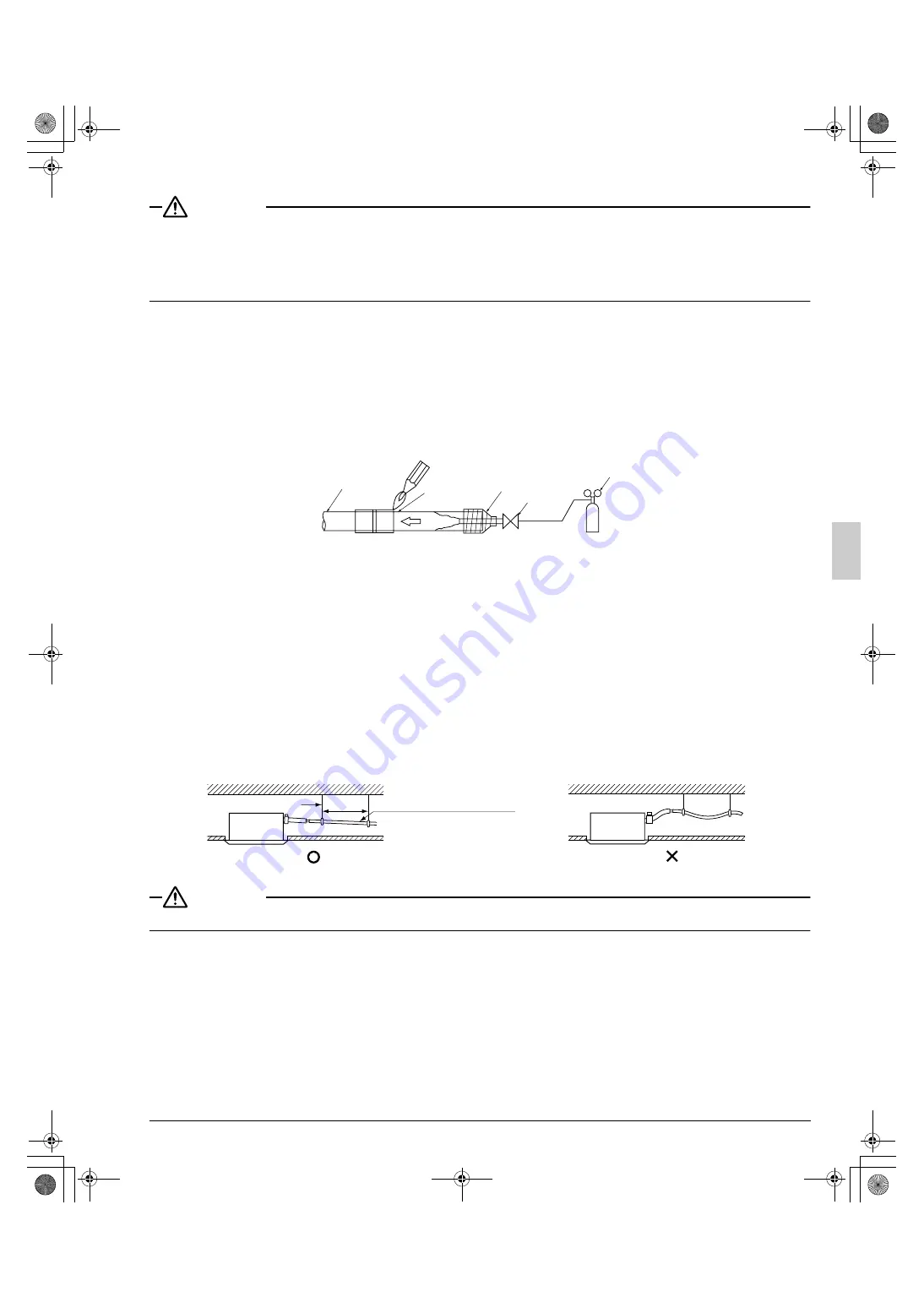
English
13
CAUTION
CAUTION TO BE TAKEN WHEN BRAZING REFRIGERANT PIPING
“Do not use flux when brazing refrigerant piping. Therefore, use the phosphor copper brazing filler metal
(BCuP-2/B-Cu93P-710/795) which does not require flux.”
(Flux has extremely harmful influence on refrigerant piping systems. For instance, if the chlorine based flux is
used, it will cause pipe corrosion or, in particular, if the flux contains fluorine, it will damage the refrigerant oil.)
•
Before brazing field refrigerant piping, nitrogen gas shall be blown through the piping to expel air from the
piping.
If you brazing is done without nitrogen gas blowing, a large amount of oxide film develops inside the piping,
and could cause system malfunction.
•
When brazing the refrigerant piping, only begin brazing after having carried out nitrogen substitution or
while inserting nitrogen into the refrigerant piping. Once this is done, connect the indoor unit with a flared
or a flanged connection.
•
Nitrogen should be set to 2.9psi with a pressure-reducing valve if brazing while inserting nitrogen into the
piping.
(Refer to Fig. 17)
7. DRAIN PIPING WORK
(1)
Rig drain piping
•
As for drain work, perform piping in such a manner that water can be drained properly.
•
Employ a pipe with either the same diameter or with the diameter larger (excluding the raising section) than
that of the connecting pipe (PVC pipe, nominal diameter 1in., outside diameter 1-1/4in.).
•
Keep the drain pipe short and sloping downwards at a gradient of at least 1/100 to prevent air pockets from
forming.
•
If the drain pipe cannot be sufficiently set on a slope, execute the drain raising piping.
•
To keep the drain pipe from sagging, space hanger bracket every 3 to 5ft..
CAUTION
Water pooling in the drainage piping can cause the drain to clog.
•
Use the attached drain hose (1) and metal clamp (2).
•
Insert the drain hose into the drain socket up to the base, and tighten the metal clamp securely within the
portion of a white tape of the hose-inserted tip. Tighten the metal clamp until the screw head is less than
5/32in. from the hose.
•
Wrap the attached sealing pad (10) over the metal clamp and drain hose to insulate.
Nitrogen
Pressure-reducing valve
Hands valve
Taping
Refrigerant piping
Part to be
brazed
Nitrogen
Fig. 17
1/100 gradient or more
3-5ft.
Fig. 18-1
GOOD
Hanger bracket
Fig. 18-2
WRONG
01_EN_3P161684-6K.fm Page 13 Friday, September 16, 2011 10:00 PM