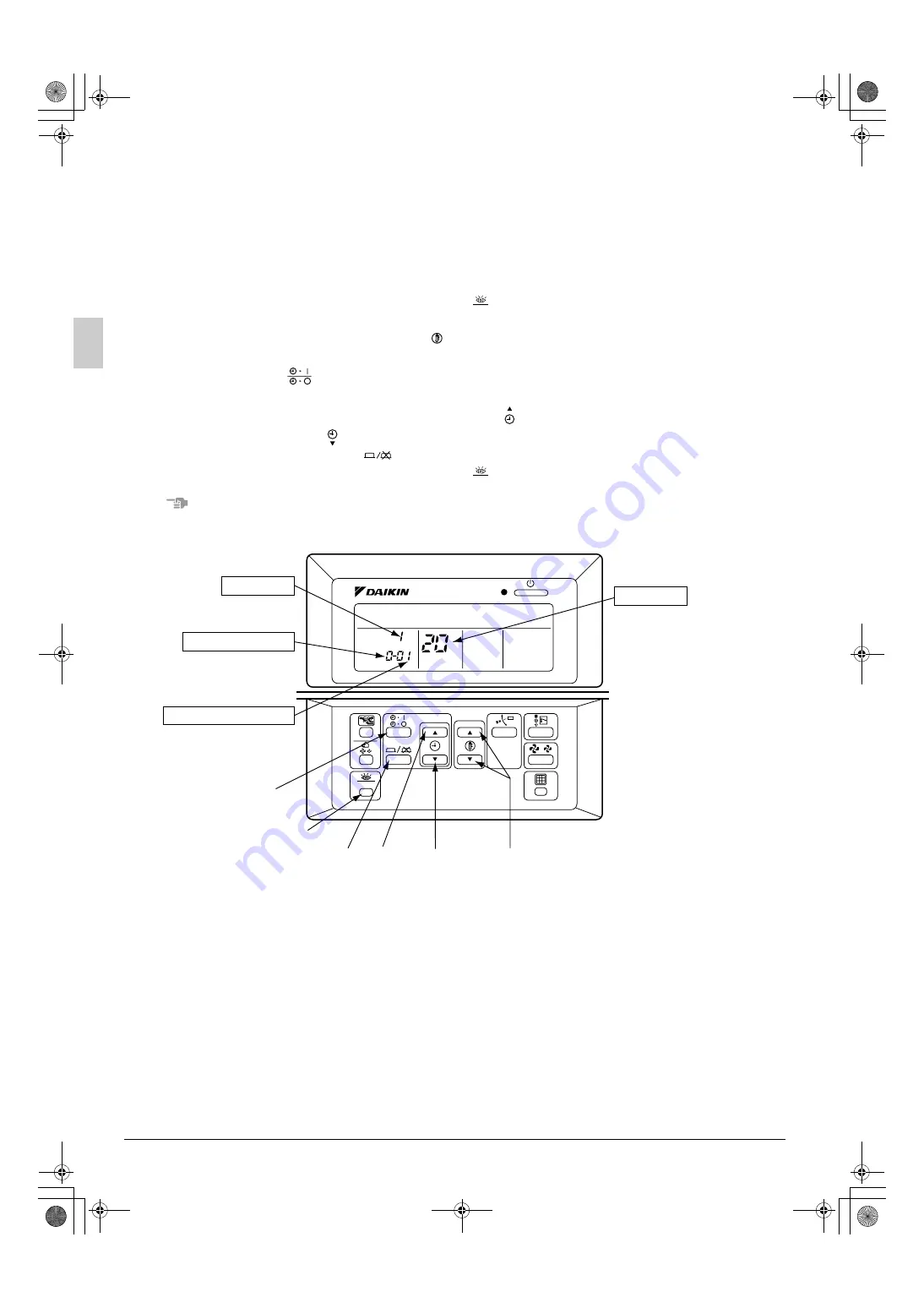
16
English
11. FIELD SETTING
Field setting
〈
Field setting must be made from the remote controller in accordance with the installation conditions.
〉
• Setting can be made by changing the “Mode No.”, “FIRST CODE NO.”, and “SECOND CODE NO.”.
• Refer to the following procedure for Field setting.
〈
Procedure
〉
(1) Press the INSPECTION/TEST OPERATION button (
) for 4 seconds or more in normal mode to
change to “FIELD SETTING MODE”.
(2) Press the TEMPERATURE SETTING button ( ) and choose the desired “Mode No.”.
(3) Under group control, if setting on each indoor unit is to be performed, press the TIMER MODE
START/STOP button (
) and select the indoor unit number.
(Unnecessary in case of unified setting of group control)
(4) Press the PROGRAMING TIME upper part of the button (
) and select the “FIRST CODE NO.”.
(5) Press the part of the button ( ) and select the “SECOND CODE NO.”.
(6) Press the TIMER ON/OFF button (
) once to fix the change of the setting.
(7) Press the INSPECTION/TEST OPERATION button (
) to return to the “NORMAL MODE”.
NOTE
•
Setting is performed by a group as a seto when individual setting of each indoor unit is required, or when
the setting results must be checked, use the mode number is ( ).
1. Setting air filter sign
•
Control panels are equiped with the liquid crystal display of air filter signs to display the time to clean
air filters.
•
Change the “ SECOND CODE NO.” according to Table 2 depending on the amount of dirt or dust in the
room.
(“SECOND CODE NO.” is factory set to “01” for filter contamination-light)
TEST
TEST
SETTING
TEST
UNIT NO.
Mode No.
SECOND CODE NO.
FIRST CODE NO.
UNIT NO.
(4)
(5)
(2)
(3)
(6)
(1)(7)
01_EN_3PA60136-8Y.fm Page 16 Saturday, December 22, 2007 1:04 PM