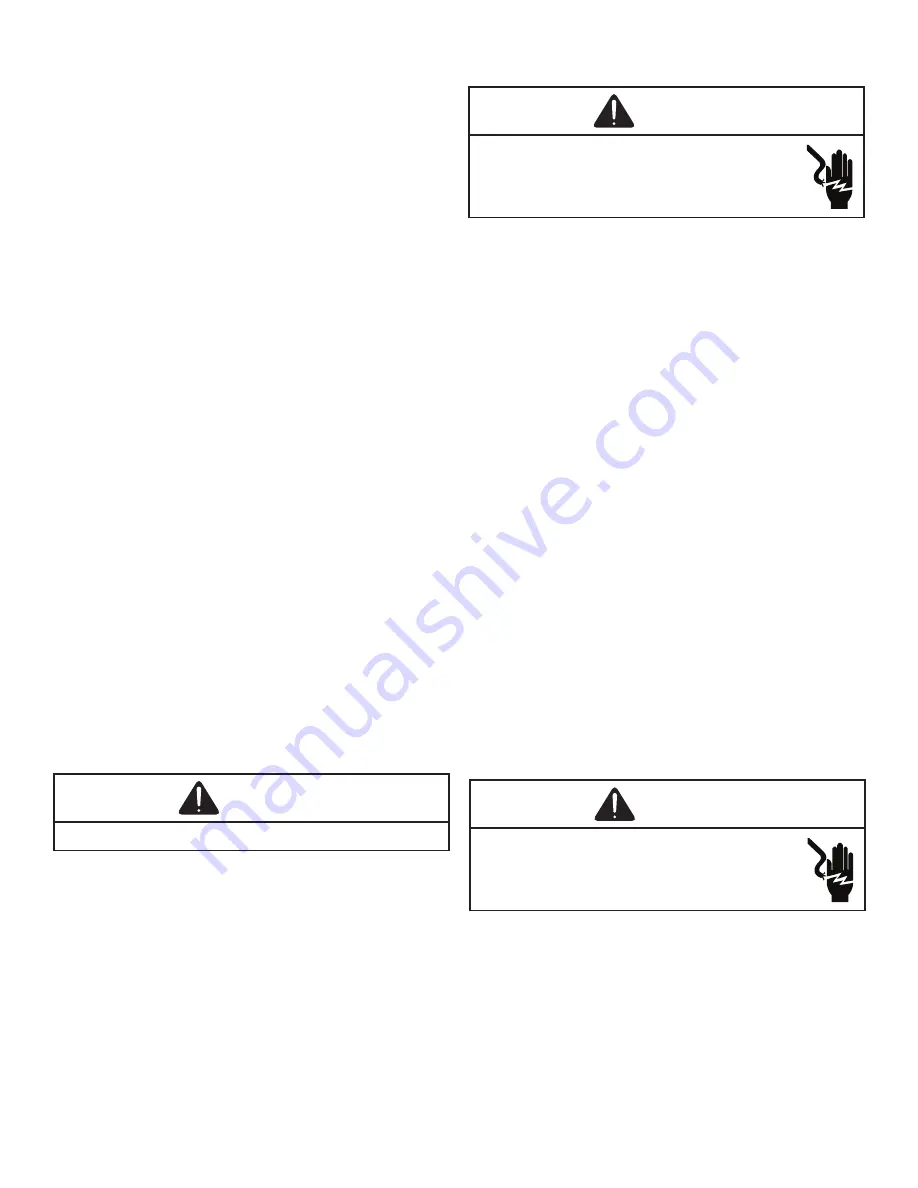
SERVICING
37
LED on the control flashes “4” to indicate an open limit
switch. The blower and inducer remain on while the limit
switch is open. The gas valve is de-energized. Power to
the thermostat “R” is removed while the limit switch is open.
When the limit switch re-closes, the induced draft motor
runs through its post purge and the indoor blower goes
through the heat off delay.
If a call for heat exists when the limit switch re-closes, the
control goes through a pre-purge period and then makes
an ignition attempt. The indoor blower remains on (for the
delay off time) during the re-ignition attempt.
1. If no voltage is measured on either side of control it
indicates ignition control or wiring to control problem.
2. If voltage is measured on one side of the control and
not the other, it indicates the control is open.
3. If voltage is measured on both sides of the control
the wiring to gas valve or valve is at fault.
Servicing procedure with furnace not firing.
1.
Confirm that the outer door was in place and all
screws tightened. (No leaks under the door.)
2. Check to see if any damage was done to the furnace
especially the wiring.
3.
Confirm that heat exchanger is not obstructed by
feeling for discharge air from the flue hood when the
combustion blower is running but the unit is not firing.
If the above steps do not suggest the reason the control
has tripped the furnace should be fired.
1. Remove the heating compartment door.
2. Turn of the power or open the thermostat circuit.
3. Reset the rollout control.
4. Turn power on and put the unit into a call for heating.
CAUTION
Flame rollout could occur. Keep face and hands a safe
distance from burner area.
5. Look under the heat shield as the unit is running.
Flames should be drawn into firing tubes.
A.
If only one burners flame is not drawn into the
tube, that tube is restricted.
B. If, without the air circulation blower running, all
flames are not drawn into the tubes either the
collector box, combustion blower, or flue outlet
is obstructed. If the combustion blower or flue
outlet is obstructed, the pressure switch should
have opened preventing the unit from firing, also
inspect the unit pressure switch and wiring.
C.
If the burner flame is not drawn into the tube only
when the air circulation blower is running, then a
cracked heat exchanger tube is present.
Testing Inducer Motor
WARNING
High Voltage!
Disconnect all power before servicing or
installing. Multiple power sources may be present.
Failure to do so may cause property damage,
personal injury or death.
1. Disconnect the motor wire leads from its connection
point at integrated ignition control module.
2. Using and ohmmeter, test for continuity between
each of the motor leads.
3. Touch one probe of the ohmmeter to the motor frame
(ground) and the other probe in turn to each lead.
If the windings do not test continuous or a reading is
obtained to ground, replace the motor.
4. After completing check and/or replacement of
induced draft blower motor.
5. Turn on electrical power and verify proper unit
operation.
Testing Gas Valve
Direct Spark Ignition (DSI) Systems
A combination redundant operator type gas valve which
provides all manual and automatic control functions
required for gas fired heating equipment is used on single
stage models.
A two-stage combination redundant operator type gas valve
which provides all manual and automatic control functions
required for gas fired heating equipment is used on two
stage models.
The valve provides control of main burner gas flow,
pressure regulation, and 100 percent safety shut-off.
WARNING
High Voltage!
Disconnect all power before servicing or
installing. Multiple power sources may be present.
Failure to do so may cause property damage,
personal injury or death.
1. Ensure gas valve and main gas supply are on.
2. Using a voltmeter, check for 24 volts as noted below
for 1- and 2- stage gas valves.
3.
If 24 volts are present and no gas flows through the
valve, replace valve.