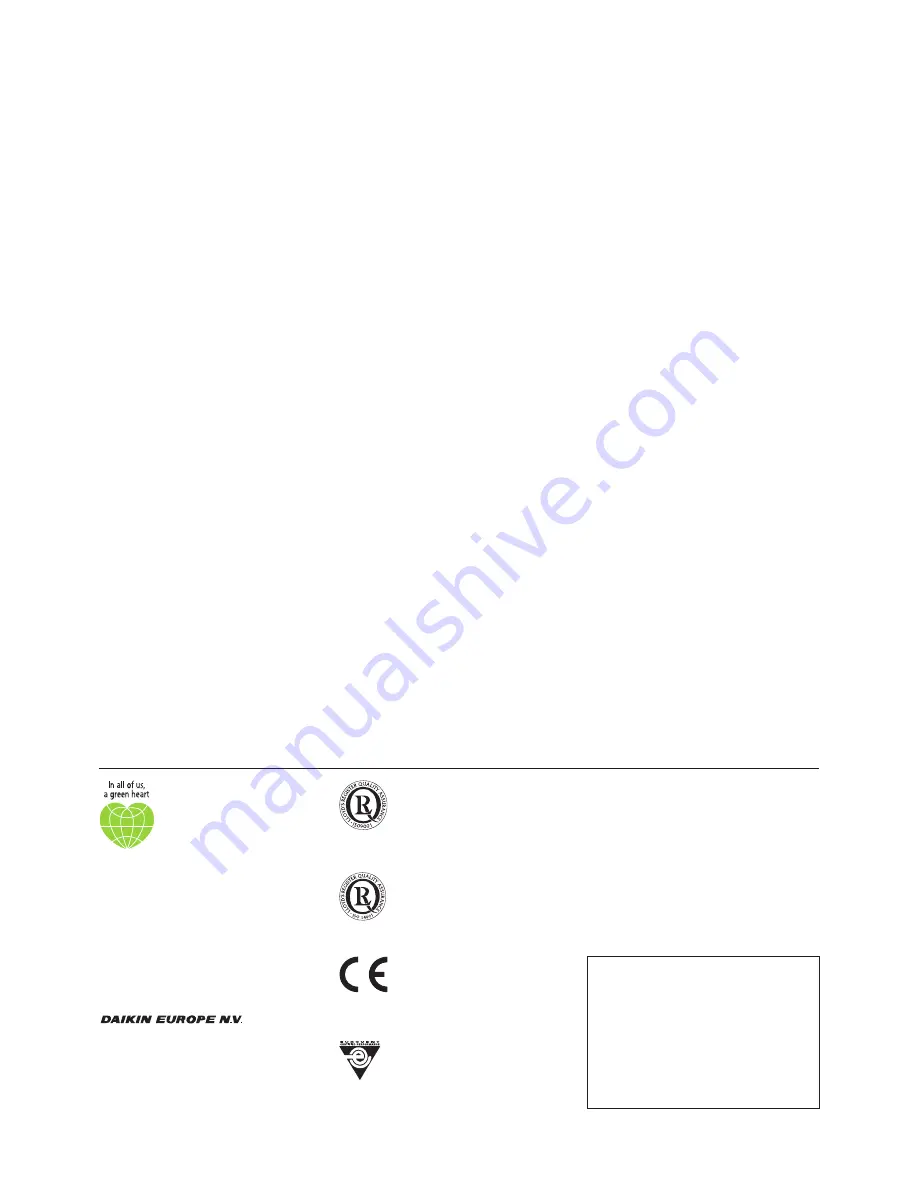
q<R.7+. !H,st
ISO14001 assures an effective environmental
management system in order to help protect human health
and the environment from the potential impact of our
activities, products and services and to assist in
maintaining and improving the quality of the environment.
Daikin Europe N.V. is approved by LRQA for its Quality
Management System in accordance with the ISO9001
standard. ISO9001 pertains to quality assurance regarding
design, development, manufacturing as well as to services
related to the product.
Daikin units comply with the European regulations that
guarantee the safety of the product.
Si
E
N
B
E
07
-618
_C
•
02
/20
11
• C
opyr
ight
D
ai
ki
n
Prep
ared i
n Bel
gium
by
Lan
noo
(w
ww.l
anno
oprin
t.be),
a co
mpa
ny wh
ose
con
cern
for
the
env
iron
mon
t is
se
t in t
he EM
AS
and I
S
O
14
001
sy
stem
s.
Res
pons
ibl
e Edi
tor: Dai
kin
Europe
N.V., Zan
dvo
ordes
traa
t 300
, B- 840
0 Ooste
nde
"The present publication is drawn up by way of information only and does
not constitute an offer binding upon Daikin Europe N.V.. Daikin Europe N.V.
has compiled the content of this publication to the best of its knowledge. No
express or implied warranty is given for the completeness, accuracy,
reliability or fitness for particular purpose of its content and the products and
services presented therein. Specifications are subject to change without
prior notice. Daikin Europe N.V. explicitly rejects any liability for any direct or
indirect damage, In the broadest sense, arising from or related to the use
and/or interpretation of this publication. All content is copyrighted by Daikin
Europe N.V.."
Daikin’s unique position as a manufacturer of air
conditioning equipment, compressors and
refrigerants has led to its close involvement in
environmental issues. For several years Daikin has
had the intension to become a leader in the provision
of products that have limited impact on the
environment. This challenge demands the eco design
and development of a wide range of products and an
energy management system, resulting in energy
conservation and a reduction of waste.
Daikin Europe N.V. is participating in the EUROVENT
Certification Programme. Products are as listed in the
EUROVENT Directory of Certified Products.
Naamloze Vennootschap
Zandvoordestraat 300
B-8400 Oostende - Belgium
www.daikin.eu
BE 0412 120 336
RPR Oostende
SIENBE07-618_C_FRONT.pdf 149
9/02/2011 9:25:12