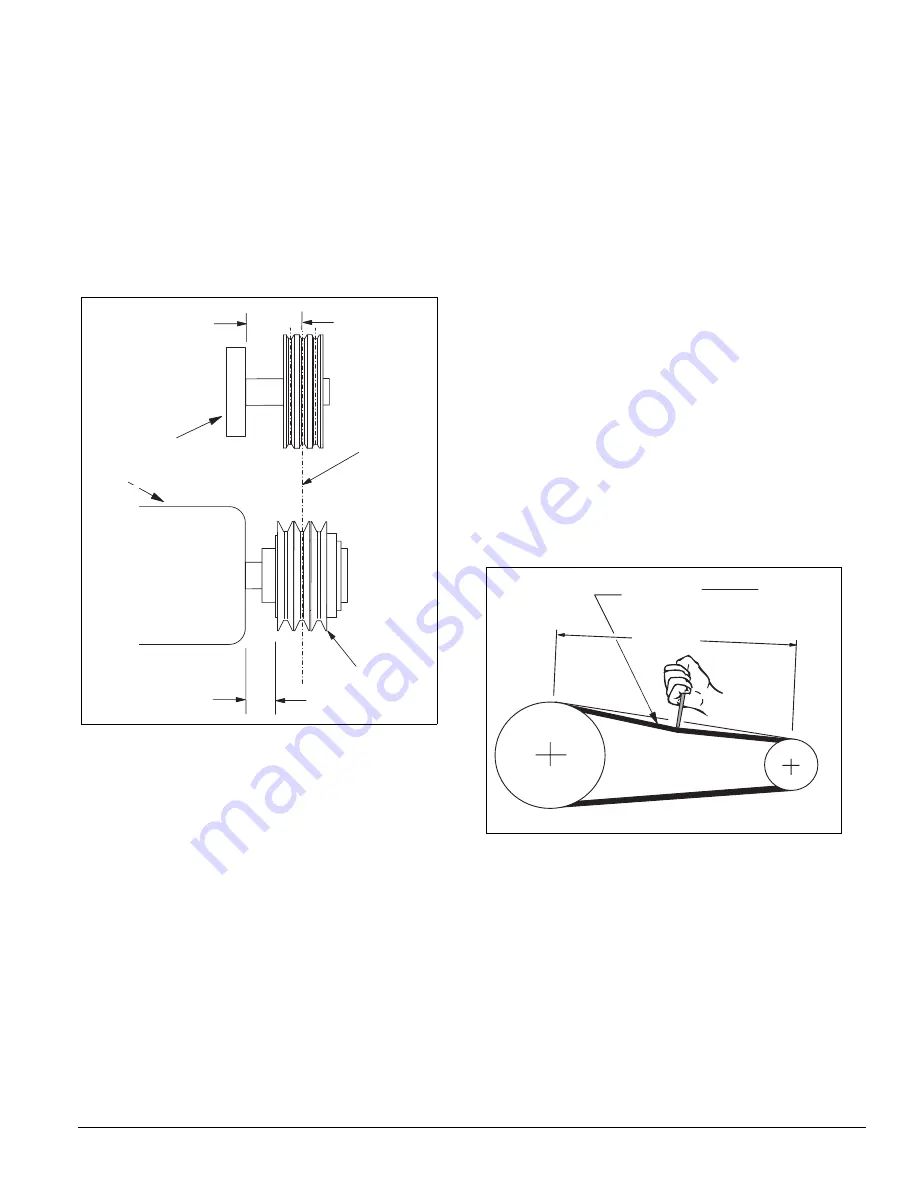
IM 738-2
105
Check, Test, and Start Procedures:
Sheave Alignment
Sheave Alignment
Mounting:
1
Verify both driving and driven sheaves are in alignment and
the shafts are parallel. The center line of the driving sheave
must be in line with the ce1nter line of the driven sheave.
See Figure 107.
2
Verify that all setscrews are torqued to the values shown in
Table 28 on page 115 before starting drive. Check setscrew
torque and belt tension after 24 hours of service.
Figure 107. Sheave alignment (adjustable shown)
Drive Belt Adjustment
General Rules of Tensioning
1
The ideal tension is the lowest tension at which the belt will
not slip under peak load conditions.
2
Check tension frequently during the first 24–
3
48 hours of operation.
4
Over tensioning shortens belt and bearing life.
5
Keep belts free from foreign material which may cause
slippage.
6
Make V-drive inspection on a periodic basis. Adjust tension
if the belt is slipping. Do not apply belt dressing. This may
damage the belt and cause early failure.
Tension Measurement Procedure
1
Measure the belt span. See
2
Place belt tension checker squarely on one belt at the center
of the belt span. Apply force to the checker, perpendicular
to the belt span, until the belt deflection equals belt span
distance divided by 64. Determine force applied while in
this position.
3
Compare this force to the values on the drive kit label
found on the fan housing.
Figure 108. Drive belt adjustment
e n t e r l i n e s
m u s t c o i n c i d e
M u s t b e
p a r a l l e l
M u s t b e
p a r a l l e l
A d j u s t a b l e
S h e a v e
M o t o r
B e a r i n g
B e l t S p a n
D e f l e c t i o n = B e l t S p a n
6 4
Summary of Contents for RDT-135c
Page 131: ...IM 738 2 129...