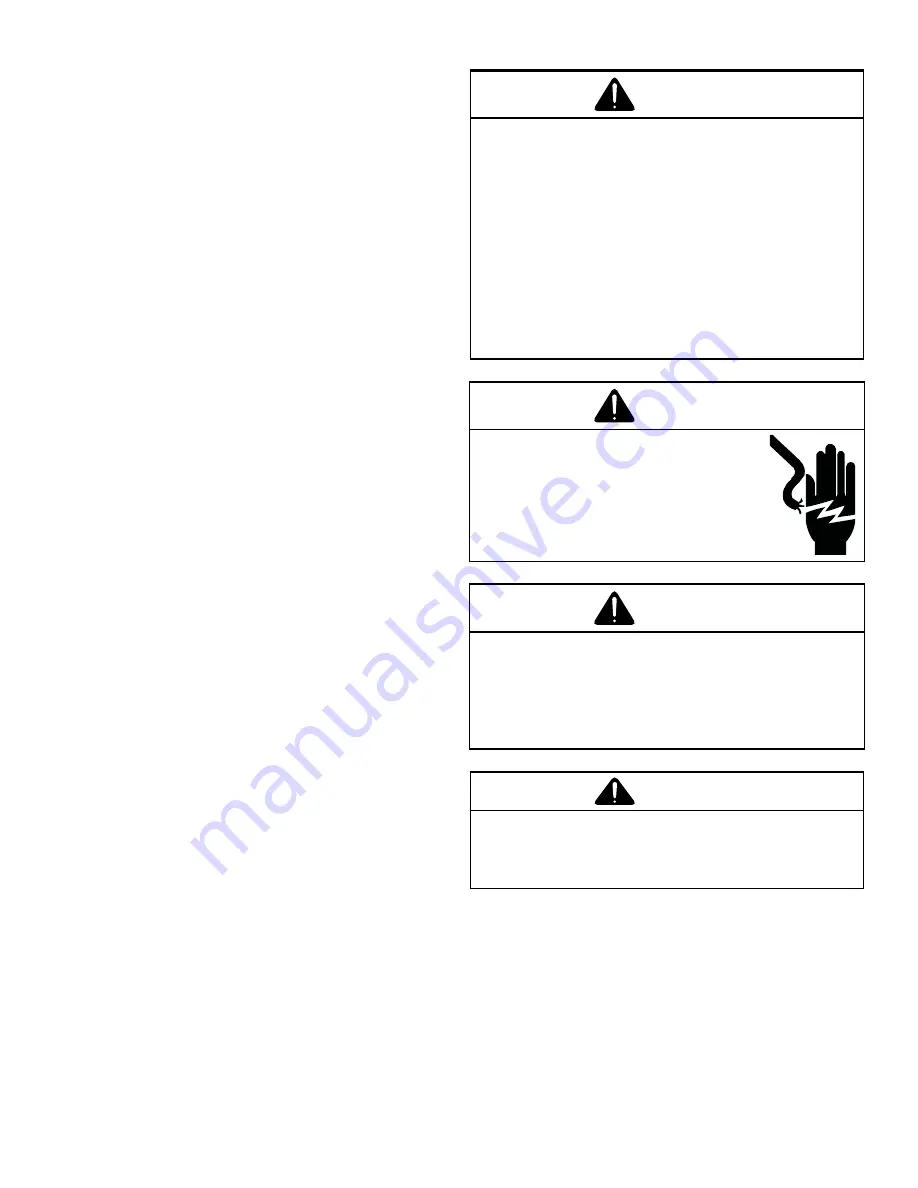
21
6. Check that the compressor is operating correctly.
The scroll compressors in these units MUST operate
in the proper rotation. To ensure the compressor
is operating in the correct direction, check the
compressor discharge line pressure or temperature
after the compressor is started.
The discharge pressure and discharge line temperature
should increase. If this does not occur and the compressor
is producing an exceptional amount of noise, perform the
following checks.
•
If the compressor is operating backward, disconnect
the unit power supply and lock it in the “OFF” position.
Switch two leads of the power supply at the unit
Single Point Power Block. Reconnect power and
check for compressor and condenser fan motor
operation.
7. With all safety devices closed, the system will
continue cooling operation until the room temperature
is satisfied.
8.
Increasing the room cooling setpoint to a value above
the current room temperature will simulate a satisfied
thermostat. The compressor and the supply fan will
cycle off.
9. After a time delay of approximately 3 minutes, the
compressor control circuits will be ready to respond to
a subsequent call for cooling.
Refrigeration Performance Check
Check that compressor RLA corresponds to values shown
in Appendix B. RLA draw can be much lower than values
listed at low load conditions and low ambient condensing
temperatures. Values in Appendix B can slightly exceed
at high load conditions and high ambient condensing
temperatures.
Final System Checks
1. Check to see if all supply and return air grilles are
adjusted and the air distribution system is balanced
for the best compromise between heating and cooling.
2. Check for air leaks in the ductwork. See Sections on
Air Flow Adjustments.
3. Make sure the unit is free of “rattles”, and the tubing
in the unit is free from excessive vibration. Also make
sure tubes or lines are not rubbing against each other
or sheet metal surfaces or edges. If so, correct the
trouble.
4.
Set the thermostat at the appropriate setting for
cooling and heating or automatic changeover for
normal use.
5. Be sure the Owner is instructed on the unit operation,
filter, servicing, correct thermostat operation, etc.
MAINTENANCE
WARNING
ELECTRICAL SHOCK, FIRE OR EXPLOSION HAZARD
Failure to follow safety warnings exactly could
result in dangerous operation, serious injury,
death or property damage.
Improper servicing could result in dangerous
operation, serious injury, death or property
damage.
•
Before servicing, disconnect all electrical
power to furnace.
•
When servicing controls, label all wires
prior to disconnecting. Reconnect wires
correctly.
•
Verify proper operation after servicing.
WARNING
HIGH VOLTAGE!
Disconnect all power before
servicing or installing this unit.
Multiple power sources may be
present. Failure to do so may cause
property damage, personal injury or
death.
WARNING
To prevent personal injury or death due to
improper installation, adjustment, alteration,
service or maintenance, refer to this manual.
For additional assistance or information,
consult a qualified installer, servicer agency or
the gas supplier.
CAUTION
Sheet metal parts, screws, clips and similar
items inherently have sharp edges, and it
is necessary that the installer and service
personnel exercise caution.
Preventive maintenance is the best way to avoid
unnecessary expense and inconvenience. Have this
system inspected at regular intervals by qualified service
personnel, at least twice a year. Routine maintenance
should cover the following items:
1. Tighten all set screws, and wire connections.
2.
Clean evaporator and condenser coils mechanically
or with cold water, if necessary. Usually any fouling
is only matted on the entering air face of the coil and
can be removed by brushing.
3. Replace filters as needed (see below).
4. Check for blockage of condensate drain.
Summary of Contents for AHRI 210
Page 31: ...31 ...
Page 32: ...32 ...
Page 33: ...33 THIS PAGE LEFT INTENTIONALLY BLANK ...
Page 34: ...34 THIS PAGE LEFT INTENTIONALLY BLANK ...