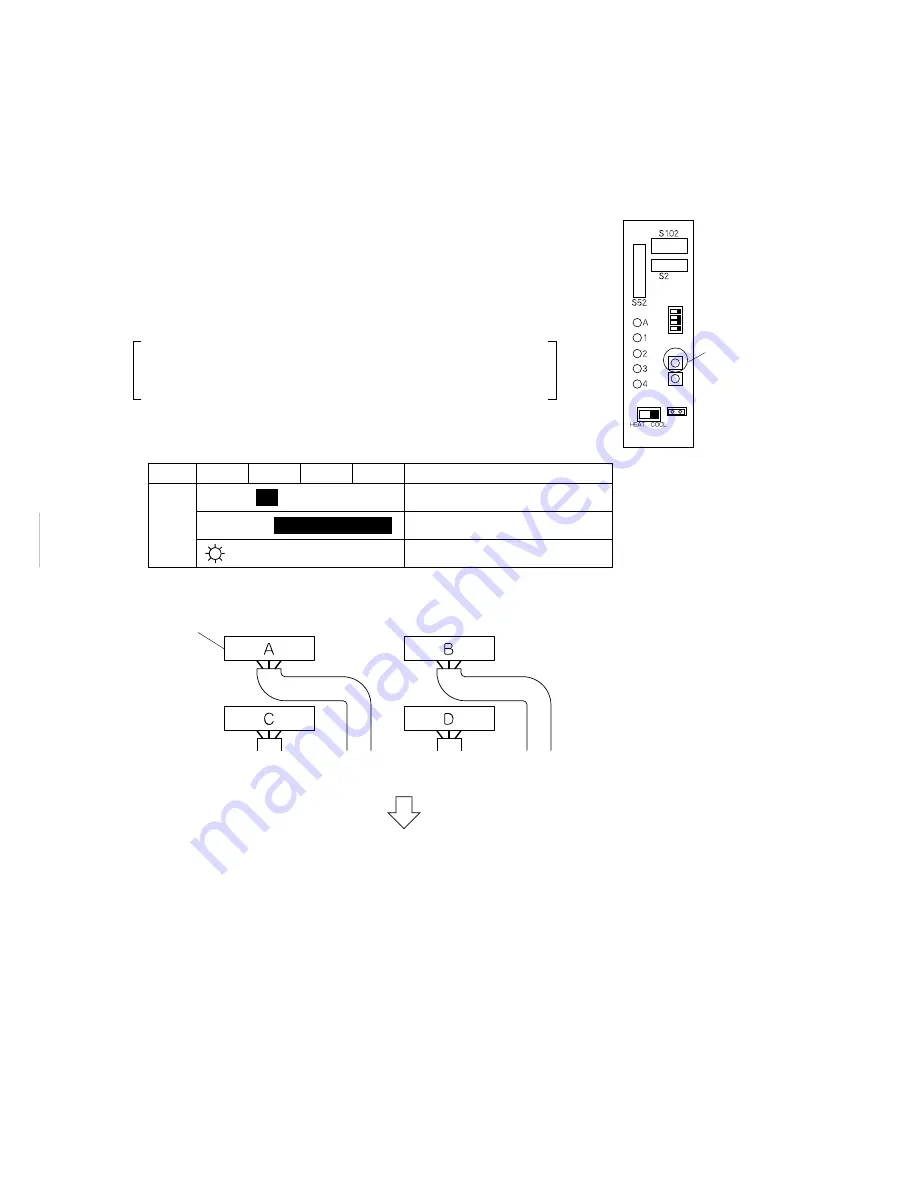
15
n
English
Trial Operation and Testing
• Before starting the test run, measure the voltage at the primary side of the safety breaker. Check that it is 220-240V.
• Check that all liquid and gas stop valves are fully open.
• Check that piping and wiring all match. The wiring error check can be conveniently used for underground wiring and other wiring
that cannot be directly checked.
1.
Wiring error check
• This product is capable of automatic correction of wiring error.
• Press the “wiring error check switch” on the outdoor unit service monitor
print board. However, the wiring error check switch will not function for
one minute after the safety breaker is turned on, or depending on the
outside air conditions (See NOTE 2.). Approximately 10–15 minutes
after the switch is pressed, the errors in the connection wiring will be
corrected.
If self-correction is not possible, check the indoor unit wiring and piping
in the usual manner.
NOTE:
1) For two rooms, LED 3 and 4 are not displayed, and for three rooms, LED 4 is not displayed.
2) If the outside air temperature is
5
°
C or less
, the wiring error check function will not operate.
3) After wiring error check operation is completed, LED indication will continue until ordinary operation starts.
This is normal.
4) Follow the product diagnosis procedures. (Check the nameplate on the underside of the stop valve.)
Wiring error
check switch
(SW3)
Service PC-board
The service monitor LEDs indicate whether or not correction is
possible, as shown in the table below. For details about how to read the
LED display, refer to the service guide.
LED
Status
1
2
3
4
All
Flashing
Automatic correction impossible
Automatic correction completed
Abnormal stop [NOTE. 4]
Message
Flashing
One after another
(One or more of LEDs 1 to 4 are ON)
Terminal block
Wiring error check
LED lighting sequence after a wiring correction.
Order of LED flashing: 2
➝
1
➝
3
➝
4
From Room C
to the “kitchen”
From Room B
to the “living room”
From Room D
to the “children’s room”
From Room A
to the “bedroom”
Wiring correct example
∗
The figure at left shows branch wiring.