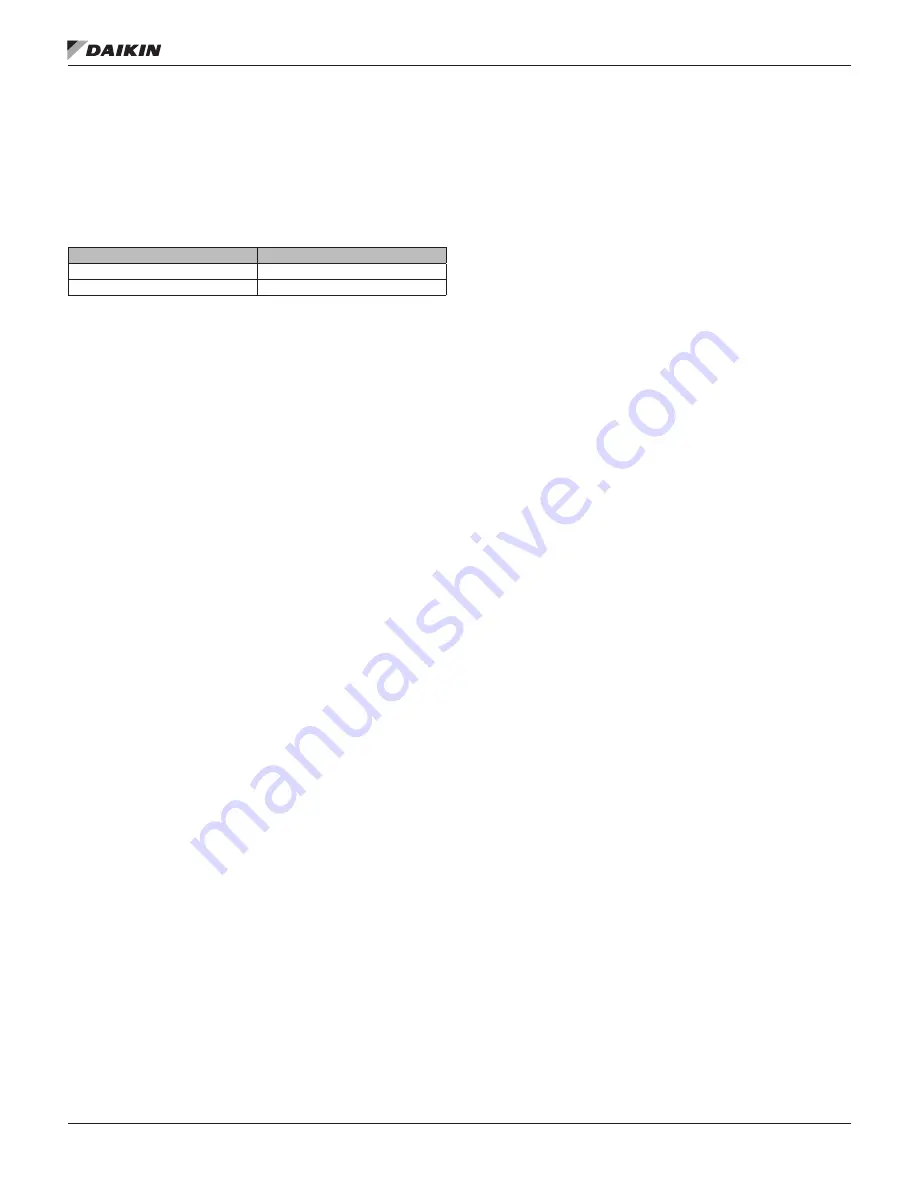
Daikin Applied EC Fan Array
www.DaikinApplied.com 39
IM 915-13 • VISION - EXTENDED SIZES
Fan Vibration Levels
Each unit as shipped is trim balanced to operate smoothly. To
provide satisfactory operation after shipping and installation,
use the accepted industry guidelines for field balancing fans.
.
Table 22: Vibration Levels
Fan speed (rpm)
Vibration
800 or less
5 mils maximum displacement
801 or greater
0.20 in/sec. maximum velocity
Note: Excessive vibration from any cause contributes to premature fan and motor bearing
failure. Monitor overall vibration levels every six months of operation. An increase in levels
is an indication of potential trouble.
Vibration Causes
1. Wheel imbalance
a. Dirt or debris on wheel blades
b. Loose set screws in wheel hub or bearing-to-shaft
c. Wheel distorted from overspeed
2. Bent shaft
3. Drive faulty
a.
Variable pitch sheaves—Axial and radial runout of
flanges; uneven groove spacing; out of balance.
Also similar faults in driven sheave.
b. Bad V-belts; lumpy, or mismatched; belt tension
too tight or too loose.
4. Bad bearings, loose bearing hold-down bolts
5. Motor imbalance
6. Fan section not supported evenly on foundation
Summary of Contents for Vision
Page 55: ......