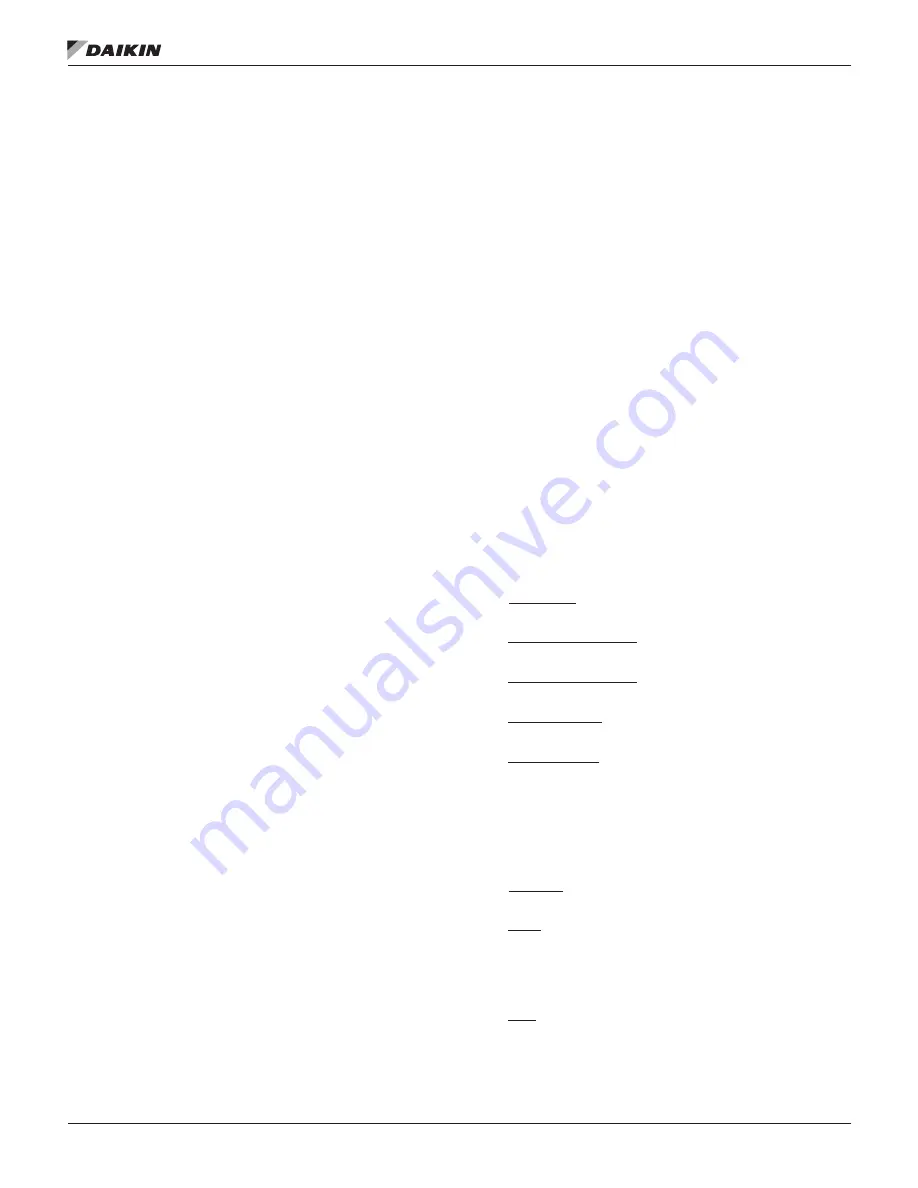
o
peraTIon
IOM 1210-1 • MAGNITUDE
®
MODEL WMC CHILLERS
20 www.DaikinApplied.com
o
peraTIon
Operator Responsibilities
It is important that the operator become familiar with the
equipment and the system before attempting operation. During
the initial startup of the chiller, the Daikin Applied technician will
be available to answer any questions and instruct the proper
operating procedures. It is recommended that the operator
maintain an operating log for each individual chiller unit. In
addition, a separate maintenance log should be kept of the
periodic maintenance and servicing activities.
Operator Schools
Training courses for Magnitude
®
Centrifugal Maintenance and
Operation are held through the year at the Daikin Learning
Institute in Staunton, Virginia. The school duration is three and
one-half days and includes instruction on basic refrigeration,
MicroTech
®
II controllers, enhancing chiller efficiency and
reliability, MicroTech
®
II troubleshooting, system components,
and other related subjects. For more information, visit us
at
www.DaikinApplied.com
and click on Training or call the
Training Department. Refer to the back cover of this document
for contact information.
Sequence of Unit Operation
The following is a general chiller sequence of operation for
Magnitude
®
Model WMC chillers. Certain conditions and chiller
alarms may alter this sequence, but the chiller’s objective is to
achieve the target temperature of the leaving water.
1.
Chiller enabled
With the chiller enabled via its onboard interlocks
and selected external control source, it will start the
evaporator pump and check for flow and chiller load.
2.
Water flow and load proven
Once evaporator flow has been confirmed and the
chiller load proven, compressor wear balancing logic will
determine which compressor to start as the Lead.
3.
Lead compressor start
As the Lead compressor approaches its maximum
capacity it will assess the need for the Lag compressor.
If the Lag compressor is needed, the Lead compressor
will signal the Lag compressor to start, and may adjust its
capacity to assist the Lag compressor start.
4.
Lag compressor start
Once started, the Lag compressor will quickly ramp up to
balance the chiller load between the two compressors.
5.
Dual compressor loading
As building load increases, the compressors will load
up maximizing the Inlet Guide Vane (IGV) position and
impeller speed. Maximum capacity at a given operating
condition can be found either when the compressors
have reached their maximum speed limit (Mechanical
limitation) or when the compressors have reached the
chiller’s Rated Load Amperage (Electrical limitation).
6.
Dual compressor unloading
As load decreases, the compressors will unload to
sustain the water temperature set point by reducing
speed until the minimum speed limit has been reached.
If further unloading is required, the IGV assemblies will
close as required to satisfy the load.
7.
Staging down to one compressor running
With the chiller running two compressors on condition
and the building load reducing to the point that one
compressor can carry the load, compressor wear
balancing logic will again determine which compressor to
shutdown.
8.
Chiller shutdown
The remaining compressor will adjust capacity to
manage the chiller load until the load increases to the
point where another compressor is needed, or the load
reduces below the minimum capacity of one compressor
and the leaving water temperature goes below set point
and reaches the stop delta temperature. Anytime the
chiller is disabled, it will perform an orderly unload and
shutdown both compressors.
Unit Enabling/Disabling
There are multiple switches that will enable and disable the
chiller and its compressors:
1. Unit Switch - The top switch on the switch bracket that is
mounted inside the control box.
2. Compressor 1 Switch - Located underneath the Unit
Switch on the switch bracket.
3. Compressor 2 Switch - Located underneath the
Compressor 1 Switch on the switch bracket.
4. External Switch - Located on the outer, left side of the
control box.
5. Remote Switch - Optional. Replaces a jumper between
Field Terminals 54 and 70 (see
"Figure 12: Wiring Index"
on page 12
).
The switches listed above work in conjunction with the “Control
Source” that is selected in the OITS via the MODES Setpoint
Screen using Setpoint button #3. (See
Figure 44
and
Table 10
on
page 38
.) The three options for “Control Source” are:
1. Switches - This is the default mode. This mode will
ignore BAS commands.
2. Local - When this mode is set, a STOP button and an
AUTO button will appear at the top of the OITS screens,
as shown in
Figure 16 on page 22
.
This mode will
ignore all functionality of a connected Remote
Switch
. It will also ignore BAS commands.
3. BAS - This mode adds BAS capability to the Switches
functionality.
Enabling and disabling the unit and its compressors using the
switches in conjunction with the selected “Control Source” are
discussed next.