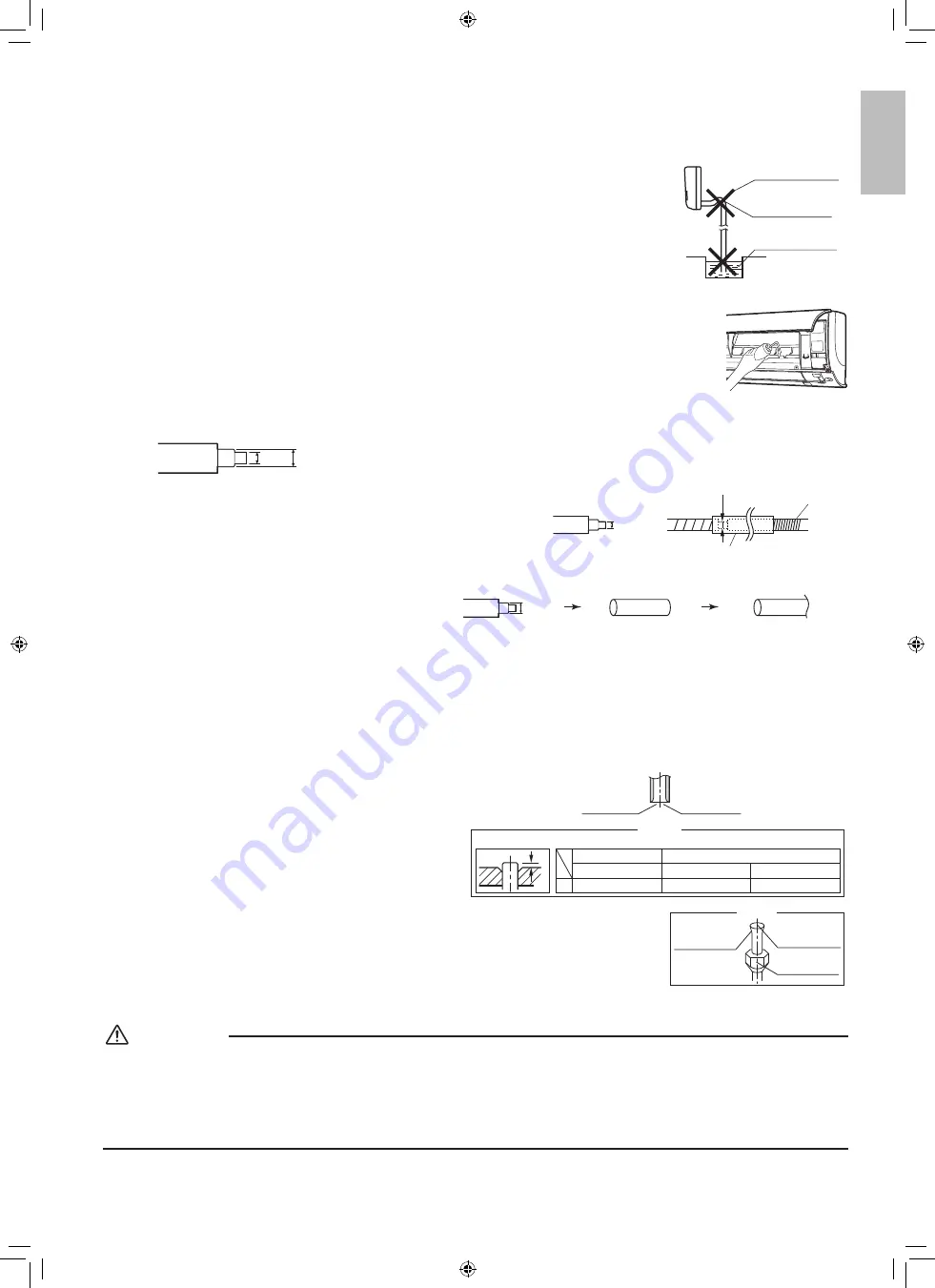
English
■
English
10
6.
Drain piping
1) Connect the drain hose, as described right.
The drain hose should
be inclined downward.
No trap is permitted.
Do not put the end
of the hose in water.
2) Remove the air filters and pour some water into the drain pan to check the water flows
smoothly.
3) If drain hose extension or embedded drain piping is required, use appropriate parts that match the hose front end.
[Figure of hose front end]
ϕ
18
ϕ
16
4) When extending the drain hose, use a commercially available
extension hose with an inner diameter of 16mm.
Be sure to thermally insulate the indoor section of the extension
hose.
ϕ
16
Drain hose supplied
with the indoor unit
Indoor unit
drain hose
ϕ
16
Extension drain hose
Heat insulation tube
(field supply)
5) When connecting a rigid polyvinyl chloride pipe
(nominal diameter 13mm) directly to the drain
hose attached to the indoor unit as with embed
-
ded piping work, use any commercially available
drain socket (nominal diameter 13mm) as a joint.
Commercially available drain
socket
(nominal diameter 13mm)
Commercially available rigid
polyvinyl chloride pipe
(nominal diameter 13mm)
Drain hose supplied
with the indoor unit
ϕ
18
Refrigerant Piping Work
1.
Flaring the pipe end
1) Cut the pipe end with a pipe cutter.
2) Remove burrs with the cut surface facing downward
so that the chips do not enter the pipe.
3) Put the flare nut on the pipe.
4) Flare the pipe.
5) Check that the flaring is properly made.
Set exactly at the position shown below.
A
Flaring
Die
A
0-0.5mm
Clutch-type
Flare tool for R410A
1.0-1.5mm
Clutch-type (Rigid-type)
1.5-2.0mm
Wing-nut type (Imperial-type)
Conventional flare tool
(Cut exactly at
right angles.)
Remove burrs.
Check
Flare’s inner
surface must
be flaw-free.
The pipe end must
be evenly flared in
a perfect circle.
Make sure that the
flare nut is fitted.
WARNING
• Do not use mineral oil on flared part.
• Prevent mineral oil from getting into the system as this would reduce the lifetime of the units.
• Never use piping which has been used for previous installations. Only use parts which are delivered with the unit.
• Do never install a drier to this R410A unit in order to guarantee its lifetime.
• The drying material may dissolve and damage the system.
• Incomplete flaring may cause refrigerant gas leakage.
01_EN_3P297034-1.indd 10
10/12/2011 11:37:07 AM