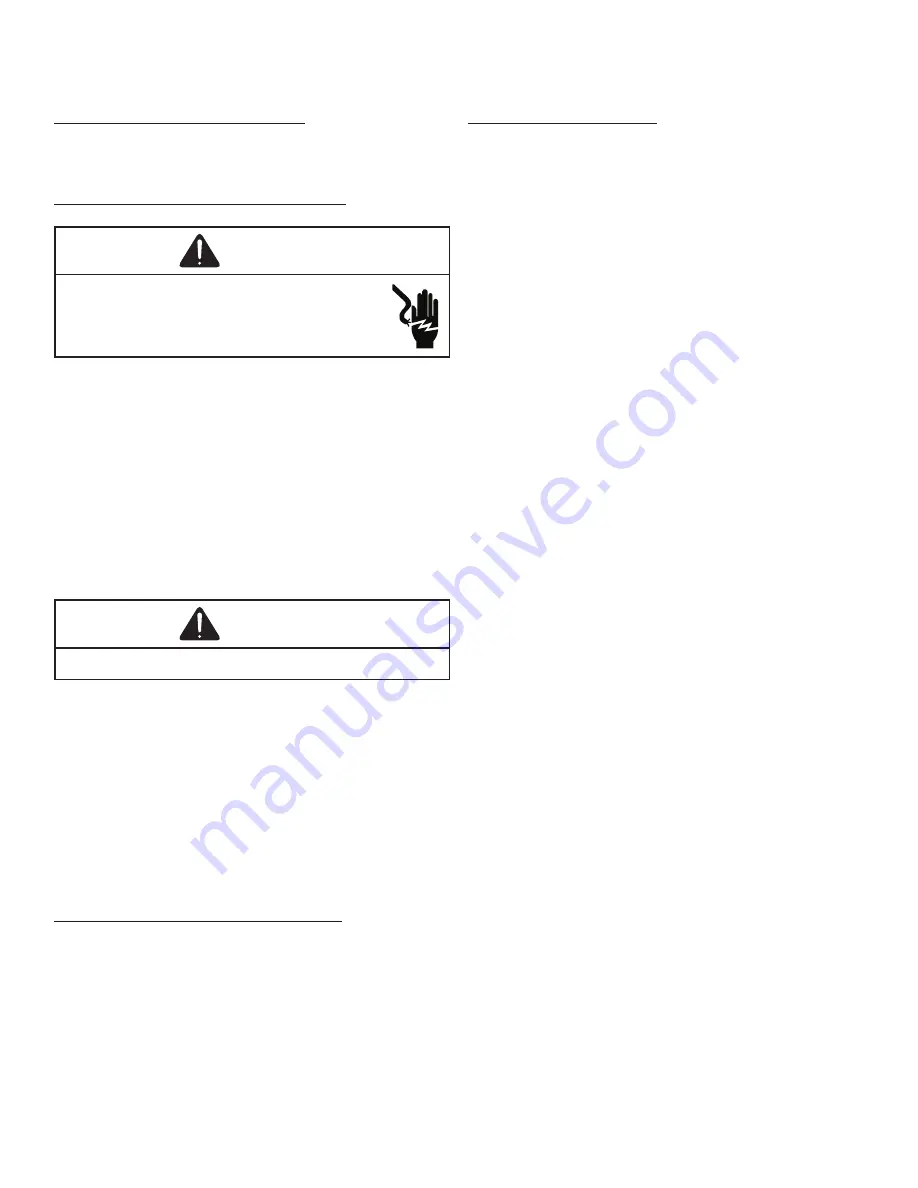
13
SERVICING
S-9 Checking Fan Relay Contacts
The fan relays are incorporated into the control board. See
Testing Ignition Control Module for checking control board.
S-12 Checking High Pressure Control
WARNING
High Voltage!
Disconnect all power before servicing or
installing. Multiple power sources may be
present. Failure to do so may cause property
damage, personal injury or death.
The high pressure control senses the pressure in the liquid
line. If abnormally high condensing pressures develop, the
contacts of the control open, breaking the control circuit
before the compressor motor overloads. This control is
automatically reset.
1. Using an ohmmeter, check across terminals of
high pressure control, with wire removed. If not
continuous, the contacts are open.
2. Attach a gauge to the dill valve port on the base valve.
With power ON:
WARNING
Line voltage now present
3. Start the system and place a piece of cardboard in
front of the condenser coil, raising the condensing
pressure.
4. Check pressure at which the high pressure control
cuts-out.
If it cuts-out at 660 PSIG ± 10 PSIG, it is operating normally.
If it cuts out below this pressure range, replace the control.
The control should reset at 420 PSIG ± 25 PSIG.
S-13 Checking Low Pressure Control
The low pressure control senses the pressure in the suction
line and will open its contacts on a drop in pressure. The
low pressure control will automatically reset itself with a
rise in pressure.
The low pressure control is designed to cut-out (open) at
approximately 55 PSIG ± 7 PSIG. It will automatically cut-in
(close) at approximately 95 PSIG ± 7 PSIG.
Test for continuity using a VOM and if not as above,
replace the control.
S-15 Checking Capacitor
Capacitor, Run
A run capacitor is wired across the auxiliary and main
windings of a single phase permanent split capacitor
motor. The capacitors primary function is to reduce
the line current while greatly improving the torque
characteristics of a motor. This is accomplished by using
the 90° phase relationship between the capacitor current
and voltage in conjunction with the motor windings so that
the motor will give two phase operation when connected
to a single phase circuit. The capacitor also reduces the
line current to the motor by improving the power factor.
Capacitor, Start
Scroll Compressor Models
Hard start components are not required on Scroll
compressor equipped units due to a non-replaceable
check valve located in the discharge line of the compressor.
However hard start kits are available and may improve low
voltage starting characteristics.
This check valve closes off high side pressure to the
compressor after shut down allowing equalization through
the scroll flanks. Equalization requires only about one or
two seconds during which time the compressor may turn
backwards.
Your unit comes with a 180-second anti-short cycle
to prevent the compressor from starting and running
backwards.
Models Equipped With A Hard Start Device
A start capacitor is wired in parallel with the run capacitor
to increase the starting torque. The start capacitor is of
the electrolytic type, rather than metallized polypropylene
as used in the run capacitor.
A switching device must be wired in series with the
capacitor to remove it from the electrical circuit after the
compressor starts to run. Not removing the start capacitor
will overheat the capacitor and burn out the compressor
windings.
These capacitors have a 15,000 ohm, 2 watt resistor
wired across its terminals. The object of the resistor
is to discharge the capacitor under certain operating
conditions, rather than having it discharge across the
closing of the contacts within the switching device such as
the Start Relay, and to reduce the chance of shock to the
servicer. See the Servicing Section for specific information
concerning capacitors.