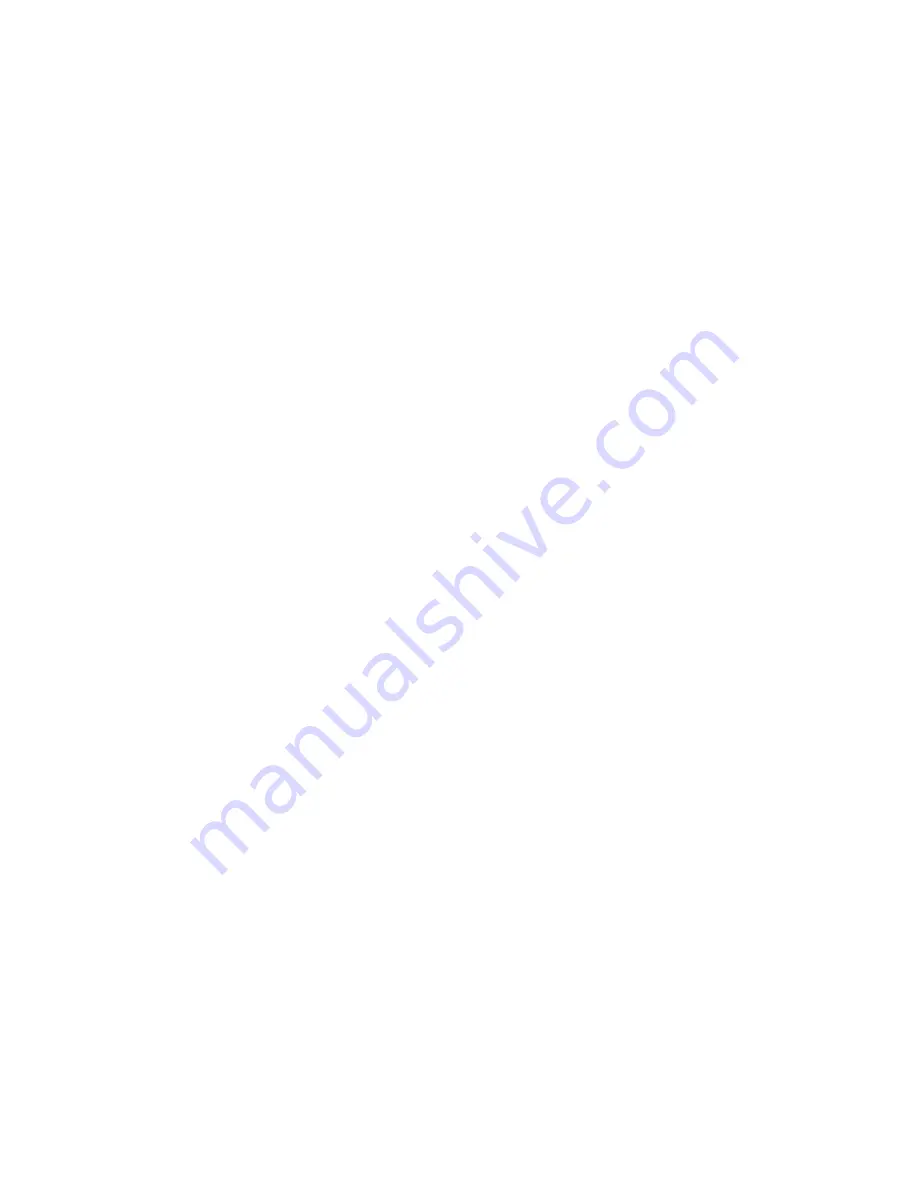
30
Propane samples can use the 1,800 psi CO
2
fluid to actuate the piston. The
over pressurization method should still be followed, but it is unlikely the piston
will need more pressure than 1,800 psi.
Once encapsulation has been achieved it is good practice to go 250 psi
above that to overcome leakage from the NMR cell over extended periods of
time.
Insoluble material is common even in good samples. Stop the stir bar and
allow the insoluble material to settle to properly observe the sample.
The insoluble material should be allowed to settle prior to transferring the
sample to the NMR cell.
After the sample has been transferred, and the NMR cell closed, the cell
should be inverted several times to help solubilize any reagents that may
have fallen out of solution during the transfer.
The pressure in the NMR cell can be increased after it has been closed.
Reconnect the NMR cell to the OUTLET/INLET valve using the transfer line.
Open the OUTLET/INLET valve and pressurize the mixing chamber to the
encapsulation pressure or the new pressure desired. Open the NMR cell
valve and let the system equilibrate to the new pressure. Close the NMR cell
valve, and the OUTLET/INLET valve. Disconnect and check the sample at
the new pressure.
Use the piston to perform test increases in pressure in the mixing chamber.
This may be preferable to adding additional solvent and diluting the sample
unnecessarily.
No matter how good the seals, the system will leak over time. If the system
will not be used for several weeks it is good idea to retract any deuterated
solvents from the RM Synthesizer, into the syringe pump, and then push that
fluid back into the alkane cylinder.
Occasionally the stir bar becomes lodged in the surfactant slurry. It can be
dislodged using a strong magnet; either on the side of the mixing chamber or
balanced along the edge of the mixing chamber cap.
Typical CTAB samples encapsulate around 4,000 psi, AOT above 8,000 psi,
and a triple surfactant mix consisting of 70% C
12
E
4
, 25% AOT, 5% DTAB
might not encapsulate around 9,000 psi. Around 8,000 psi the viscosity of
ethane is equal to propane so the benefit of working in ethane is lost.