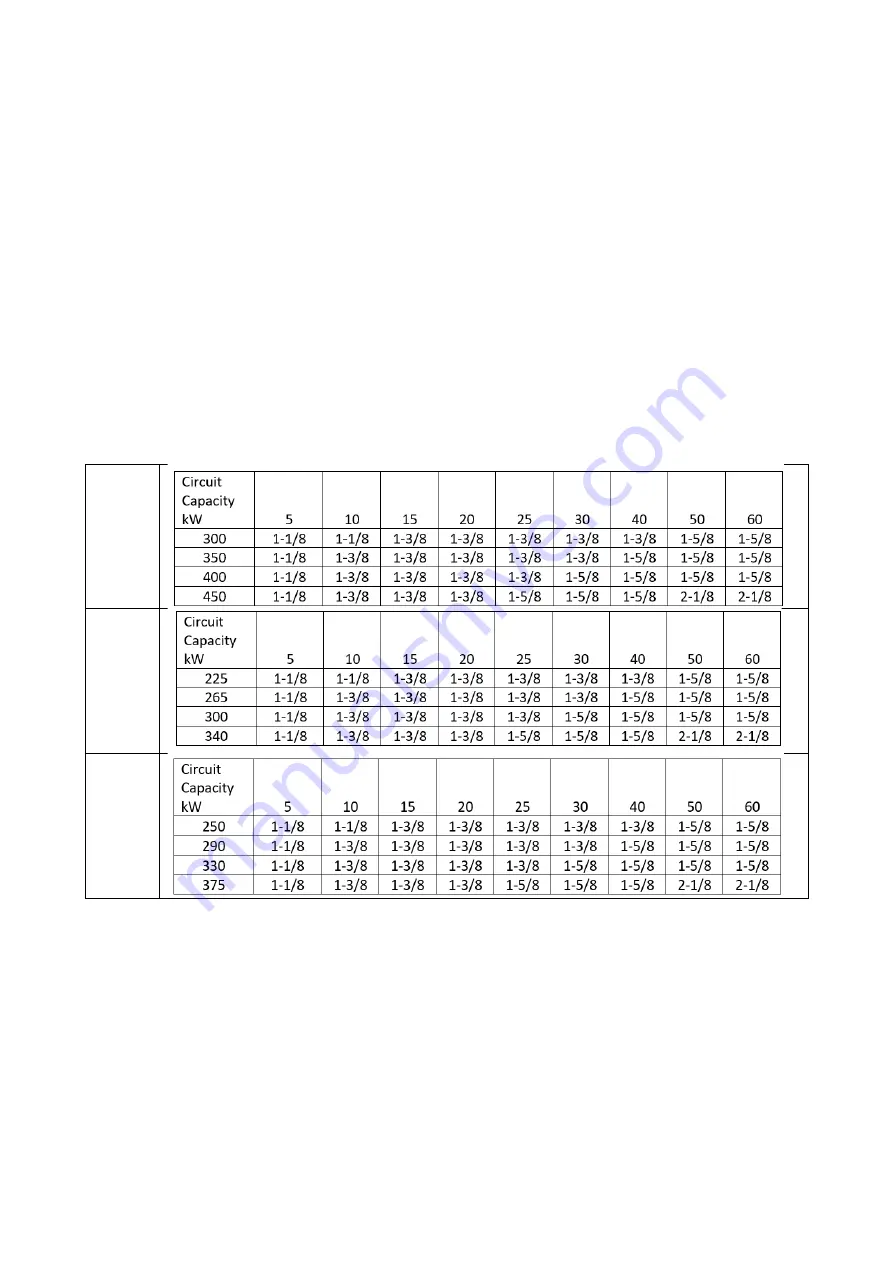
D-EIMWC01008-16_03EN - 26/35
6.2.2
Liquid line sizing
In designing liquid lines it is important that the liquid reaches the expansion valve without flash gas, since this gas will
reduce the valve capacity. Because flashing gas can be caused by pressure drop in the line, the pressure losses due to
friction and changes in static head should be kept at minimum.
A check valve must be installed in the liquid line where the ambient temperature can drop below the equipment room
temperature to prevent liquid migration to the condenser and to maintain liquid refrigerant in the line for unit startup (if
thermostatic expansion valve is used, the check valve also helps to keep liquid pressure high enough to keep the valve
closed with compressor off).
A relief valve should be installed between the check valve and the expansion valve.
The liquid line diameter should be as small as possible while maintaining acceptable pressure drop. This is necessary to
minimize refrigerant charge. The total length between the chiller unit and the air -cooled condenser must not exceed 60
equivalent meters.
Liquid line risers in the system will require an additional 11.5 kPa pressure drop per meter of vertical rise. When it is
necessary to have a liquid line riser, make the vertical run immediately after the condenser before any additional
restrictions. The liquid line risers must not exceed 3 meters in height from the condenser liquid line connection (see
Figure 22). The liquid line does not have to be pitched.
Liquid lines are not typically insulated. However, if the lines are exposed to solar heat gain or temperatures exceeding
43°C, sub-cooling may be affected. In these situations, insulate the liquid lines.
Reference for liquid line sizing is shown in Table 3. It has to be used for reference only, for circuit working with
condensing temperature equal to 55°C and 5°C subcooling at the condenser outlet. Line dimensioning is responsibility of
plant designer, use ASHRAE Refrigeration Handbook or other suitable design guide.
Table 2
– liquid line sizing
R134a
R1234ze
R513A
6.2.3
Discharge (Hot Gas) Line Sizing
Discharge line size is based on the velocity needed for proper chiller operation handling oil properly and protecting
compressor from damage that can result from condensing liquid refrigerant during shutdown.
Total friction loss for discharge line from 20 to 40 kPa is considered good design. Carefully consideration must be given
for sizing each section of piping so that gas velocities are sufficient at all operating conditions to carry oil.
If the velocity in a vertical discharge riser is to low, considerable oil can collect in the riser and horizontal header, causing
compressor to lose oil and it can result in compressor damage due to lack of oil. When the compressor load (and the gas
velocity in the discharge line) increase the oil collected during reduced load can be carried out in a slug back to the
compressor causing damage.
Any discharge lines coming into and horizontal header should rise above the centerline of the header.
The discharge lines should pitch downward, in the direction of the hot gas flow, at the rate of 6 mm per meter of
horizontal run. This is necessary to move by gravity any oil lying in the header. Oil pockets should be avoided because
oil would collect at such points of the compressor can become starved.
If the chiller unit is below condenser, loop the discharge line to at least 2.5 cm above the top of the condenser. A