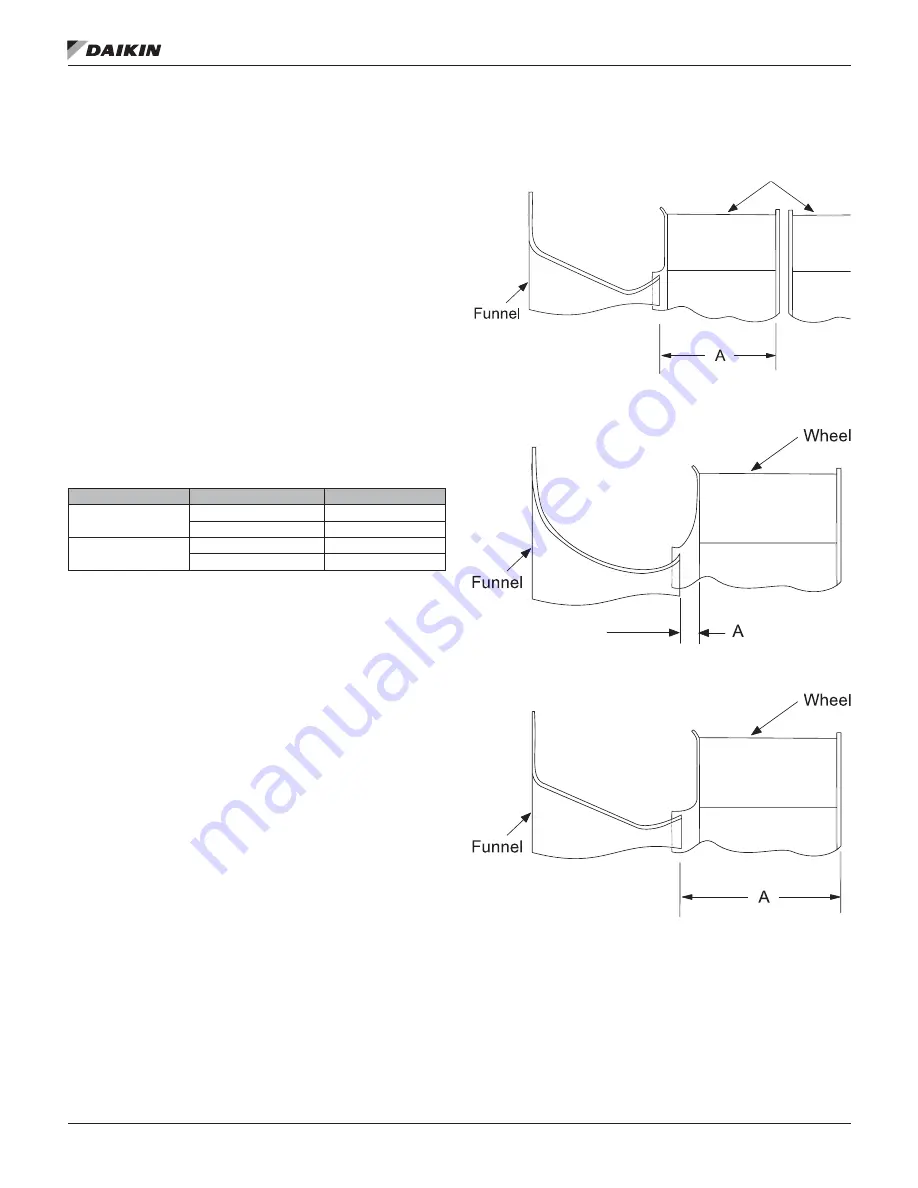
Maintenance
www.DaikinApplied.com 99
IM 991-2 • MAVERICK II ROOFTOP
Supply Fan Wheel-to-Funnel Alignment
If the unit is equipped with an airfoil or backward curved
supply fan, the fan wheel-to-funnel alignment must be as
shown in
and
proper air delivery and operating clearance. If necessary,
adjustments are made as follows:
1.
Verify that the fan shaft has not moved in its bearings.
2.
Loosen the fan hub setscrews and move the wheel(s)
along the shaft as necessary to obtain the correct
dimension shown in
3.
Retighten the setscrews to the torque specification
given in
. Tighten the setscrews
over the keyway first; tighten those at 90 degrees to the
keyway last.
4.
Verify that the radial clearance around the fan is uniform.
Radial clearance can be adjusted by slightly loosening
the funnel hold-down fasteners, shifting the funnel as
required, and retightening the fasteners.
Table 18: Wheel-to-Funnel Relationship
Fan Type
Wheel diameter (inches)
A
DWDI Airfoil
30
10.6 (+0.3–0.0)
33
11.7 (+0.3–0.0)
SWSI Airfoil
40
0.62
44
16.21
Figure 77: DWDI Airfoil Wheel-to-Funnel Alignment
Figure 78: 40" SWSI Airfoil Wheel-to-Funnel Alignment
Figure 79: 44" SWSI Airfoil Wheel-to-Funnel Alignment
Wheels