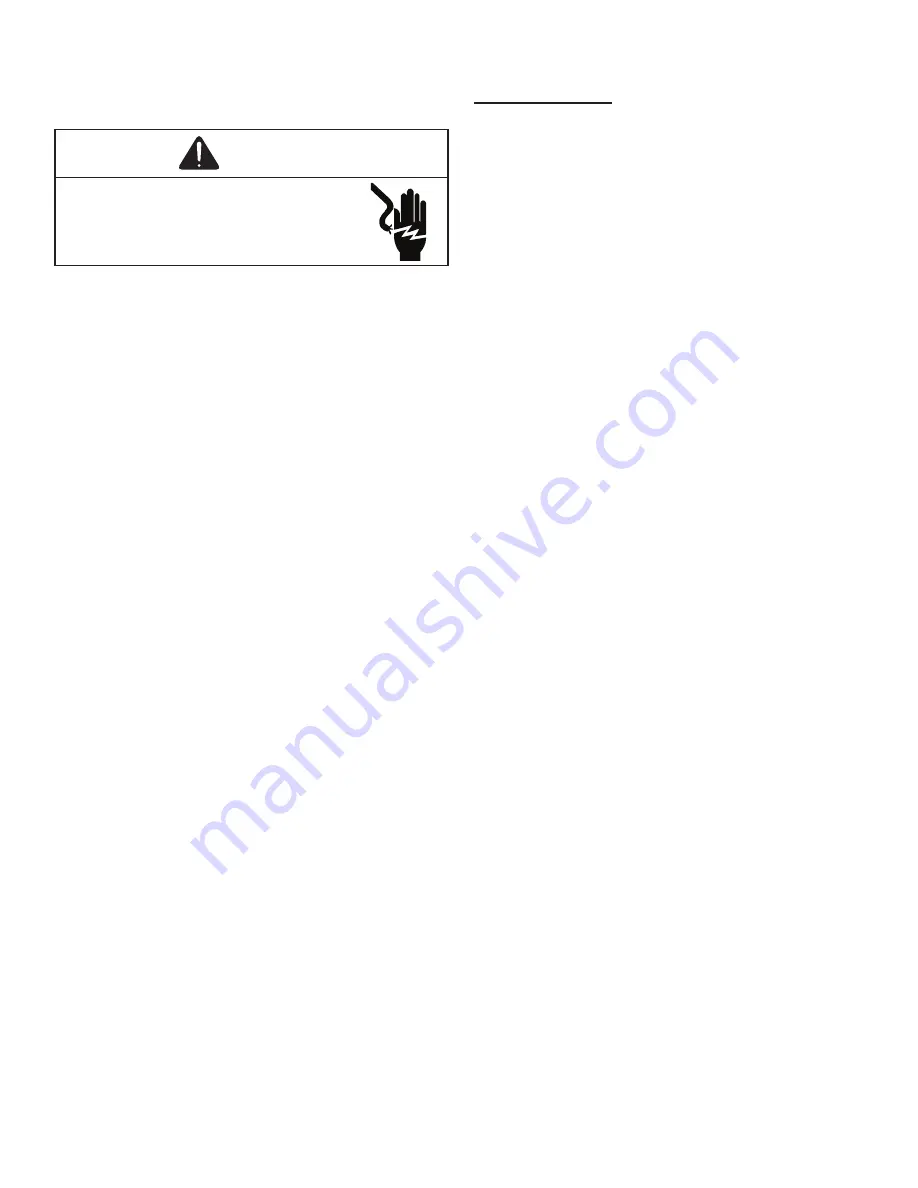
27
Replace or Clean Filter
WARNING
HIGH VOLTAGE!
Disconnect all power before servicing or
installing this unit. Multiple power sources
may be present. Failure to do so may cause
property damage, personal injury or death.
IMPORTANT NOTE:
Never operate unit without a filter installed
as dust and lint will build up on internal parts resulting in loss of
efficiency, equipment damage and possible fire.
A return air filter is not supplied with this unit; however, there must
be a means of filtering the return air. An indoor air filter must be
used with your comfort system. A properly maintained filter will
keep the indoor coil of your comfort system clean. A dirty coil
could cause poor operation and/or severe equipment damage.
The installer of your unit can tell you where your filter(s) are and
how to clean or replace them.
Check your return filter(s) at least once every two months. When
they are dirty, replace or clean as required. Disposable type filters
should be replaced. Reusable type filters may be cleaned.
NOTE:
Reusable type filters should be washed with warm water,
dried completely and sprayed with an adhesive according to the
manufacturers recommendations.
You may want to ask your dealer about high efficiency filters. High
efficiency filters are available in both electronic and non-electronic
types. These filters can do a better job of catching small airborne
particles.
Improper filter maintenance is the most common cause of inade
-
quate heating or cooling performance. Filters should be cleaned
(permanent) or replaced (disposable) every two months or as
required. When replacing a filter, it must be replaced with a filter
of the same type and size and always make certain the air flow
arrows on the filter point in the proper direction.
Condenser, Evaporator and Induced Draft Motors
The bearings on the air circulating blower motor, condenser motor
and the combustion fan motor are permanently lubricated and
require no further lubrication.
Compressor
The compressor motor is hermetically sealed and does not re-
quire additional oiling.
Aluminum Indoor Coil Cleaning (Qualified Servicer Only)
This unit is equipped with an aluminum tube evaporator coil. The
safest way to clean the evaporator coil is to simply flush the coil
with water. This cleaning practice remains as the recommended
cleaning method for both copper tube and aluminum tube residen-
tial cooling coils. An alternate cleaning method is to use one of the
products listed in the technical publication TP-109 (shipped in the
literature bag with the unit) to clean the coils. The cleaners listed
are the only agents deemed safe and approved for use to clean
round tube aluminum coils. TP-109 is available on the web site in
Partner Link > Service Toolkit.
NOTE:
Ensure coils are rinsed well after use of any chemical
cleaners.
Annual Inspection (Qualified Servicer Only)
Your package unit should be inspected by a qualified installer, or
service agency at least twice every year. This check should be
performed before the heating and cooling seasons begin. This will
ensure that adequate combustion air is being drawn and the vent
system is working properly. Particular attention should be paid to
the following items. Repair as necessary.
• Check physical support of the unit. Ensure it is sound with-
out any sagging, cracks, or gaps, around the base.
• Check for obvious signs of deterioration of the unit.
• Flue Hood and Combustion Air Inlet. Check for blockage
(wasp nest, etc.) and corrosion.
Flue Hood (Qualified Servicer Only)
• Return Air Connection. Check for physical soundness and
ensure that the connection is firmly sealed to the package
unit casing.
• Heat exchanger. Check for corrosion and/or obstructions
within the heat exchanger passageways.
•
Burners. Check for proper ignition, burner flame, and flame
sense.
• Wiring. Check wires for damage. Check electrical connec-
tions for tightness and/or corrosion.
•
Filters. Check that filters are clean and in the proper place
-
ment in the unit or duct system.
• Louvers. Inspect air inlet louvers inside the heat exchanger
compartments. Ensure the area is clean and free of dirt and
debris.
Clean Outside Coil (Qualified Servicer Only)
The outdoor coil should be inspected annually. It is important to
keep the outdoor coil clean. Dirt, leaves, or debris could restrict
the airflow. If cleaning of the outdoor coil becomes necessary, hire
a qualified servicer. Inexperienced people could easily puncture
the tubing in the coil.
Before Calling Your Servicer
•
Check the thermostat to confirm that it is properly set.
•
Check the disconnect switch near the unit to confirm that it
is closed.
• Check the electrical panel for tripped circuit breakers or
failed fuses. Reset the circuit breakers or replace fuses as
necessary.
• Check for blockage of the indoor air inlets and outlets.
Confirm that they are open and have not been blocked by
objects (rugs, curtains or furniture).
•
Check for obstructions on the unit. Confirm that it has not
been covered on the sides or the top. Remove any obstruc-
tion that can be safely removed. If the unit is covered with
dirt or debris, call a qualified servicer to clean it.
•
Check the filter. If it is dirty, clean or replace it.
PACKAGE UNITS
- DUAL FUEL & GAS
HOMEOWNER’S ROUTINE MAINTENANCE RECOMMENDATIONS
We strongly recommend a bi-annual maintenance checkup be performed by a
qualified service agency
before the heating and cooling seasons begin.