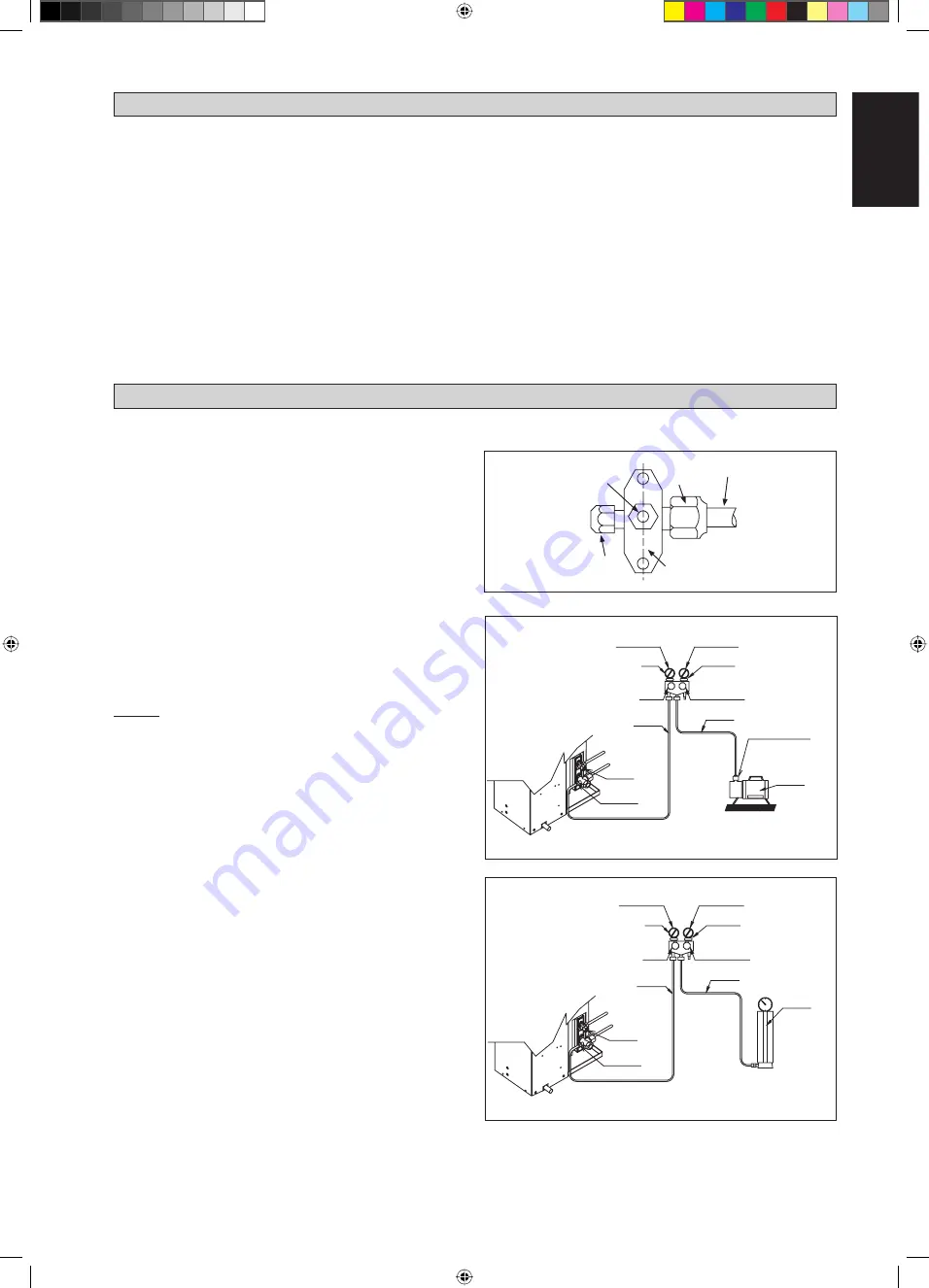
English
1-13
SPECIAL PRECAUTIONS WHEN DEALING WITH R410A UNIT
R410A is a new HFC refrigerant which does not damage the
ozone layer. The working pressure of this new refrigerant is
1.6 times higher than conventional refrigerant (R22), thus
proper installation/servicing is essential.
Never use refrigerant other than R410A in an air conditioner
which is designed to operate with R410A.
POE or PVE oil is used as lubricant for R410A compressor,
which is different from the mineral oil used for R22
compressor. During installation or servicing, extra precaution
must be taken not to expose the R410A system too long
to moist air. Residual POE or PVE oil in the piping and
components can absorb moisture from the air.
To prevent mischarging, the diameter of the service port
on the flare valve is different from that of R22.
•
•
•
Use tools and materials exclusively for refrigerant R410A.
Tools exclusively for R410A are manifold valve, charging
hose, pressure gauge, gas leak detector, flare tools, torque
wrench, vacuum pump and refrigerant cylinder.
As an R410A air conditioner incurs higher pressure
than R22 units, it is essential to choose the copper pipes
correctly. Never use copper pipes thinner than 0.8mm even
though they are available in the market.
If the refrigerant gas leakage occurs during installation/
servicing, be sure to ventilate fully. If the refrigerant gas
comes into contact with fire, a poisonous gas may occur.
When installing or removing an air conditioner, do not
allow air or moisture to remain in the refrigerant cycle.
•
•
•
•
VACUUMING AND CHARGING
Vacuuming is necessary to eliminate all moisture and air from the system.
Vacuuming The Piping And The Indoor Unit
Except for the outdoor unit which is pre-charged with
refrigerant, the indoor unit and the refrigerant connection
pipes must be air-purged because the air containing moisture
that remains in the refrigerant cycle may cause malfunction
of the compressor.
Remove the caps from the valve and the service port.
Connect the center of the charging gauge to the vacuum
pump.
Connect the charging gauge to the service port of the 3-way
valve.
Start the vacuum pump. Evacuate for approximately 30
minutes. The evacuation time varies with different vacuum
pump capacity. Confirm that the charging gauge needle has
moved towards -760mmHg.
Caution
If the gauge needle does not move to -760mmHg, be sure to
check for gas leaks (using the refrigerant detector) at flare
type connection of the indoor and outdoor unit and repair
the leak before proceeding to the next step.
Close the valve of the changing gauge and stop the vacuum
pump.
On the outdoor unit, open the suction valve (3 way) and
liquid valve (2 way) (in anti-clockwise direction) with 4mm
key for hexagon sacked screw.
Charge Operation
This operation must be done by using a gas cylinder and a
precise weighing machine. The additional charge is topped-up
into the outdoor unit using the suction valve via the service
port.
Remove the service port cap.
Connect the low pressure side of the charging gauge to the
suction service port center of the cylinder tank and close
the high pressure side of the gauge. Purge the air from the
service hose.
Start the air conditioner unit.
Open the gas cylinder and low pressure charging valve.
When the required refrigerant quantity is pumped into
the unit, close the low pressure side and the gas cylinder
valve.
Disconnect the service hose from service port. Put back
the service port cap.
•
•
•
•
•
•
•
•
•
•
•
•
•
Refrigerant Piping
Outdoor Unit 3 ways valve
Allen key
Service Port
Flare nut
HIGH PRESSURE GAUGE
GAUGE MANIFOLD
LOW PRESSURE GAUGE
HANDLE
HI
(ALWAYS CLOSED)
CHARGE HOSE
-760mmHg
HANDLE
LO
CHARGE HOSE
VACUUM PUMP
ADAPTER FOR
COUNTER FLOW
PREVENTION
CHECK VALVE
LIQUID VALVE
HIGH PRESSURE GAUGE
LOW PRESSURE GAUGE
GAUGE MANIFOLD
-760mmHg
HANDLE
LO
HANDLE
HI
(ALWAYS CLOSED)
CHARGE HOSE
CHARGE HOSE
CHECK VALVE
LIQUID VALVE
GAS VALVE
(3-WAY)
CONFIGURATION OF AIR
PURGE BY CHARGING
GAS VALVE
(3-WAY)
CONFIGURATION OF AIR
PURGE BY CHARGING
1 IM-5WMYJ-1113(2)DK_EN-39396B.i13 13
1 IM-5WMYJ-1113(2)DK_EN-39396B.i13 13
4/23/14 12:02:16 PM
4/23/14 12:02:16 PM