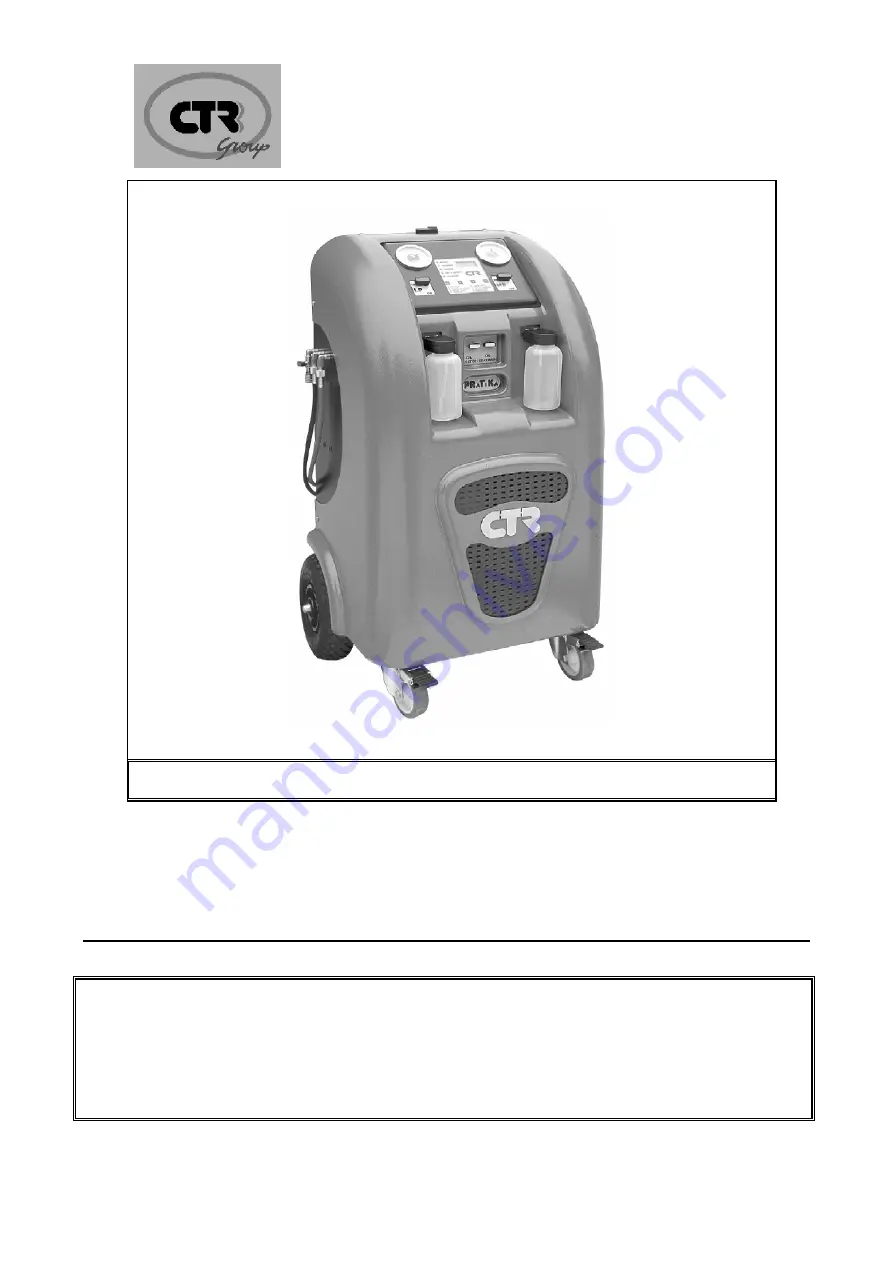
ECOLOGICAL MACHINE DIVISION
User and Maintenance Guide
___________________________________________
PRATIKA
P/N 4018014
Please fully read this User and Maintenance Guide before using the machine.
C.T.R. s.r.l. Via Via T.ed E. Manzini n° 9, 43100 Parma (Italy)
Tel. +39 0521/957611 - Fax. + 39 0521/957677