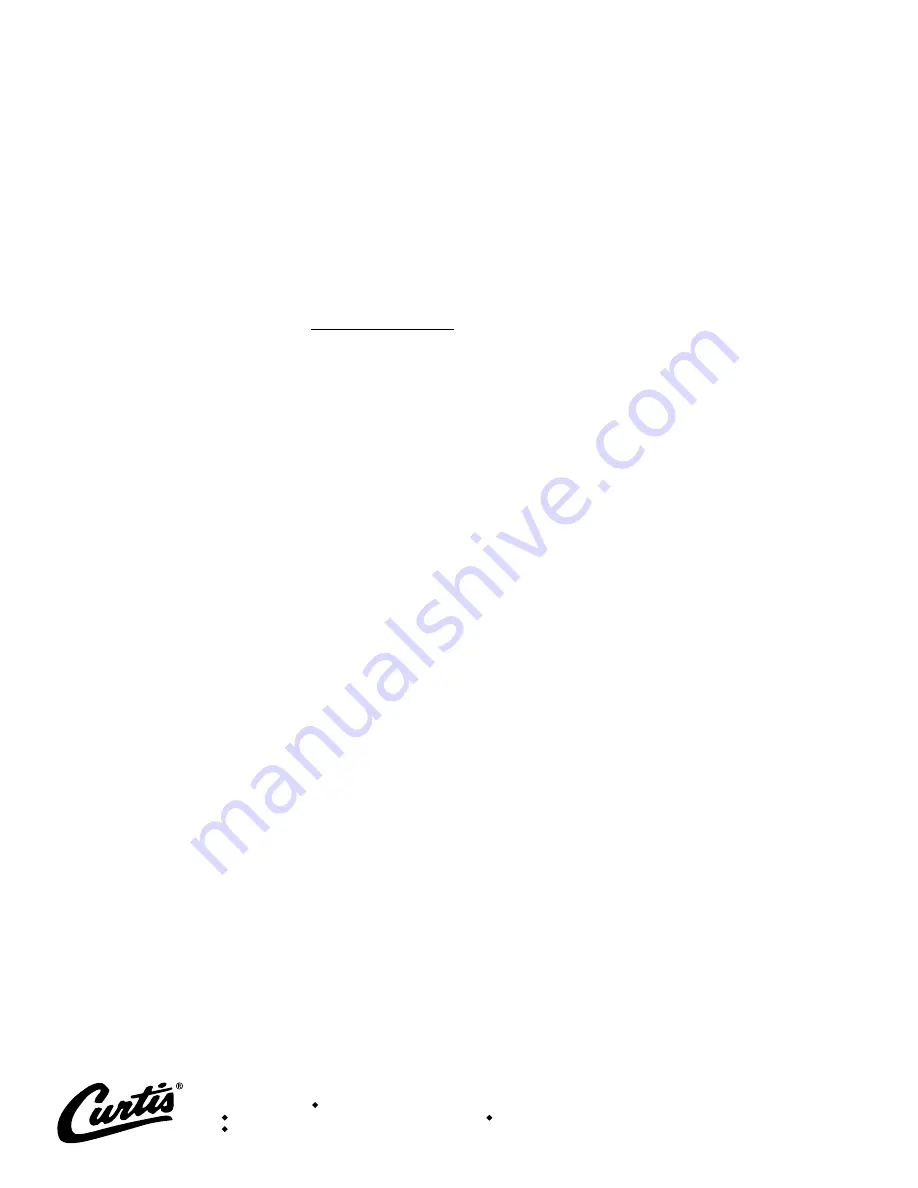
Product Warranty Information
The Wilbur Curtis Company certifies that its products are free from defects in material and workmanship under normal
use. The following limited warranties and conditions apply:
3 Years, Parts and Labor, from Original Date of Purchase on digital control boards.
2 Years, Parts, from Original Date of Purchase on all other electrical components, fittings and tubing.
1 Year, Labor, from Original Date of Purchase on all electrical components, fittings and tubing.
Additionally, the Wilbur Curtis Company warrants its Grinding Burrs for Forty (40) months from date of purchase or
40,000 pounds of coffee, whichever comes first. Stainless Steel components are warranted for two (2) years from date of
purchase against leaking or pitting and replacement parts are warranted for ninety (90) days from date of purchase or for
the remainder of the limited warranty period of the equipment in which the component is installed.
All in-warranty service calls must have prior authorization. For Authorization, call the Technical Support Department at 1-
800-995-0417. Effective date of this policy is April 1, 2003.
Additional conditions may apply. Go to www.wilburcurtis.com to view the full product warranty information.
CONDITIONS & EXCEPTIONS
The warranty covers original equipment at time of purchase only. The Wilbur Curtis Company, Inc., assumes no respon-
sibility for substitute replacement parts installed on Curtis equipment that have not been purchased from the
Wilbur Curtis Company, Inc. The Wilbur Curtis Company will not accept any responsibility if the following conditions are
not met. The warranty does not cover and is void under the following circumstances:
1)
Improper operation of equipment: The equipment must be used for its designed and intended purpose and
function.
2)
Improper installation of equipment: This equipment must be installed by a professional technician and must
comply with all local electrical, mechanical and plumbing codes.
3)
Improper voltage: Equipment must be installed at the voltage stated on the serial plate supplied with this equip-
ment.
4)
Improper water supply: This includes, but is not limited to, excessive or low water pressure, and inadequate or
fluctuating water flow rate.
5)
Adjustments and cleaning: The resetting of safety thermostats and circuit breakers, programming and tempera-
ture adjustments are the responsibility of the equipment owner. The owner is responsible for proper cleaning and
regular maintenance of this equipment.
6)
Damaged in transit: Equipment damaged in transit is the responsibility of the freight company and a claim should
be made with the carrier.
7)
Abuse or neglect (including failure to periodically clean or remove lime accumulations): Manufacturer is
not responsible for variation in equipment operation due to excessive lime or local water conditions. The equipment
must be maintained according to the manufacturer’s recommendations.
8)
Replacement of items subject to normal use and wear: This shall include, but is not limited to, light bulbs,
shear disks, “0” rings, gaskets, silicone tube, canister assemblies, whipper chambers and plates, mixing bowls,
agitation assemblies and whipper propellers.
9)
Repairs and/or Replacements are subject to our decision that the workmanship or parts were faulty and the
defects showed up under normal use. All labor shall be performed during regular working hours. Overtime charges
are the responsibility of the owner. Charges incurred by delays, waiting time, or operating restrictions that hinder the
service technician’s ability to perform service is the responsibility of the owner of the equipment. This includes
institutional and correctional facilities. The Wilbur Curtis Company will allow up to 100 miles, round trip, per in-
warranty service call.
RETURN MERCHANDISE AUTHORIZATION: All claims under this warranty must be submitted to the Wilbur Curtis
Company Technical Support Department prior to performing any repair work or return of this equipment to the factory.
All returned equipment must be repackaged properly in the original carton. No units will be accepted if they are
damaged in transit due to improper packaging. NO UNITS OR PARTS WILL BE ACCEPTED WITHOUT A RETURN
MERCHANDISE AUTHORIZATION (RMA). RMA NUMBER MUST BE MARKED ON THE CARTON OR SHIPPING
LABEL. All in-warranty service calls must be performed by an authorized service agent. Call the Wilbur Curtis
Technical Support Department to find an agent near you.
WILBUR CURTIS CO., INC.
6913 Acco St., Montebello, CA 90640-5403 USA
Phone: 800/421-6150
Fax: 323-837-2410
Technical Support Phone: 800/995-0417 (M-F 5:30A - 4:00P PST)
E-Mail: [email protected]
Web Site: www.wilburcurtis.com
8/06 . F-2049. rev A