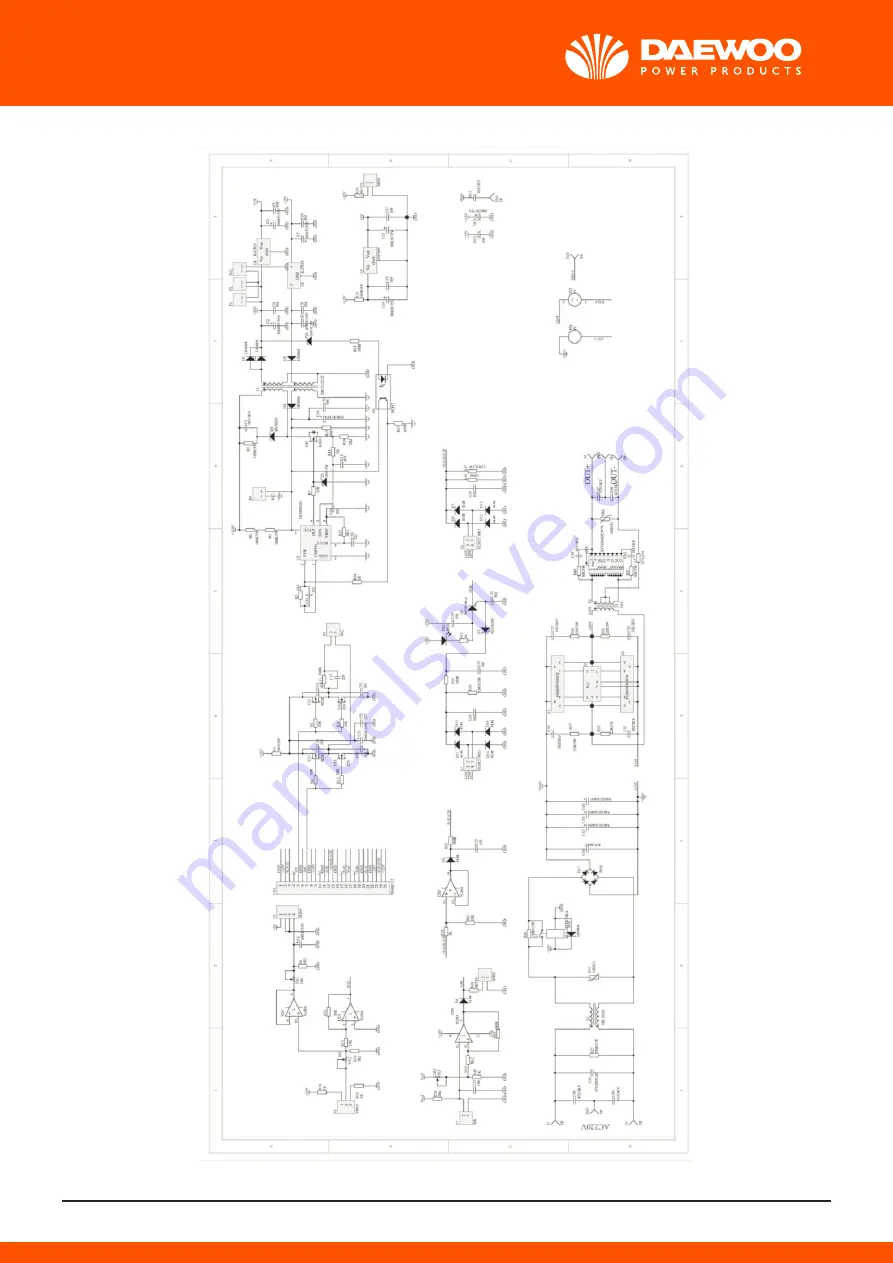
13
1. SAFETY CAUTION
On the process of welding, there will be any possibility of injury, so please take protection into
consideration during operation. More detail please review the Operator Safety Guide, which com-
plies with the preventive requirements of the manufacturer.
Electric shock——may lead to death
!!
• Set the earth fitting according to applying standard.
• It is forbidden to touch the electric parts and electrode when the skin is naked,
wearing wet gloves or clothes.
• Make sure you are insulated from the ground and the workshop.
• Make sure you are in safe position.
Gas —— may be harmful health!
• Keep your head out of the gas.
• When arc welding, air extractor should be used to prevent from breathing gas.
• Use enough forced ventilation or local exhaust (forced suction) at
• the arc to remove the fumes from your breathing area.
Arc radiation —— Harmful to your eye and burn your skin
!
• Use suitable helmet and light filter, wear protective garment to protect eye and body.
• Use suitable helmet or curtain to protect looker-on.
Fire
• Do not weld near flammable material or where the atmosphere may contain
flammable dust, gas, or liquid vapors.
Noise —— extreme noise harmful to ear
!
• Use ear protector or others means to protect ear.
• Warn that noise harmful to hearing if looker – on around.
• Wear approved safety glasses with side shields under your
• Welding helmet or face shield and at all times in the work area.
• Wear complete body protection. Wear oil-free protective clothing
such as leather gloves, heavy shirt, cuffless pants, and high boots.
• Do not weld on containers that have held combustibles, or on closed containers
such as tanks, drums, or pipes.
(
Lifting devices) Small and light welder can be hold by
hand, and heavier one can be moved by it's wheels. The package of welder is carton
box and wooden case. There are no lifting devices on the welder and user need to use
the forklift to take it to the right place and then unpacked.
• Make sure that all the accessories are been dismantled.
• Forbid to stand below the machine when transport.
• It is strictly prohibited to crane fast moving.
• Don't put the machine placed 35 degree in slope.
MMA
• Do not touch live electrical parts.
• Do not use AC weld output in damp, wet, or confined spaces,
or if their is a danger of falling.
• Use AC output ONLY if required for the welding process.
• If AC output is required, use remote output control if present on unit.
• Protect yourself from electric shock by insulating yourself from work and ground.
Use non-flammable, dry insulating material if possible, or use dry rubber mats, dry
wood or plywood, or other dry insulating material big enough to cover your full area
of contact with the work or ground, and watch for fire.
• Disconnect input plug or power before working on machine.
Malfunction —— When trouble, count on the professionals
!
• If trouble in installation and operation, please follow this manual instruction to check up.
• If fail to fully understand the manual, or fail to solve the problem with the instruction, you should
contact the suppliers or our service center for professional help.
CAUTION!
Creepage-protecting switch should be added when using the machine!!
2. MACHINE DESCRIPTION
The welding machine is a rectifier adopting the most advanced inverter technology.
Inverter welding power source utilizes high-power component IGBT to transfer 50/60HZ frequency
up to 30KHZ, then reduce the voltage and commutate, and output high-power voltage via PWM
technology. Because of the great reduce of main transformer’s weight and volume, the efficiency
increases by 30%. The appearance of inverter welding equipment is considered to be a revolution
for welding industry.
The welding power source can offer stronger, more concentrated and more stable arc. When stick
and work piece get short, its response will be quicker. It means that it is easier to design into
welding machine with different dynamic characteristics, and it even can be adjusted for specialty to
make arc softer or harder.
The welding machine has the following characteristics : effective, power saving, compact, stable
arc, good welding pool, high no-load voltage, good capacity of force compensation and multi-use. It
can weld stainless steel, alloy steel, carbon steel, copper and other color metal. It can apply to in
high altitude, the open air and inside and outside decoration. Compared with the same products of
home and abroad, it is compact in volume light in weight, easy to install and operate.
Thanks for purchasing the product and hope for your precious advice. We will dedicate to produce
the best products and offer the best service.
3. SPECIFICATIONS
MINI SERIES
PROFESSIONAL SERIES
4. INSTALLATION INSTRUCTIONS
The induction power is equipped with power voltage compensation function. When rated output
voltage moves /-15%, it still can work normally.
When use long cable
,
you must choose bigger section cable to prevent the voltage drop
;
If cable is
too long, it may heavily influence the performance of the arc striking and the other power system. So
we suggest u use our recommend length.
1. Make sure the intake is not blocked or covered to prevent the cooling system couldn’t work.
2. Choose the cable which section is not less than 4mm²to connect the housing to the ground.
3. Correctly connect the electrode holder and earth clamp as the following sketch.
4. Pay attention to the polarity, DC welder have 2 connecting ways : positive connection and negati-
ve connection .Positive connection
:
holder connects with “-”polarity .While work piece connects
with “+”.Negative connection depends on different work piece and technical requirement. If unsuita-
ble choice, it will cause unstable arc, more spatters and conglutination. If such problems occur,
please change the polarity of the fastening plug.
5. Connect the power line to the distribution box according to the input voltage classes of the
welding machine, don’t connect the wrong voltage. And u must confirm that the input voltage within
bounds.
INSTALL SKETCH
If the distance of work piece and welder is too far (50-100m), and the cables (torch cable and earth
cable) are too long, please choose cable for bigger section to minimize the reduction of the voltage.
5. PANEL FUNCTION DESCRIPTION
MINI Series panel function description
1. Digital screen
2. Power
3. O.C
4. Potentiator
5. Output end negative pole
6. Output end positive pole
MINI Series back panel description
1. Input cable and infix
2. Power switch
PROFESSIONAL DW160LMMA/DW200LMMA
Panel function description
1. Digital screen
2. O.C
3. Potentiator
4. Output end positive pole
5. Output end negative pole
Back panel description
1. Input cable and infix
2. Power switch
PROFESSIONAL DW200XLMMA /DW250XLMMA
Panel function description
1. Digital screen
2. O.C
3. Arc force
4. Potentiator
5. Output end positive pole
6. Output end negative pole
Back panel description
1. Input cable and infix
2. Power switch
Turn the switch to “ON” on the front panel , the digital screen show the current that u set.
At the same time the cooling fan should twirled then u can confirm the welder is
been turned on.
1. Adjust the welding current and thrust current according to the thickness of the welding work
piece, the diameter of the electrode and the requirement of the station and workmanship.
2.Clip the electrode to the electrode holder, then the machine is on a standby mode for the manual
welding.
The relationship from electrode and current
6. NOTICE AND PRECAUTIONS
1. Environment
1) Welding should be done under an environment relatively dry, and air humidity less than 90%.
2) Environment humidity from -10
℃
to 40
℃
.
3) Avoid welding under strong sunshine and raining , never make water or rain into the welding
machine
4) Avoid welding operation in dusty and corrosive air environment.
5) Avoid welding in strong air flowing environment.
2. Safety Cautions
This welding machine fitted with over voltage ,over current,overt heat protection. The machine will
stop work when voltage, output current ,or humidity inside over the standard.But overtimes to use
the machine under non-standard (e.g.: Over voltage ) will shorter the life of the machine even to
break the machine .So please make cautions as following :
1) Make sure a good air flow.
As it is a DIY machine ,there will be high current during welding , in-fitted fan meets the request of
the cooling the machine . Operator need to make sure the fan works well and keep space less than
0.3m with around objets.
2) Prohibit Overload
Keep the welding current less than the max overload current. Over current will shorter the life of the
machine even to make the machine broken.
3) Prohibit Over voltage
If voltage over the allowed value, may cause machine to break,operator should have good unders-
tanding and take preventive measures.
4) Every machine fitted with an earth connecting screw marking with a label. Choose a wire more
than 6mm2 to do the earth connection before operation.
5) The machine will stop if over duty cycle during welding,this caused by thermal control and the
indicator on the front panel will light . At this moment , you don't need to turn off the machine, keep
the machine work and fan inside will make the machine cooling . The machine work again after the
indicator turn off.
7. MAINTENANCE
WARNING:
All maintenance, repair work must be completely cut off the power,
make sure the machine is unplugged in to the power before opening the case.
1. Blow the dust with dry air regularly. Operator need remove the dust very day if welding in dense
smoke and serious polluted air.
2.The air flow should be in reasonable pressure ,too strong flow will destroy some small compo-
nents.
3. Avoid water or steam into the machine.Operator needs to dry the machine when this situation
happed.Then to measure the insulation with an ohmmeter. Ensure everything is OK , then start to
welding.
4. Packing up the machine to relatively dry environment if not using frequently.
Overhaul precautions
WARNING:
Blind experiments and imprudent overhaul may lead to the expansion of the area
of the fault,cause difficulties to the formal overhaul. The equipment in an energized state
machine within the exposed part with can lead to dangerous voltage, any direct or indirect
contact may lead to electric shock accidents, serious electrical shock will result in death! ! !
Note:
During the warranty period, the user repairs without authorization or error repair, the free
repair warranty provided by the suppliers will be invalidated.
8. TROUBLE SHOOTING
The phenomenon you meet here may have connections with spare parts, welding materials,environ-
ment and supply power ,please take measures to avoid those things.
A
.
Hard to start arc , easy to break arc
:
1. Make sure the welding electrode good quality.
2. The electrode without dealing with drying process may cause arc unstable ,bad
welding quality .
3. The output voltage will decrease when using longer output cables.It's suggested
using shorter output cables.
B
.
Output current can not meet the rated value
:
Unrated power supply will cause output value not match the rated value data.
C
.
The current not stable during welding process.
This situation may caused by the following:
1. The supply voltage not stable.
2. Disturbed by the supply voltage
D
.
More sparks
:
1. Using small electrode with high current adjusted .
2. The output polarity reversed . Under normal conditions , electrode holder connect to negative ,
and the work peace to positive.
WARNING:
Never pull out or insert the plug cable or connector while in the welding process,
this will cause to personal safety and serious damage to equipment.
9
. P
IC
T
U
R
E 1
:
TH
E S
C
H
E
M
A
T
IC O
F W
H
O
L
E M
A
C
H
IN
E