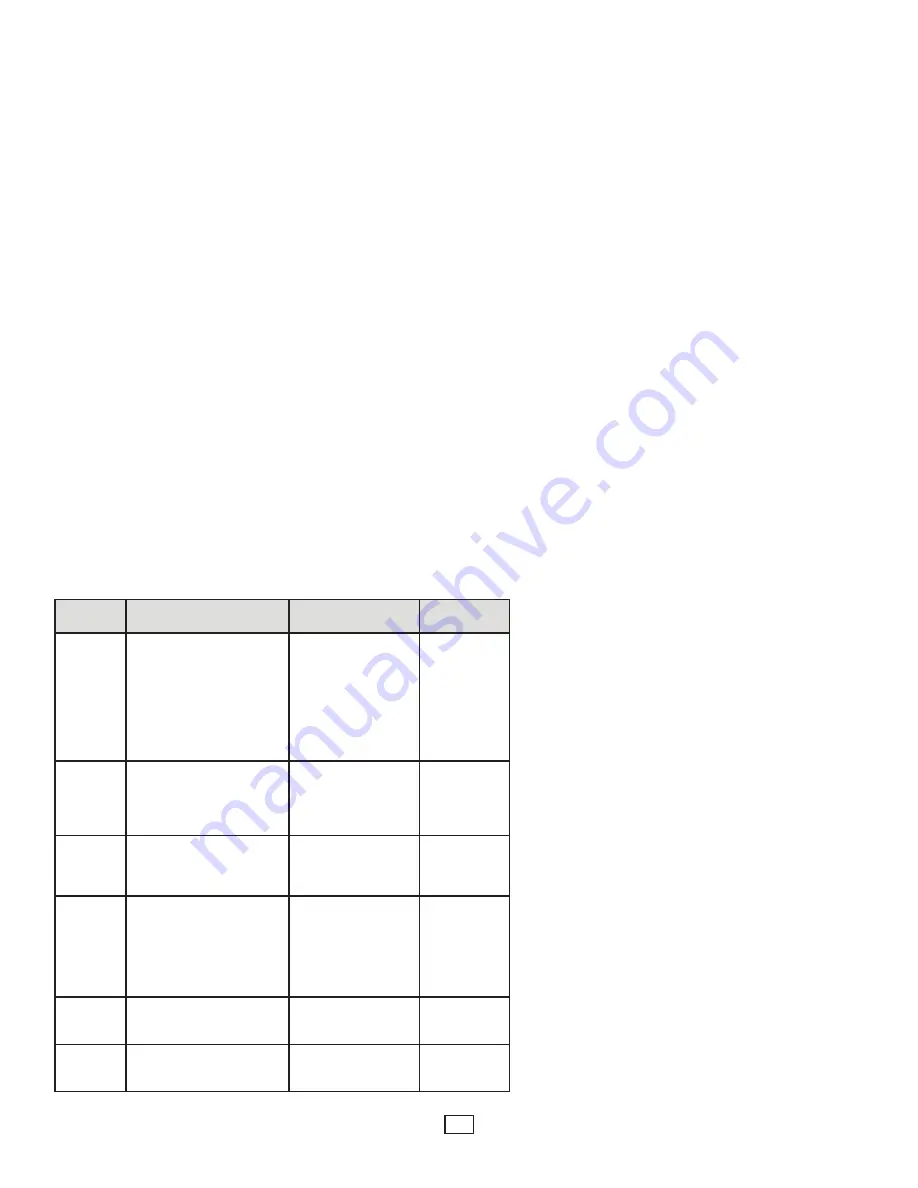
9
WHAT IS THE PROPER USE OF THE NOZZLE THREAD CHASER TAP?
All D/F Nozzles are hand checked for fit before and after plating, and checked again before shipping. If a nozzle has been installed on a
new complete torch, they have also been hand checked while being assembled.
The only reason to ever take a gas cup out a nozzle is to clean it. The nozzle and the gas cup must be blown out, and all of the threads
have to be wire brushed and blown out again before hand-tightening the gas cup back into the nozzle. If you can’t thread it in by hand
then something is wrong. Never force a gas cup into a nozzle.
When using the D/F Machine Specialties nozzle thread chaser taps, be sure to always follow the steps below:
Make sure that the nozzle is properly supported when tapping so it does not twist in the front of the torch body and cause damage.
1.
Improper support can cause the spigots to twist off the top of the rear nozzle collar, or damage the torch internal body parts.
•
Note where the water ports go down the sides of the water-cooled nozzle (following down in line with the spigots). Too much direct
•
pressure on these water ports could cause them to cave in and block of the flow of water.
Best practice is to hold the water-cooled nozzle in a vice with soft jaws, perpendicular to the spigots.
•
Over-tightening of the vice can cause damage in general.
•
Remove the tip from the front of the torch before tapping.
2.
Lightly lubricate the nozzle and nozzle thread chaser tap before tapping.
3.
Be sure to start the tap very carefully. Do not cross thread the nozzle.
4.
Be very careful to start threads correctly. Only tap 1/2 turn at a time, always backing up and removing chips 1/2 cycle at a time before
5.
moving forward. Do not try to tap further into the water-cooled nozzle than needed or past the factory thread depth.
Blow out the nozzle after tapping. Wire brush and blow off the gas cup before threading it back into the nozzle.
6.
If nozzle is badly deformed or damaged please return to the factory for a repair estimate before disposing of product (damaged parts
7.
can often be repaired).
CODE NO.
DESCRIPTION
USED WITH
NOZZLE ASSEMBLY
USED FOR
GAS NOZZLE
14610
Nozzle Thread Chaser Tap
for Standard A/C & W/C
Nozzle Assembly Front
13197
16184
11117, 45101
11118, 45102
11119, 45103
45114
45107
NCC-N/HTC-N
NCC-LRN, HTC-LRN
10340
10359
10362
10374
14611
Nozzle Thread Chaser Tap
for BIG MIG & BIG TIG
Nozzle Assembly Front
11123
10382
10387
10389
10390
10392
14612
Nozzle Thread Chaser Tap
for Nozzle Body
Assembly Rear
13196
13197
13198
16184
14614
Nozzle Thread Chaser Tap
for Series A High-Capacity
Nozzle Assembly Front
11142, 45120
11138, 45121
45127
11132, 45129
45125
16748
16749
16750
16751
18030
18031
18032
14615
Nozzle Thread Chaser Tap
for Nozzle Body
Assembly Front
13198
10379
14617
Nozzle Thread Chaser Tap
for Tandem Nozzle
Assembly Front
41641
41667
41668
ORDERING INFORMATION - NOZZLE THREAD CHASER TAPS
Summary of Contents for MAC
Page 7: ...REQUIRED TOOLS LIST FOR DISASSEMBLY ASSEMBLY 7 ...
Page 21: ......