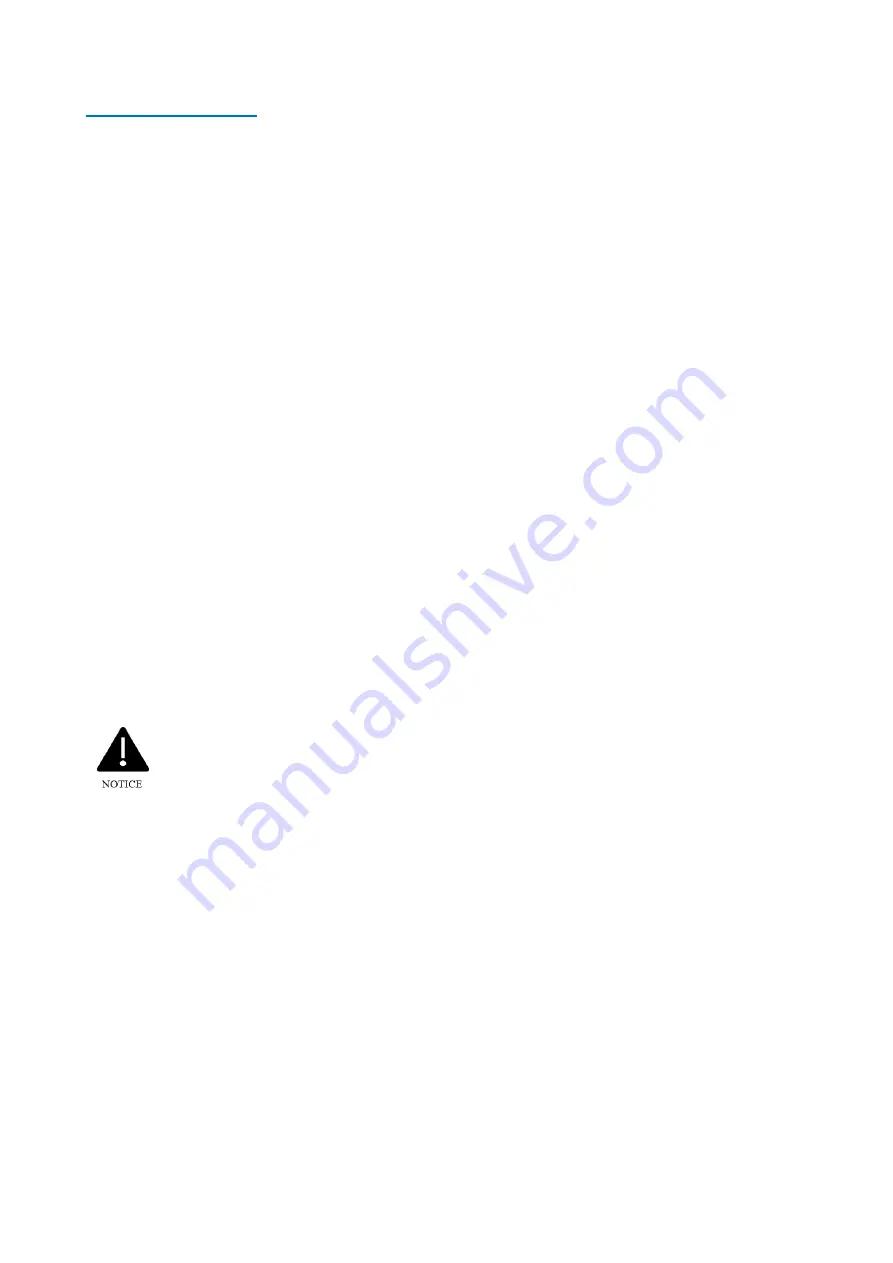
T-CU11-OCT22-0
Page 19
Commissioning
Pre startup checks
Before starting the condensing unit, the following checks should be carried out as a minimum:
•
Check electrical supply is correct and all connections are sound.
•
All moving parts are free, and guards fitted.
•
Check all mechanical connections for tightness
•
Compressor oil level satisfactory for model with oil sight glass.
•
Overload relay set correctly.
•
All valves in correct operating position.
•
Initial refrigerant charge.
•
Initial settings for low pressure switch
–
default settings from factory specified in
•
Crankcase heater (not provided) energized for a minimum of 12 hours before compressor first start-up.
•
Gauge manifold connected to both low and high sides of system.
Running the Unit
•
Run the unit and check compressor and condenser fan operation.
•
Check system pressures and temperatures, liquid line sight glass, charge and running currents of motors to
ensure correct operation.
•
Check compressor suction superheat. This should be between 10K and 20K at normal operating conditions.
•
Final adjustment of low-pressure switch.
•
Allow the system to run for 3
–
4 hours. Check compressor oil level and top up with the correct oil type as
. Recheck the compressor oil level again after 24 hours operation.
•
Carry out final leak test and ensure all panels/covers are fitted and screws tightened.
•
Log all information along with the system model and serial numbers for future reference.
•
Ensure that the customer / responsible person is provided with basic operating instructions and where
electrical isolators are situated in case of emergency.
There must be no more than 10 compressor starts per hour. A higher number reduces
the service life of the compressor and can cause carry-over of oil into the system. If
necessary, use an anti-short-cycle timer in the control circuit. A minimum 3 minutes
runtime after each start of the compressor and a 3 minutes idle time after each stop
are recommended. Only during the pump down cycle may the compressor run for much shorter
intervals.
System Operation
Once the system is correctly charged with refrigerant and the operating condition is stable, check that the compressor
suction superheat is between 10~20K and that the compressor discharge temperature is between 50°C ~ 90°C. A
suction superheat that is too low may indicate liquid refrigerant return to the compressor, whereas a suction superheat
that is too high will not provide enough cooling effect for the compressor and will also cause high discharge
temperatures. In either case, it is likely that compressor damage/failure will occur.