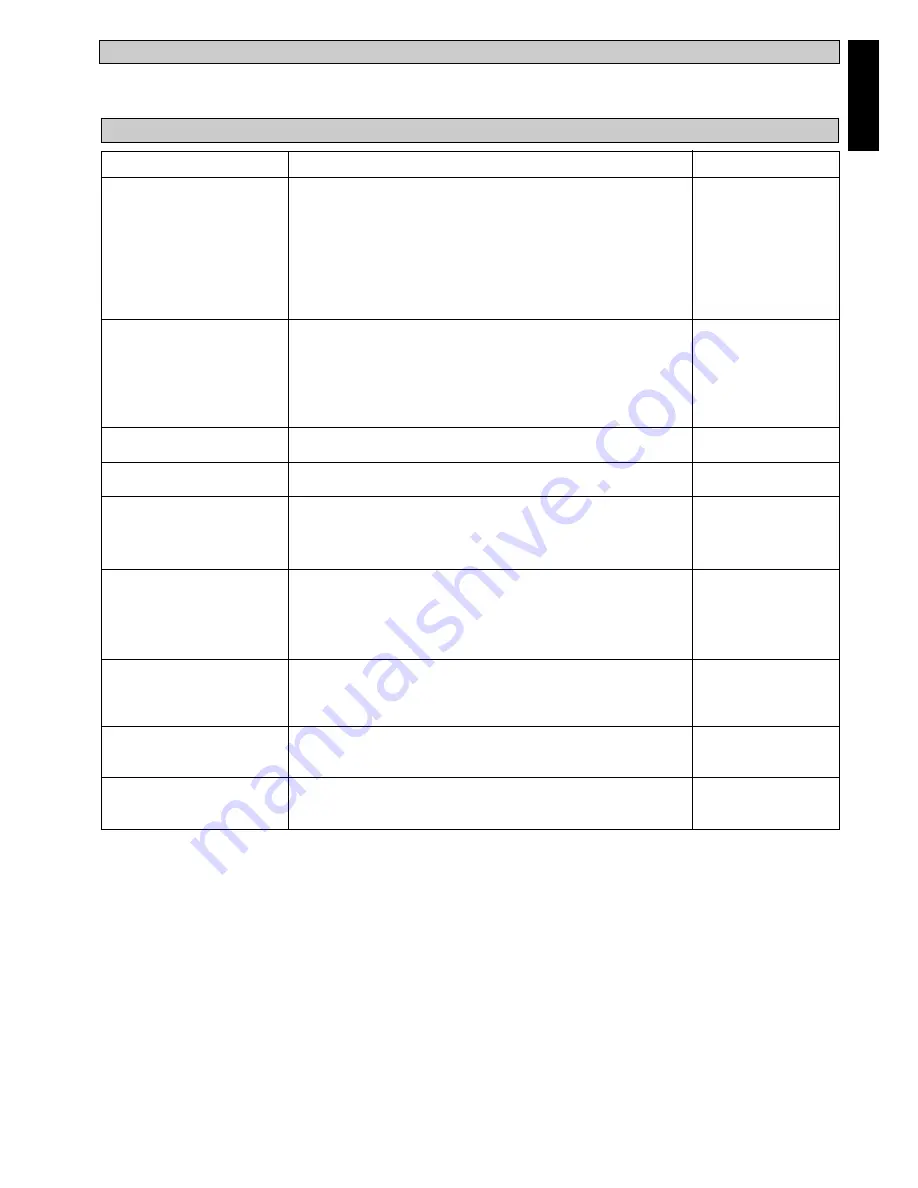
11
English
Maintenance Procedures
1. Remove any dust adhered on the filter by using a vacuum
cleaner or wash in lukewarm water (below 40°C) with neutral
cleaning detergent.
2. Rinse well and dry the filter before placing it back onto the
unit.
3. Do not use gasoline, volatile substances or chemical to clean
the filter.
1. Clean any dirt or dust on the grille or panel by wiping it using
soft cloth soaked in lukewarm water (below 40°C) with
neutral detergent solution.
2. Do not use gasoline, volatile substances or chemical to clean
the indoor unit.
1. Check its cleanliness and clean it if necessary.
1. Check for any abnormal noise.
1. Check and remove any dirt clogged between the fins.
2. Check and remove any obstacles that hinder air flowing into
and out of the indoor/outdoor unit.
1. Check the voltage and current of the indoor and outdoor unit.
2 Check the electrical wiring for any faulty contacts caused by
loose connections, foreign matters, etc. Tighten the wires onto
the terminal block if necessary.
1. No maintenance needed if the refrigerant circuit remain sealed.
However, check for any refrigerant leaks at all joints and
fitting.
1. The compressor oil is factory-precharged. It is not necessary
to add any oil if the circuit remains sealed.
1. All motor pre-lubricated and sealed at factory.
Period
At least once
every 2 week.
More frequently if
necessary.
At least once
every 2 weeks.
More frequently if
necessary.
Every 3 months.
When necessary.
Every month.
Every month.
Every 2 months.
Every 2 months.
Every 6 months.
No maintenance
required.
No maintenance
required.
Service Parts
Indoor Air Filter
Indoor Unit
Condense Drain Pan & Pipe
Indoor Fan
Indoor/Outdoor Coil
Power Supply
Compressor
Compressor Oil
Fan Motor Oil
SERVICE AND MAINTENANCE
AUTO RANDOM RE-START FUNCTION
If there is a power cut when the unit is operating, it will automatically resume the same operating mode when the power is restored.
(Applicable only to units with this feature).