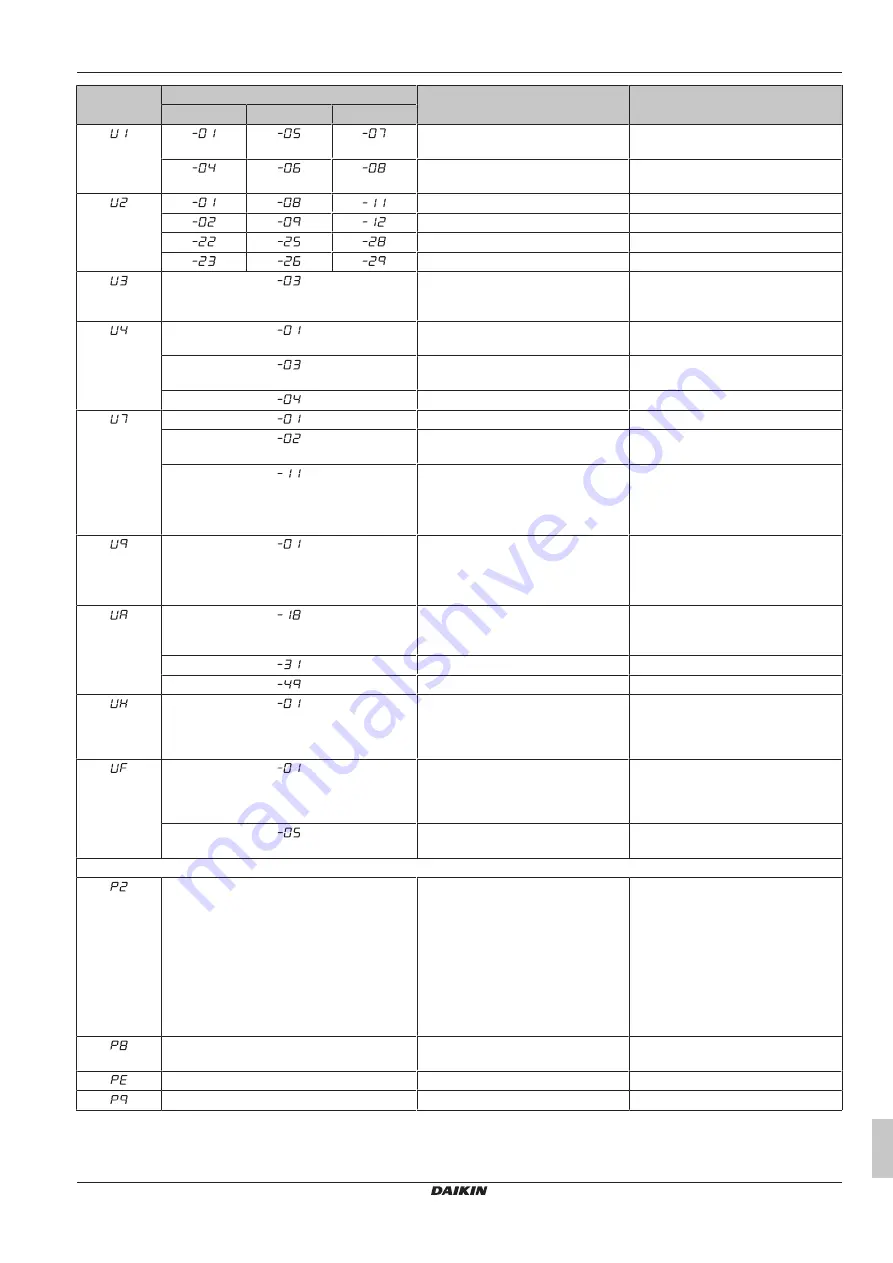
19 Troubleshooting
Installation and operation manual
41
RXYQQ8~20U7Y1B
VRV IV Q+ series heat pump
4P546221-1B – 2020.10
Main code
Sub code
Cause
Solution
Master
Slave 1
Slave 2
Reversed power supply phase
malfunction
Correct phase order.
Reversed power supply phase
malfunction
Correct phase order.
INV1 voltage power shortage
Check if power supply is within range.
INV1 power phase loss
Check if power supply is within range.
INV2 voltage power shortage
Check if power supply is within range
INV2 power phase loss
Check if power supply is within range.
Malfunction code: System test run not
yet executed (system operation not
possible)
Execute system test run.
Faulty wiring to Q1/Q2 or indoor -
outdoor
Check (Q1/Q2) wiring.
Faulty wiring to Q1/Q2 or indoor -
outdoor
Check (Q1/Q2) wiring.
System test run abnormal ending
Execute test run again.
Warning: faulty wiring to Q1/Q2
Check Q1/Q2 wiring.
Malfunction code: faulty wiring to Q1/
Q2
Check Q1/Q2 wiring.
▪ Too
many
indoor
units
are
connected to F1/F2 line
▪ Bad wiring between outdoor and
indoor units
Check indoor unit amount and total
capacity connected.
System mismatch. Wrong type of
indoor units combined (R410A,
R407C, RA, Hydrobox, etc)
Indoor unit malfunction
Check if other indoor units have
malfunction and confirm indoor unit
mix is allowed.
Connection malfunction over indoor
units or type mismatch (R410A,
R407C, RA, Hydrobox, etc)
Check if other indoor units have
malfunction and confirm indoor unit
mix is allowed.
Wrong unit combination (multi system) Check if unit types are compatible.
Wrong unit combination (multi system) Check if unit types are compatible.
Auto address malfunction
(inconsistency)
Check if transmission wired unit
amount matches with powered unit
amount (by monitor mode) or wait till
initialisation is finished.
Auto address malfunction
(inconsistency)
Check if transmission wired unit
amount matches with powered unit
amount (by monitor mode) or wait till
initialisation is finished.
Stop valve closed or wrong (during
system test run)
Open stop valves.
Auto charging related
—
Unusual low pressure on suction line
Close valve A immediately. Push BS1
to reset. Check following items before
retrying autocharge procedure:
▪ Check if the gas side stop valve is
opened correctly.
▪ Check if the valve of the refrigerant
cylinder is opened.
▪ Check if the air inlet and outlet of the
indoor unit are not obstructed.
—
Freeze-up prevention indoor unit
Close valve A immediately. Push BS1
to reset. Retry autocharge procedure.
—
Automatic charging nearly finished
Prepare for autocharge stopping.
—
Automatic charging finished
Finish autocharge mode.