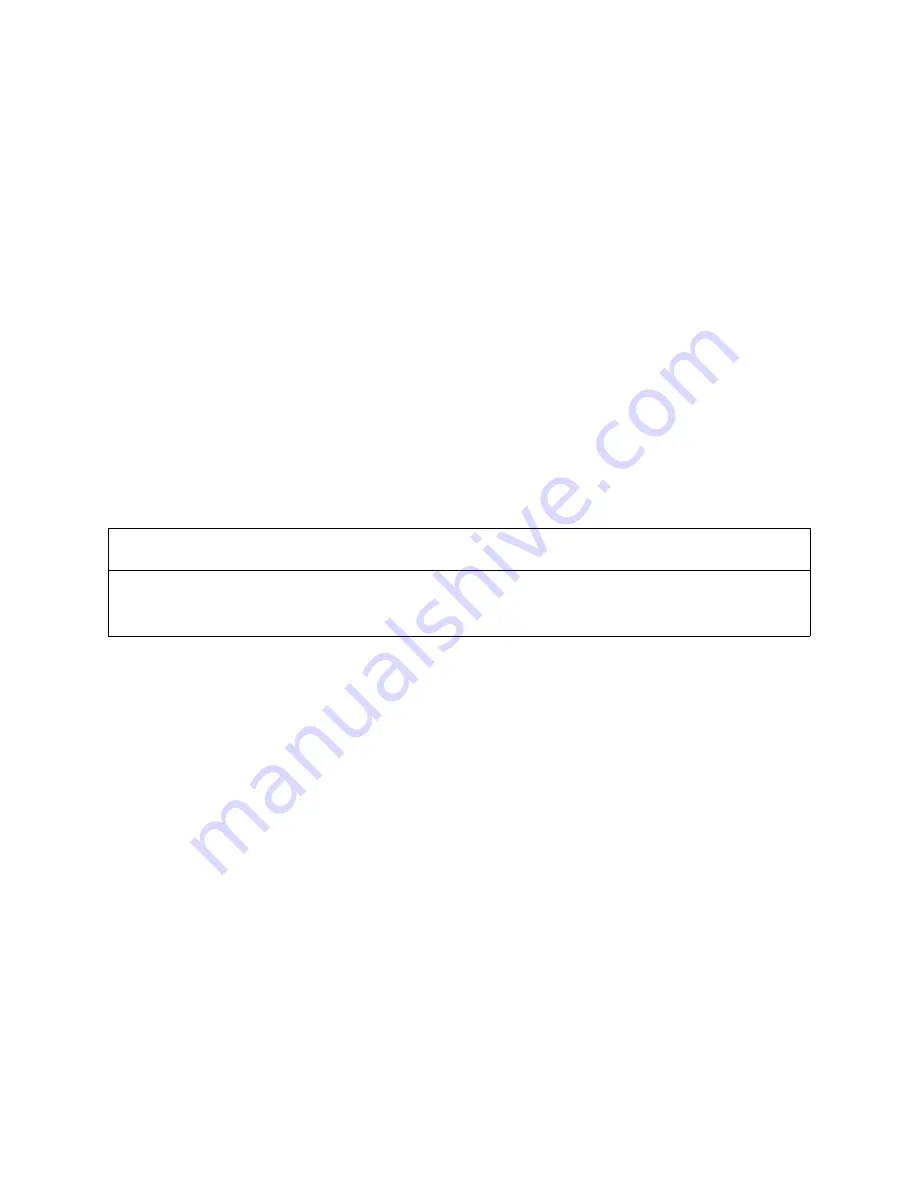
Page 6
General Maintenance Procedures
Return to Master Table of Contents
HYDRAULIC SYSTEM CLEANLINESS AND OIL LEAKS
MAINTENANCE PRECAUTIONS FOR HYDRAULIC SYSTEM SERVICE
Whenever m aintenance, r epairs or any othe r typ e o f tr oubleshooting o r se rvice i s bei ng performed, it ’s
important to r emember th at the hydraulic system – including both t he interior an d exterior s urfaces o f
assemblies, and every drop of operating fluid – must be protected from contamination.
Dust and other foreign contaminants are major contributors to premature wear in h ydraulic circuits. The
narrow tolerances, rapidly moving parts and high operating pressures of the system require that fluid be
kept as cl ean as pos sible. The pe rformance and dependability of the ma chine (and the service li ft of
individual components) can be noticeably reduced if proper precautions are not observed:
•
Use a s afe, n on-combustible, e vaporative-type, l ow-residue sol vent an d tho roughly c lean
exterior surfaces of assemblies before any part of the circuit is opened up or disassembled.
NOTE:
It’s just as important to clean the cap and reservoir top before routine fluid changes or
quick c hecks a s i t is bef ore ma jor r epairs. ( Accumulated d irt attr acts mo isture, oi l an d
other fluids – as well as more dirt.)
•
Keep dismantled parts covered during disassembly. Use clean caps, plugs or tape to protect the
disconnected openings of flanges, manifolds and piping.
•
Do not allow cleaning solvents or other fluids to mix with the oil in the system. Use clean oil to
flush any traces of solvent or other residue before reassembly.
•
If metal or rubber fragments are found in th e system, flush and replace all fluid in the system
and troubleshoot the circuit to identify the source of contamination.
OIL LEAKAGE PRECAUTIONS
Oil that is visibly seeping from joints or seals should always serve as a “red flag” alarm.
Leaks must alert the machine operator and maintenance crew that air, water and dirt have an open, free
passageway through which to enter the circuit. Harsh, corrosive salt air, freezing and thawing condensation
cycles and working environments that are ful l of fi ne dus t ar e es pecially ha zardous. Clogging of valve
spools o r e xternal piping (especially pil ot c ircuit piping) c an g radually dim inish or very s uddenly pu t a
complete stop to nor mal hydraulic func tion. You ca n prevent having to mak e the se ty pes of repairs by
following recommended assembly procedures:
1.
Use new O-rings and oil seals whenever hydraulic assemblies are rebuilt.
2.
Prepare joint surfaces prior to assembly by checking alignment and flatness. Clean and repair
corrosion or any other damage.
3.
Follow bolt torque recommendations and all other assembly requirements.
IMPORTANT
Make sure that cleaning solvents will be compatible with rubber materials used in the hydraulic
system. Many petroleum based compounds can cause swelling, softening, or other deterioration
of system sealing elements, such as O-rings, caps and other seals.
Summary of Contents for Solar 200W-V
Page 1: ...Shop Manual 2023 7139E Serial Number 0001 and Up March 2000 Solar 200W V...
Page 3: ......
Page 6: ...Return to Master Table of Contents 1SAFETY...
Page 28: ...S0102020 Page 22 Wheel Excavator Safety Return to Master Table of Contents...
Page 29: ...Return to Master Table of Contents 1SPECIFICATIONS...
Page 30: ...Return to Master Table of Contents...
Page 37: ...S0202040 Page 7 Specifications for Solar 200W V Return to Master Table of Contents...
Page 57: ...Return to Master Table of Contents 1GENERAL MAINTENANCE...
Page 58: ...Return to Master Table of Contents...
Page 72: ...S0302000 Page 14 General Maintenance Procedures Return to Master Table of Contents...
Page 85: ...Return to Master Table of Contents 1UPPER STRUCTURE...