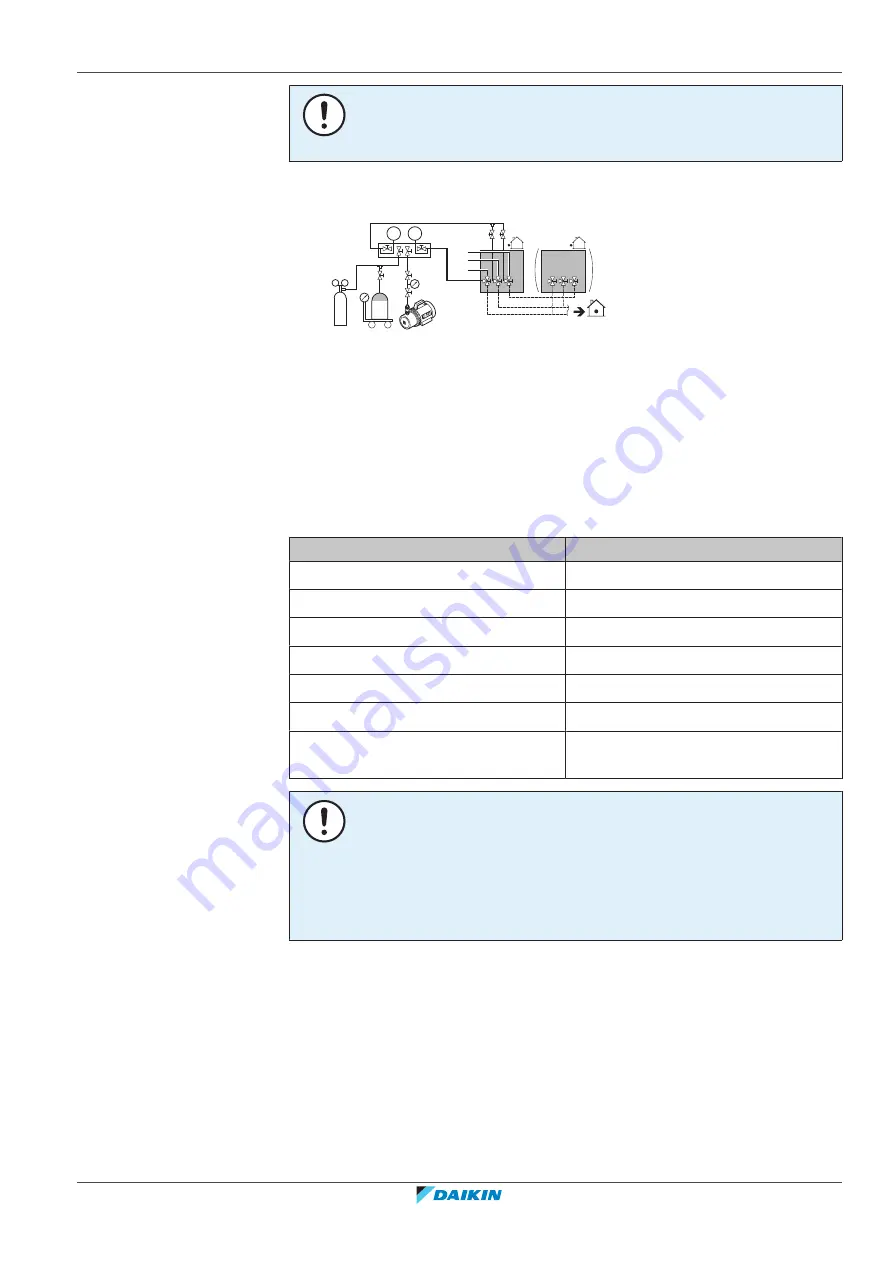
18
|
Piping installation
Installer and user reference guide
101
REMA5+REYA8~20A7Y1B
VRV 5 heat recovery
4P687640-1 – 2022.07
NOTICE
Do NOT purge the air with refrigerants. Use a vacuum pump to evacuate the
installation.
18.3.3 Checking refrigerant piping: Setup
p< p>
R32
N
2
C
D
b
c
e
a
g
h
f
d
A
B
a
Pressure reducing valve
b
Nitrogen
c
Weighing scales
d
Refrigerant R32 tank (siphon system)
e
Vacuum pump
f
Liquid line stop valve
g
Gas line stop valve
h
High pressure/low pressure gas line stop valve
A
Valve A
B
Valve B
C
Valve C
D
Valve D
Valve
State of valve
Valve A
Open
Valve B
Open
Valve C
Open
Valve D
Open
Liquid line stop valve
Close
Gas line stop valve
Close
High pressure/low pressure gas line
stop valve
Close
NOTICE
The connections to the indoor units and all indoor units should also be leak and
vacuum tested. Keep any possible (field supplied) field piping valves open as well.
Refer to the indoor unit installation manual for more details. Leak test and vacuum
drying should be done before the power supply is set to the unit. If not, see also the
flow chart earlier described in this chapter (see
18.3.4 To perform a leak test
The leak test must satisfy the specifications of EN378‑2.
To check for leaks: Vacuum leak test
1
Evacuate the system from the liquid and gas piping to –100.7 kPa (–1.007 bar)
(5 Torr absolute) for more than 2 hours.
2
Once reached, turn off the vacuum pump and check that the pressure does
not rise for at least 1 minute.