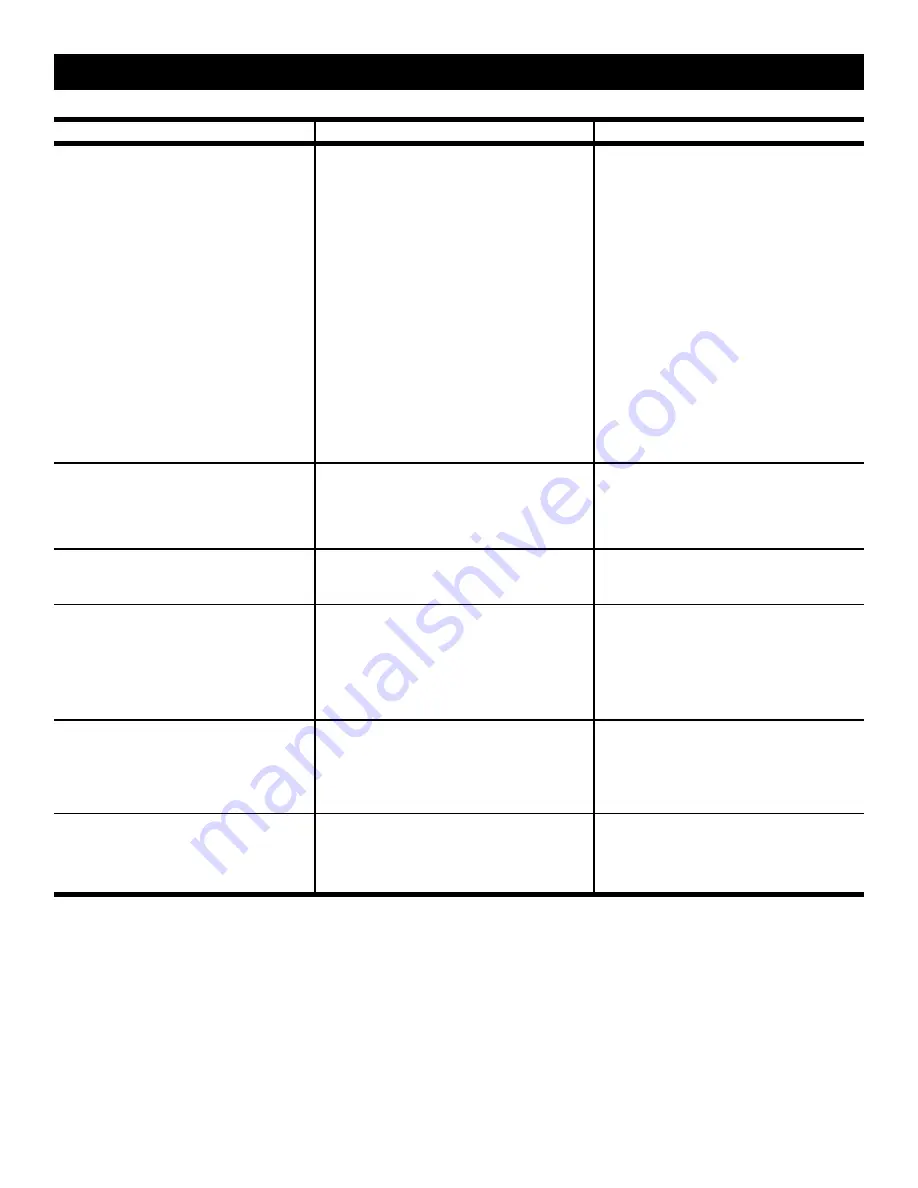
6
TROUBLESHOOTING
SYMPTOM
3. Screen will not move
“up.”
Motor does
not
hum.
Motor
hums.
CAUSE
(a) Blown fuse or tripped circuit
breaker.
(b) No power between red and white
leads in junction box.
(c) Thermal overload tripped.
(d) Burned out motor winding.
(e) Temporary binding.
(f) Burned out capacitor.
(g) Broken wire or loose connection
in
“up”
position circuit.
SOLUTION
(a) Replace fuse or reset circuit
breaker.
(b) Correct improper wiring.
(c) Let motor cool for 15 minutes. Try
again.
(d) Check for power between red
and white motor leads. Replace
motor if there is power.
(e) With power
off,
turn roller by
hand to free binding.
(f) Replace capacitor.
(g) Secure connection or replace
wire.
4. Scraping or grinding noise.
(a) If metal shipping bracket is left at-
tached to screen, it may be rub-
bing on motor end of roller.
(a) Remove shipping bracket.
6. Fabric rubbing.
(a) Normal condition.
NOTE: Screens with ironing boards
have fabric that drags across the
board.
7. Incorrect stopping point in
upward
position.
(a) Lost roller wrap.
(b) Limit switch out of adjustment.
(a) Lift bottom edge up and over
roller.
(b) See installation instructions.
8. Incorrect stopping point in
downward
direction.
(a) Lost roller wrap.
(b) Limit switch out of adjustment.
(a) See above.
(b) See installation instructions.
5. Gear noise.
(a) Gear may need lubrication.
(a) Apply grease.