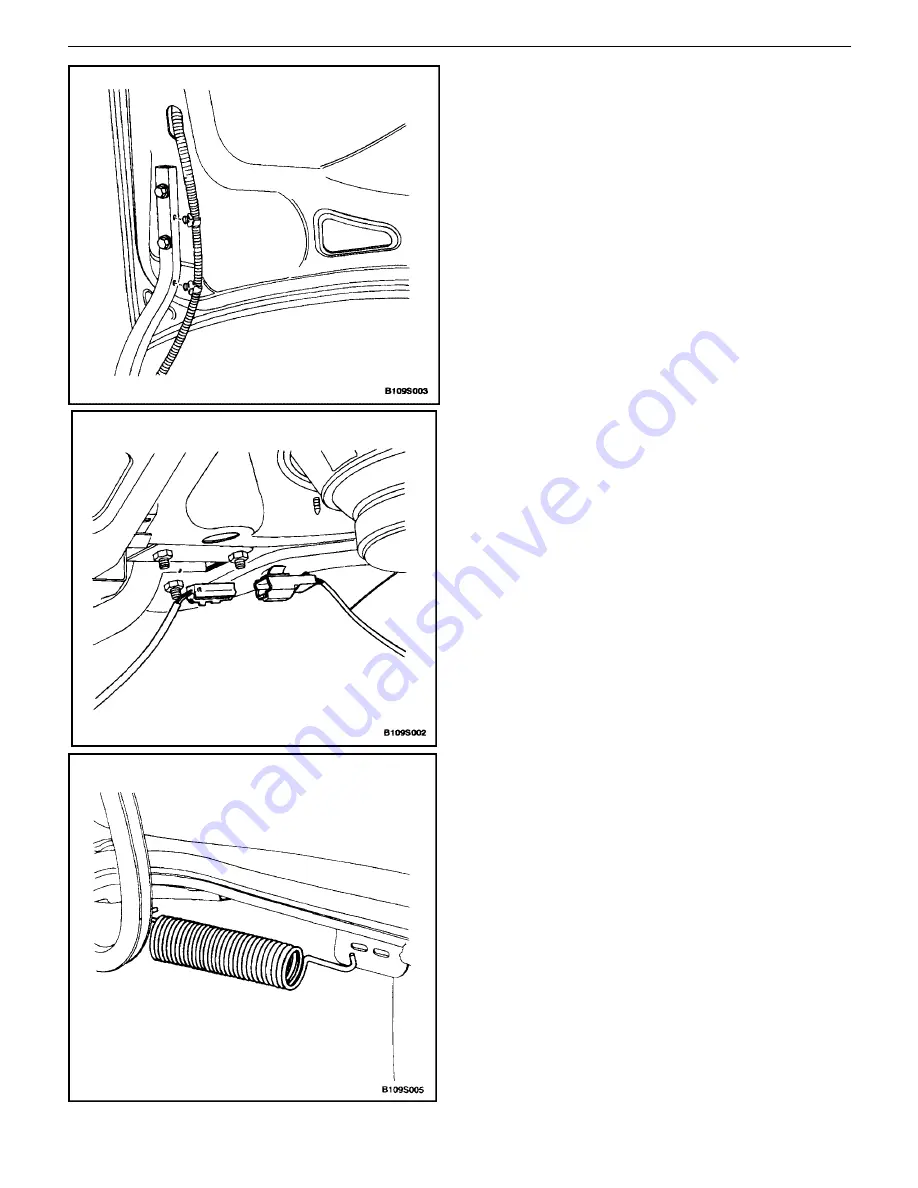
BODY REAR END 9S – 5
DAEWOO V–121 BL4
2. Install the electrical harness to the rear deck lid
hinge arm.
3. Connect the electrical connector.
4. Connect the negative battery cable.
REAR DECK LID SPRINGS
(NOTCHBACK)
Removal Procedure
1. Raise and support the deck lid in the open position.
2. Pull the spring out of the rear mount.
3. Remove the spring from the hinge.
Summary of Contents for NUBIRA
Page 1: ......
Page 26: ...GENERAL INFORMATION 0B 25 DAEWOO V 121 BL4 ...
Page 27: ...0B 26IGENERAL INFORMATION DAEWOO V 121 BL4 Vehicle Lifting Points ...
Page 46: ...1C 8IDOHC ENGINE MECHANICAL DAEWOO V 121 BL4 COMPONENT LOCATOR UPPER END ...
Page 48: ...1C 10IDOHC ENGINE MECHANICAL DAEWOO V 121 BL4 LOWER END ...
Page 140: ...1F 16IENGINE CONTROLS DAEWOO V 121 BL4 PCM ECM WIRING DIAGRAM 2 OF 6 IPCM 6KD ISFI 6TD ...
Page 141: ...ENGINE CONTROLS 1F 17 DAEWOO V 121 BL4 PCM ECM WIRING DIAGRAM 3 OF 6 IPCM 6KD ISFI 6TD ...
Page 142: ...1F 18IENGINE CONTROLS DAEWOO V 121 BL4 PCM ECM WIRING DIAGRAM 4 OF 6 IPCM 6KD ISFI 6TD ...
Page 143: ...ENGINE CONTROLS 1F 19 DAEWOO V 121 BL4 PCM ECM WIRING DIAGRAM 5 OF 6 IPCM 6KD ISFI 6TD ...
Page 144: ...1F 20IENGINE CONTROLS DAEWOO V 121 BL4 PCM ECM WIRING DIAGRAM 6 OF 6 IPCM 6KD ISFI 6TD ...
Page 145: ...ENGINE CONTROLS 1F 21 DAEWOO V 121 BL4 CONNECTOR END VIEW ...
Page 146: ...1F 22IENGINE CONTROLS DAEWOO V 121 BL4 ...
Page 147: ...ENGINE CONTROLS 1F 23 DAEWOO V 121 BL4 ...
Page 148: ...1F 24IENGINE CONTROLS DAEWOO V 121 BL4 ...
Page 149: ...ENGINE CONTROLS 1F 25 DAEWOO V 121 BL4 ...
Page 150: ...1F 26IENGINE CONTROLS DAEWOO V 121 BL4 COMPONENT LOCATOR ...
Page 160: ...1F 36IENGINE CONTROLS DAEWOO V 121 BL4 ...
Page 251: ...SECTION 3 WIRING DIAGRAM FOR POWER SUPPLIES ...
Page 252: ...3 2WWIRING DIAGRAM FOR POWER SUPPLIES 1 IGNITION SWITCH CIRCUIT ...
Page 255: ...WIRING DIAGRAM FOR POWER SUPPLIESW3 5 4 ENGINE ROOM FUSE RELAY CIRCUIT ...
Page 256: ...3 6WWIRING DIAGRAM FOR POWER SUPPLIES ...
Page 257: ...WIRING DIAGRAM FOR POWER SUPPLIESW3 7 ...
Page 271: ...SECTION 4 USAGE AND CAPACITY OF FUSES ...
Page 345: ...ANTILOCK BRAKE SYSTEM 4F 5 DAEWOO V 121 BL4 SCHEMATIC AND ROUTING DIAGRAMS ABS CIRCUIT 1 OF 4 ...
Page 346: ...4F 6IANTILOCK BRAKE SYSTEM DAEWOO V 121 BL4 ABS CIRCUIT 2 OF 4 ...
Page 347: ...ANTILOCK BRAKE SYSTEM 4F 7 DAEWOO V 121 BL4 ABS CIRCUIT 3 OF 4 ...
Page 348: ...4F 8IANTILOCK BRAKE SYSTEM DAEWOO V 121 BL4 ABS CIRCUIT 4 OF 4 ...
Page 363: ...SECTION 5 ELECTRICAL WIRING DIAGRAMS ...
Page 381: ...5A 16I4T40 E AUTOMATIC TRANSAXLE DAEWOO V 121 BL4 POWERTRAIN CONTROL MODULE 2 OF 3 ...
Page 382: ...4T40 E AUTOMATIC TRANSAXLE 5A 17 DAEWOO V 121 BL4 POWERTRAIN CONTROL MODULE 3 OF 3 ...
Page 392: ...FIVE SPEED MANUAL TRANSAXLE 5B 9 DAEWOO V 121 BL4 COMPONENT LOCATORS GEARS AND CASE ...
Page 395: ...5B 12IFIVE SPEED MANUAL TRANSAXLE DAEWOO V 121 BL4 SHIFT LINKAGE ...
Page 402: ...5C0 6ICLUTCH DAEWOO V 121 BL4 1 Flywheel 2 Clutch Disc 3 Pressure Plate 4 Release Bearing ...
Page 470: ...9A 2IBODY WIRING SYSTEM DAEWOO V 121 BL4 POWER DISTRIBUTION SCHEMATIC ...
Page 471: ...BODY WIRING SYSTEM 9A 3 DAEWOO V 121 BL4 ...
Page 475: ...BODY WIRING SYSTEM 9A 7 DAEWOO V 121 BL4 REAR HARNESS ROUTING ...
Page 476: ...9A 8IBODY WIRING SYSTEM DAEWOO V 121 BL4 FRONT HARNESS ROUTING ...
Page 477: ...BODY WIRING SYSTEM 9A 9 DAEWOO V 121 BL4 FLOOR HARNESS ROUTING ...
Page 478: ...9A 10IBODY WIRING SYSTEM DAEWOO V 121 BL4 INSTRUMENT HARNESS ROUTING ...
Page 479: ...BODY WIRING SYSTEM 9A 11 DAEWOO V 121 BL4 DOOR HARNESS ROUTING ...
Page 483: ...9B 4ILIGHTING SYSTEMS DAEWOO V 121 BL4 PARKING TAIL POSITION AND LICENSE LAMPS CIRCUIT ...
Page 484: ...LIGHTING SYSTEMS 9B 5 DAEWOO V 121 BL4 TURN AND HAZARD LAMPS CIRCUIT ...
Page 485: ...9B 6ILIGHTING SYSTEMS DAEWOO V 121 BL4 BRAKE AND BACKUP LAMPS CIRCUIT ...
Page 487: ...9B 8ILIGHTING SYSTEMS DAEWOO V 121 BL4 HEADLAMPS CIRCUIT ...
Page 488: ...LIGHTING SYSTEMS 9B 9 DAEWOO V 121 BL4 DAYTIME RUNNING LAMPS CIRCUIT ...
Page 489: ...9B 10ILIGHTING SYSTEMS DAEWOO V 121 BL4 FOG LAMPS CIRCUIT ...
Page 511: ...9C 2IHORNS DAEWOO V 121 BL4 SCHEMATIC AND ROUTING DIAGRAMS HORN WIRING SYSTEM ...
Page 517: ...WIPERS WASHER SYSTEMS 9D 3 DAEWOO V 121 BL4 WIPERS AND WASHER SYSTEM HATCHBACK ...
Page 561: ...9F 2IAUDIO SYSTEMS DAEWOO V 121 BL4 SCHEMATIC AND ROUTING DIAGRAMS AUDIO SYSTEM CIRCUIT ...
Page 603: ...DOORS 9P 3 DAEWOO V 121 BL4 SCHEMATIC AND ROUTING DIAGRAMS POWER DOOR LOCKS ...
Page 604: ...9P 4IDOORS DAEWOO V 121 BL4 POWER WINDOWS FRONT AND REAR ...
Page 637: ...9Q 2IROOF DAEWOO V 121 BL4 SCHEMATIC AND ROUTING DIAGRAMS POWER SUNROOF SYSTEM ...
Page 710: ...CRUISE CONRTOL SYSTEM 9U 3 DAEWOO V 121 BL4 CRUISE CONTROL SYSTEM AUTOMATIC TRANSAXLE 2 OF 2 ...
Page 711: ...9U 4ICRUISE CONRTOL SYSTEM DAEWOO V 121 BL4 CRUISE CONTROL SYSTEM MANUAL TRANSAXLE 1 OF 2 ...
Page 712: ...CRUISE CONRTOL SYSTEM 9U 5 DAEWOO V 121 BL4 CRUISE CONTROL SYSTEM MANUAL TRANSAXLE 2 OF 2 ...
Page 743: ......
Page 744: ......