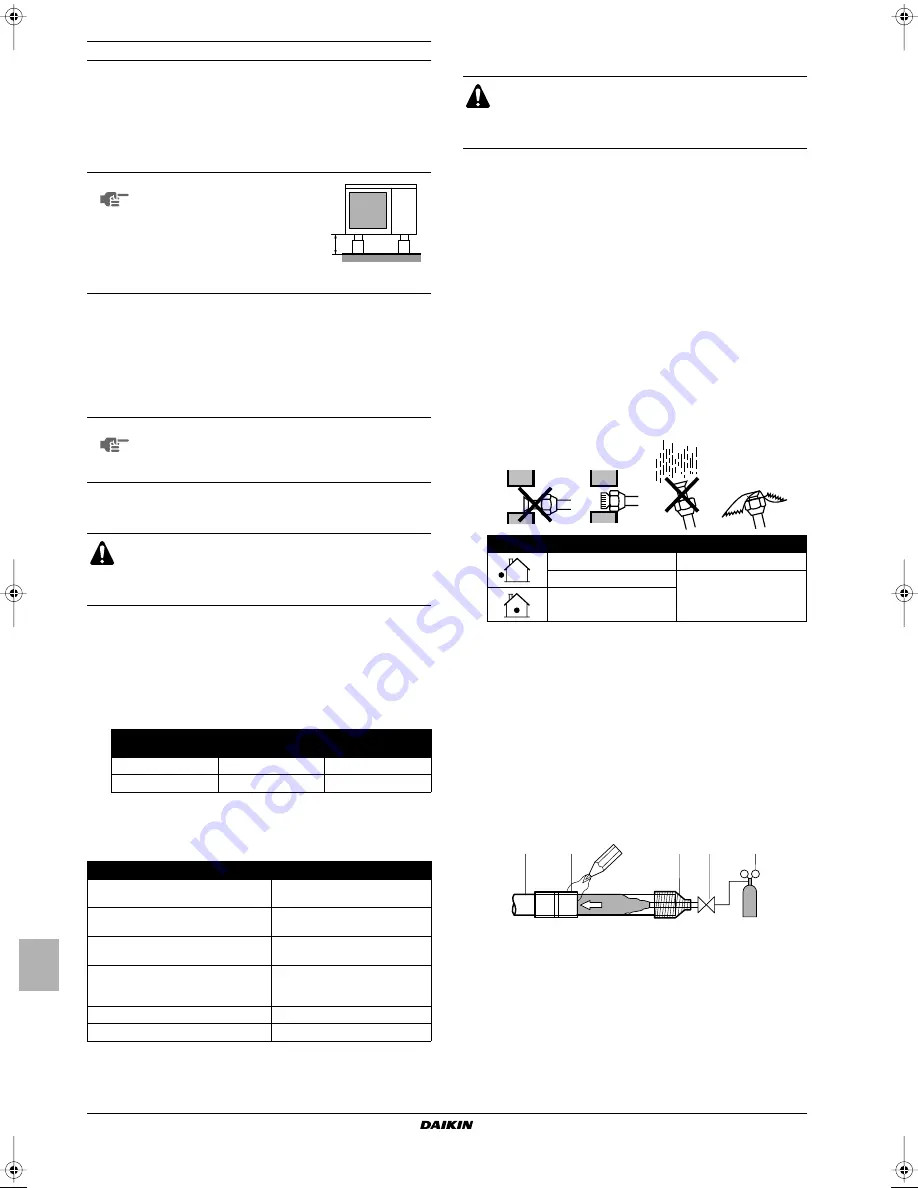
Installation manual
7
ERLQ018~030BAVJU
Outdoor unit for air to water heat pump
4PW62590-1 – 07.2010
Drain work
Refer to "6.2. Weather dependent precautions" on page 5.
■
If drain work from the outdoor unit causes trouble (for example, if
the drain water may splash on people) provide a waterproof
plate (field supply) within 5.9 inch (150 mm) of the underside of
the unit.
■
Make sure the drain works properly.
8.
R
EFRIGERANT
PIPE
SIZE
AND
ALLOWABLE
PIPE
LENGTH
8.1.
Refrigerant piping material
8.2.
Piping material selection
■
Foreign materials inside pipes (including oils for fabrication)
must be
≤
0.014 grain/ft (30 mg/10 m).
■
Temper grade: use piping with temper grade in function of the
pipe diameter as listed in table below.
■
The pipe thickness of the refrigerant piping shall comply with the
applicable legislation. The minimal pipe thickness for R410A
piping must be in accordance with the table below.
O = Annealed
8.3.
Refrigerant piping specifications
9.
P
RECAUTIONS
ON
REFRIGERANT
PIPING
■
Do not allow anything other than the designated refrigerant to
get mixed into the freezing cycle, such as air, etc. If any
refrigerant gas leaks while working on the unit, ventilate the
room thoroughly right away.
■
Use R410A only when adding refrigerant
-
Installation tools:
Make sure to use installation tools (gauge manifold charge
hose, etc.) that are exclusively used for R410A installations
to withstand the pressure and to prevent foreign materials
(e.g. mineral oils and moisture) from mixing into the system.
-
Vacuum pump:
Use a 2-stage vacuum pump with a non-return valve.
Make sure the pump oil does not flow oppositely into the
system while the pump is not working.
Use a vacuum pump which can evacuate to –14.6 psi
[–100.7 kPa (5 Torr, –755 mm Hg)].
■
In order to prevent dirt, liquid or dust from entering the piping,
cure the piping with a pinch or taping.
-
Great caution is needed when passing copper tubes through
walls.
9.1.
Guidelines for brazing
■
Make sure to blow through with nitrogen when brazing.
Blowing through with nitrogen prevents the creation of large
quantities of oxidized film on the inside of the piping. An oxidized
film adversely affects valves and compressors in the
refrigerating system and prevents proper operation.
■
The nitrogen pressure should be set to 2.9 psi (0.02 MPa) (i.e.,
just enough so it can be felt on the skin) with a pressure-
reducing valve.
■
Do not use anti-oxidants when brazing the pipe joints.
Residue can clog pipes and break equipment.
NOTE
If drain holes of the outdoor
unit are covered by a
mounting base or by floor
surface, raise the unit in
order to provide a free
space of more than
3.94 inch (100 mm) under
the outdoor unit.
NOTE
Piping and other pressure containing parts shall
comply with the applicable legislation and shall be
suitable for refrigerant. Use phosphoric acid
deoxidised seamless copper for refrigerant.
CAUTION
Never use piping which has been used for previous
installations. Only use parts which are delivered with the
unit.
Pipe size
Temper grade of
piping material
Minimal thickness
1/4 inch (Ø6.4 mm)
O
0.031 inch (0.8 mm)
5/8 inch (Ø15.9 mm)
O
0.039 inch (1.0 mm)
Refrigerant piping specifications
Maximum allowable piping length
between outdoor unit and indoor unit
98.4 ft (30 m)
Minimum required piping length
between outdoor unit and indoor unit
9.8 ft (3 m)
Maximum allowable height difference
between outdoor unit and indoor unit
65.6 ft (20 m)
Additional refrigerant required for
refrigerant pipe exceeding 32.8 ft (10 m)
in length
0.013 lbs/ft (20 g/m)
Gas pipe - outer diameter
5/8 inch (15.9 mm)
Liquid pipe - outer diameter
1/4 inch (6.4 mm)
≥
3.94 inch
(
≥
100 mm)
CAUTION
R410A, as well as other refrigerants, should always be
recovered and never be released directly into the
environment.
Installation period
Protection method
More than a month
Pinch the pipe
Less than a month
Pinch or tape the pipe
Regardless of the period
1
Refrigerant piping
2
Part to be brazed
3
Taping
4
Hands valve
5
Pressure-reducing valve
6
Nitrogen
1
2
3
4
5
6
6
4PW62590-1.book Page 7 Wednesday, June 30, 2010 12:17 PM