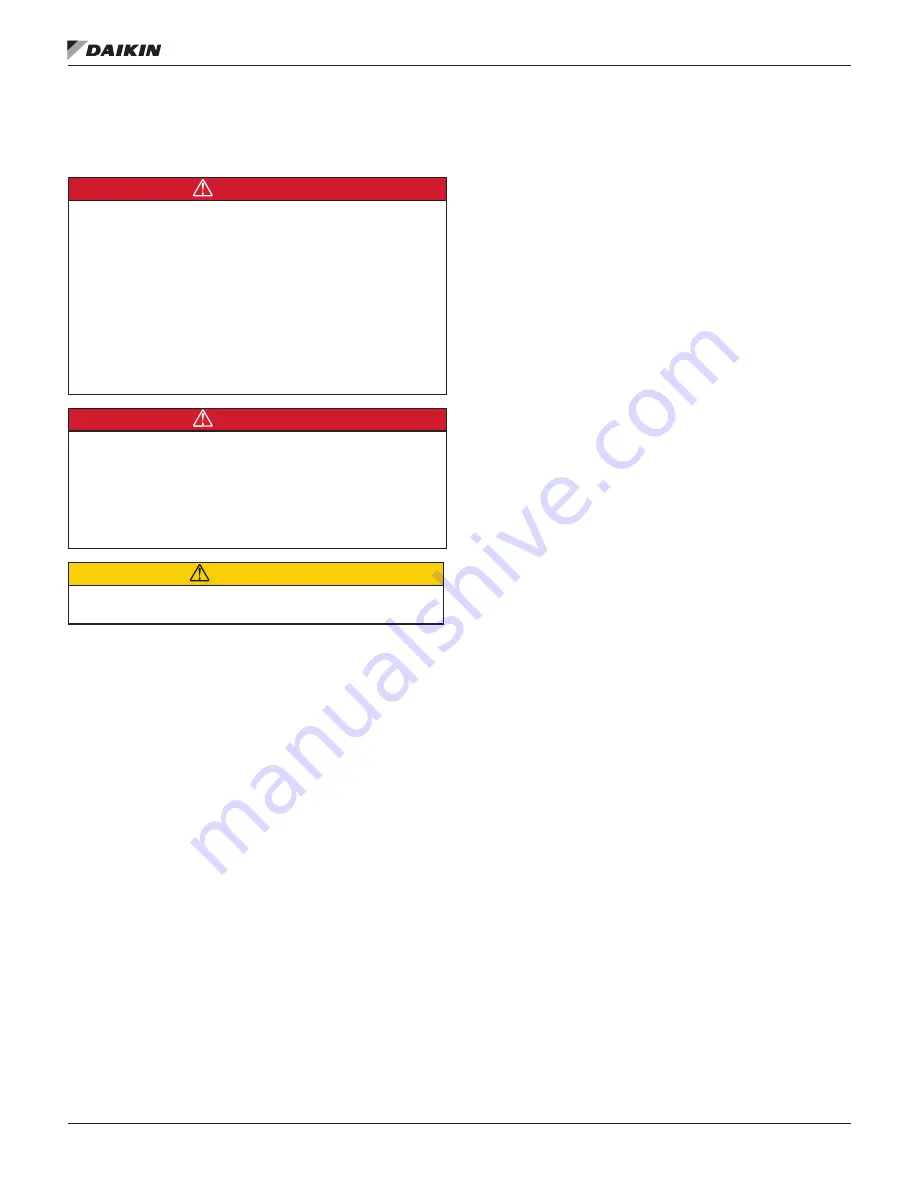
Electrical Installation
www.DaikinApplied.com 23
IM 915-13 • VISION - EXTENDED SIZES
Electrical Installation
Wiring
DANGER
Capacitor Hazardous Voltage!
Failure to disconnect power
and discharge capacitors before servicing will result in serious
injury or death.
Disconnect all electric power (including remote disconnects)
before servicing. Perform lockout/tagout procedures to ensure
that power can not be energized. For variable frequency
drives, or other energy storing components that have been
furnished and mounted by either Daikin Applied, or by others,
refer to the specific manufacturer’s literature for allowable
waiting periods for discharge of capacitors. Verify capacitors
have been discharged using an appropriate voltmeter.
DANGER
• This equipment is not suitable for use in high impedance
grounding or neutral systems.
• Connect only to low impedance, solidly grounded electrical
supply systems.
Failure to follow these instructions will result in death or
serious injury.
CAUTION
Use copper conductors only!
Failure to use copper
conductors can result in equipment damage.
• Electrical service to each fan must correspond to the
rated voltage on the motor or electrical panel nameplate
and conform to the National Electric Code and local
restrictions.
• Connect each fan section metal frame to the building
electrical ground.
• A door electrical interlock is not provided as standard.
• Thermal motor protection is external to the unit. Unless
the unit is provided with a variable frequency drive
(VFD) or a unit mounted starter, thermal protection and
a disconnect switch provision per electric codes are
provided by others.
• When the unit is factory provided with a disconnect
switch, starter or a variable frequency drive (VFD), the
components are mounted on the outside of the unit
cabinet. Factory wiring is provided from the device to the
unit internal motor.
• All electrical components must be grounded to the
building central ground. Suitable ground wires and/or
(bonding) lugs are provided for all motors, disconnect
switches, starters, and variable frequency drives. Provide
dedicated ground (bonding) copper conductors in
accordance with local and national codes.
• For units provided with a motor only or with an external
junction box, wire connections are made with suitable
wire nuts or connectors for the gauge wires provided.
•
For units provided with a disconnect switch or starter, field
wiring will be terminated to lugs. Wire size and lug torque
requirements are shown on the unit electrical schematic
provided in the component print pocket. All power supply
wire connections must be torqued as shown.
• When the unit is provided with a VFD only, refer to the
VFD manual for wire size and torque requirements. For
instances where multiple motors are being driven by a
single VFD, be sure to set up the VFD and size the wiring
according to the power requirements of all motors that
are being driven by that VFD.
• When not being serviced, close and secure electrical
panel doors to prevent ingress of moisture and airborne
contaminants.
Control Wiring
• Access to the VFD is through the fan cabinet access door
for single fans. Provide shielded cable only as described
in the provided VFD manual. Route wire through the
interfere with other components or access doors. Do
not drill through drip pans or drain pans. Refer to the
provided VFD installation manual for detailed control
wiring instructions.
• For multiple fans in parallel, the VFD(s) are mounted
inside of the electrical enclosure, which is mounted
on the exterior of the fan section. When multiple fan
sections are provided with multiple VFDs, they must be
set up so that the fans always start simultaneously and
are set to ramp up and down together. Do not attempt
to run fans in parallel at different speeds as this can
result in uneven airflow that can cause performance,
sound, and vibration problems that can lead to failure.
Provided that the fan is capable of running fast enough,
the motor is sized appropriately, and the VFD can be
sped up within its rated continuous output, VFDs may
be operated up to a maximum recommended frequency
of 90 Hertz for 1800 RPM and slower motors. Motors
that are 3600 RPM may be operated up to a maximum
speed of 4000 RPM or 66.7 Hertz provided the fan is
rated that high. Operation above 4000 RPM can damage
motor bearings and is not recommended.
Wiring Penetrations
• Seal any panel penetrations for wiring or conduit per the
panel cutting procedure instructions within this document.
• Seal any other wiring or conduit penetrations in
accordance with NEC, relevant codes, and in order to
maintain the enclosure rating, only use fittings that are
approved to keep the particular rating of the individual
enclosure being penetrated per relevant code or standard
tables. Seal wireway openings tight enough to prevent air
movement between sections and control enclosures.
Summary of Contents for Vision
Page 55: ......