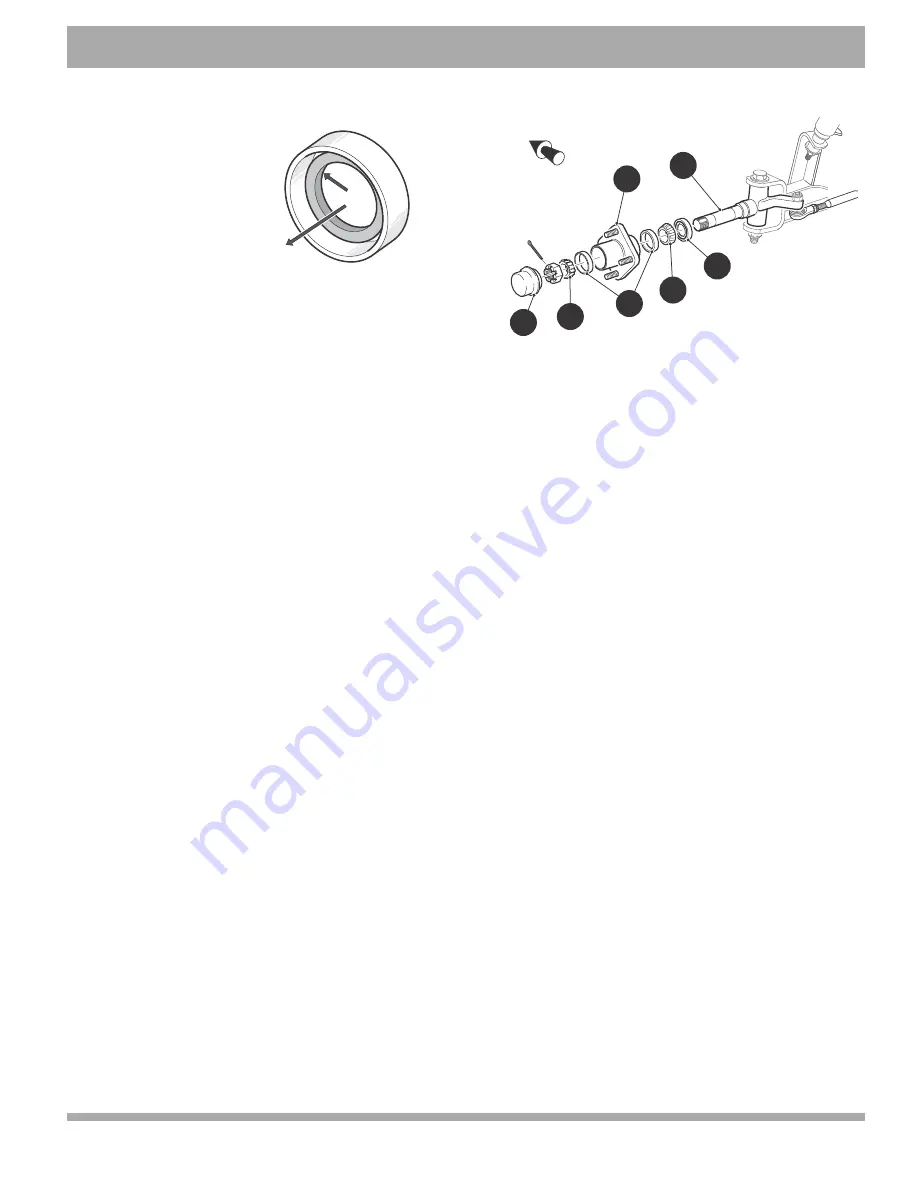
B
FRONT SUSPENSION AND STEERING
Read all of SAFETY and this section before attempting any procedure. Pay particular attention to Notices, Cautions, Warnings and Dangers.
27
Repair and Service Manual
634756
Fig. 12 Seal Installation
Place new hub onto spindle and fill the area between the
two wheel bearings about 1/2 - 3/4 full with grease and
apply a light coating to the outer bearing race.
Install outer wheel bearing (4) and secure hub loosely
with castellated nut. Place wheel onto hub and hand
tighten lug nuts.
Adjust bearing. See “Wheel Bearing Adjustment” on
page 21.
Replace the dust cap (1).
Lower vehicle per SAFETY section. Tighten front
wheel(s) per WHEELS AND TIRES section.
Wheel Bearing and Race Replacement
Tool List
Qty.
Non-Ferrous Punch ..................................................... 1
Ball Peen Hammer ...................................................... 1
Bearing Driver ............................................................. 1
Remove hub (1) from spindle (Ref. Fig. 13). See “Hub
Replacement” on page 26.
Remove grease seal (3), inner wheel bearing (4) and
bearing races (5) by tapping (through the other side of
hub) the bearing race with a hammer and soft non-ferrous
punch. Tap race in a circular pattern while moving from
side to side to avoid damaging bore of hub.
Clean outer wheel bearing (6), inner wheel bearing (4),
hub and dust cap (7) in solvent and dry thoroughly.
Inspect for signs of damage. Pitting or a blue coloration of
the rollers indicates bearing replacement is required. If
the roller portion of the bearing is to be replaced, the race
must also be replaced.
To install race (5), make sure bore of hub (1) is clean and
place new race over bore of hub. Evenly tap with hammer
and bearing driver to drive race fully in bore. Repeat on
other side of hub.
Clean spindle (2) and pack new bearings with grease.
See “Wheel Bearing Packing” on page 20.
Fig. 13 Wheel Bearing Replacement
Install inner wheel bearing (4) and new grease seal in hub
and mount hub to spindle. See “Wheel Bearing Adjust-
ment” on page 21. Adjust bearing. See “Wheel Bearing
Adjustment” on page 21.
Replace dust cap (7).
Lower vehicle per SAFETY section. Tighten front
wheel(s) per WHEELS AND TIRES section.
B
A - Install this side of seal
into housing
B - Lubricate lip of seal
A
Front of Vehicle
1
4
7
2
3
6
5