: ...TORQUE 3 3L ENGINE 9 39...
Page 696: ...ENGINE SPECIFICATIONS 9 70 3 5L ENGINE...
Page 697: ...ENGINE SPECIFICATIONS CONT 3 5L ENGINE 9 71...
Page 698: ...ENGINE SPECIFICATIONS CONT 9 72 3 5L ENGINE...
Page 700: ......
Page 706: ...ENGINE DIAGNOSIS PERFORMANCE 9 6 ENGINE...
Page 707: ...ENGINE DIAGNOSIS MECHANICAL ENGINE 9 7...
Page 735: ...ENGINE SPECIFICATIONS 3 3L ENGINE 9 35...
Page 736: ...ENGINE SPECIFICATIONS CONT 9 36 3 3L ENGINE...
Page 737: ...ENGINE SPECIFICATIONS CONT 3 3L ENGINE 9 37...
Page 738: ...ENGINE SPECIFICATIONS CONT 9 38 3 3L ENGINE...
Page 739: ...TORQUE 3 3L ENGINE 9 39...
Page 770: ...ENGINE SPECIFICATIONS 9 70 3 5L ENGINE...
Page 771: ...ENGINE SPECIFICATIONS CONT 3 5L ENGINE 9 71...
Page 772: ...ENGINE SPECIFICATIONS CONT 9 72 3 5L ENGINE...
Page 774: ......
Page 786: ...TORQUE SPECIFICATION 11 12 EXHAUST SYSTEM AND INTAKE MANIFOLD...
Page 790: ...Fig 6 Engine Compartment Side View 13 4 FRAME AND BUMPERS...
Page 791: ...Fig 7 Forward Frame Section and Engine Cradle FRAME AND BUMPERS 13 5...
Page 792: ...Fig 8 Rear Frame Section 13 6 FRAME AND BUMPERS...
Page 809: ...Fig 40 Connecting Quick Connect Fittings to Fuel Rail FUEL DELIVERY 14 17...
Page 811: ...Fig 43 Chassis Fuel Tubes FUEL DELIVERY 14 19...
Page 840: ...3 3L FUEL INJECTOR DIAGNOSIS 14 48 FUEL INJECTION GENERAL DIAGNOSIS...
Page 841: ...3 5L FUEL INJECTOR DIAGNOSIS FUEL INJECTION GENERAL DIAGNOSIS 14 49...
Page 850: ...POWERTRAIN CONTROL MODULE 60 WAY CONNECTOR 14 58 FUEL INJECTION ON BOARD DIAGNOSTICS...
Page 874: ...SPECIFICATIONS TORQUE 14 82 FUEL INJECTION SERVICE PROCEDURES...
Page 876: ...DIAGNOSTIC TROUBLE CODE DESCRIPTION 14 2 FUEL SYSTEMS...
Page 877: ...DIAGNOSTIC TROUBLE CODE DESCRIPTION CONTINUED FUEL SYSTEMS 14 3...
Page 878: ...DIAGNOSTIC TROUBLE CODE DESCRIPTION CONTINUED 14 4 FUEL SYSTEMS...
Page 881: ...STEERING COMPONENTS SERVICE DIAGNOSIS POWER STEERING SERVICE DIAGNOSIS STEERING 19 3...
Page 882: ...POWER STEERING SERVICE DIAGNOSIS 19 4 STEERING...
Page 883: ...POWER STEERING SERVICE DIAGNOSIS STEERING 19 5...
Page 884: ...POWER STEERING SERVICE DIAGNOSIS 19 6 STEERING...
Page 885: ...POWER STEERING SERVICE DIAGNOSIS STEERING 19 7...
Page 886: ...POWER STEERING SERVICE DIAGNOSIS 19 8 STEERING...
Page 910: ...Fig 1 L H Platform Saginaw Tilt Steering Column 19 32 STEERING...
Page 924: ......
Page 929: ...DIAGNOSIS GUIDE VEHICLE WILL NOT MOVE TRANSAXLE 21 5...
Page 930: ...DIAGNOSIS GUIDE FLUID LEAKS 21 6 TRANSAXLE...
Page 931: ...DIAGNOSTIC TROUBLE CODE CHART A TRANSAXLE 21 7...
Page 932: ...DIAGNOSIS CHART B 21 8 TRANSAXLE...
Page 950: ...BACK UP LAMP DIAGNOSTIC CHART 21 26 TRANSAXLE...
Page 1010: ...DIAGNOSTIC TROUBLE CODE 12 DIAGNOSTIC TROUBLE CODE 13 21 86 TRANSAXLE...
Page 1011: ...DIAGNOSTIC TROUBLE CODE 14 DIAGNOSTIC TROUBLE CODE 15 TRANSAXLE 21 87...
Page 1012: ...DIAGNOSTIC TROUBLE CODE 16 DIAGNOSTIC TROUBLE CODE 17 21 88 TRANSAXLE...
Page 1013: ...DIAGNOSTIC TROUBLE CODE 18 DIAGNOSTIC TROUBLE CODE 19 TRANSAXLE 21 89...
Page 1014: ...DIAGNOSTIC TROUBLE CODE 20 21 90 TRANSAXLE...
Page 1015: ...DIAGNOSTIC TROUBLE CODE 21 27 TRANSAXLE 21 91...
Page 1016: ...DIAGNOSTIC TROUBLE CODE 28 21 92 TRANSAXLE...
Page 1017: ...DIAGNOSTIC TROUBLE CODE 29 DIAGNOSTIC TROUBLE CODE 31 32 TRANSAXLE 21 93...
Page 1018: ...DIAGNOSTIC TROUBLE CODE 36 DIAGNOSTIC TROUBLE CODE 35 21 94 TRANSAXLE...
Page 1019: ...DIAGNOSTIC TROUBLE CODE 37 DIAGNOSTIC TROUBLE CODE 38 TRANSAXLE 21 95...
Page 1020: ...DIAGNOSTIC TROUBLE CODE 41 44 21 96 TRANSAXLE...
Page 1021: ...DIAGNOSTIC TROUBLE CODE 45 DIAGNOSTIC TROUBLE CODE 46 TRANSAXLE 21 97...
Page 1023: ...DIAGNOSTIC TROUBLE CODE 50 58 TRANSAXLE 21 99...
Page 1024: ...DIAGNOSTIC TROUBLE CODE 60 62 21 100 TRANSAXLE...
Page 1025: ...42LE HYDRAULIC SCHEMATICS TRANSAXLE 21 101...
Page 1026: ...21 102 TRANSAXLE...
Page 1027: ...TRANSAXLE 21 103...
Page 1028: ...21 104 TRANSAXLE...
Page 1029: ...TRANSAXLE 21 105...
Page 1030: ...21 106 TRANSAXLE...
Page 1031: ...TRANSAXLE 21 107...
Page 1032: ...21 108 TRANSAXLE...
Page 1033: ...TRANSAXLE 21 109...
Page 1034: ...21 110 TRANSAXLE...
Page 1035: ...TRANSAXLE 21 111...
Page 1036: ...21 112 TRANSAXLE...
Page 1037: ...TRANSAXLE 21 113...
Page 1038: ...42LE SPECIFICATIONS 42LE FOUR SPEED AUTOMATIC TRANSAXLE 21 114 TRANSAXLE...
Page 1039: ...42LE TORQUE SPECIFICATIONS TRANSAXLE 21 115...
Page 1040: ...MASTER SHIM CHART 21 116 TRANSAXLE...
Page 1044: ...Fig 4 Tire Wear Patterns 22 4 WHEELS TIRES...
Page 1045: ...LEAD CORRECTION CHART LEAD CORRECTION CHART WHEELS TIRES 22 5...
Page 1053: ...AFTERMARKET PAINT REPAIR PRODUCTS BODY 23 5...
Page 1061: ...Fig 2 Sunroof Components BODY 23 13...
Page 1062: ...SUNROOF COMPONENT LEGEND 23 14 BODY...
Page 1100: ......
Page 1110: ...SUNROOF COMPONENT CALL OUTS 23 10 BODY...
Page 1111: ...Fig 2 Sunroof Components BODY 23 11...
Page 1119: ...A C PERFORMANCE TEMPERATURES HEATING AND AIR CONDITIONING 24 7...
Page 1147: ...DRB SCAN TOOL FLOW CHART MANUAL ATC HEATING AND AIR CONDITIONING 24 35...
Page 1148: ...DRB SCAN TOOL MENU BODY SECTION CLIMATE CONTROL ITEMS 24 36 HEATING AND AIR CONDITIONING...
Page 1149: ...DRB SCAN TOOL FLOW CHART SYSTEM TESTS HEATING AND AIR CONDITIONING 24 37...
Page 1150: ......
Page 1155: ...ENGINE VACUUM SCHEMATIC 3 3L ENGINE EMISSION CONTROL SYSTEMS 25 3...
Page 1156: ...ENGINE VACUUM SCHEMATIC 3 5L ENGINE 25 4 EMISSION CONTROL SYSTEMS...
Page 1165: ...EGR DIAGNOSIS CHART 3 3L ENGINE EMISSION CONTROL SYSTEMS 25 13...
Page 1170: ...ENGINE VACUUM SCHEMATIC 3 5L ENGINE 25 2 EMISSION CONTROL SYSTEMS...
Page 1172: ......
Page 1176: ......
Page 1180: ......
Page 1185: ...CONVERSION TABLES INTRODUCTION 5...
Page 1186: ...CONVERSION TABLES INTERNATIONAL CONTROL AND DISPLAY SYMBOLS 6 INTRODUCTION...
Page 1188: ......
Page 1190: ......
Page 1193: ...520 QVWDOODWLRQ QG 2SHUDWLRQ QVWUXFWLRQ RRNOHW...