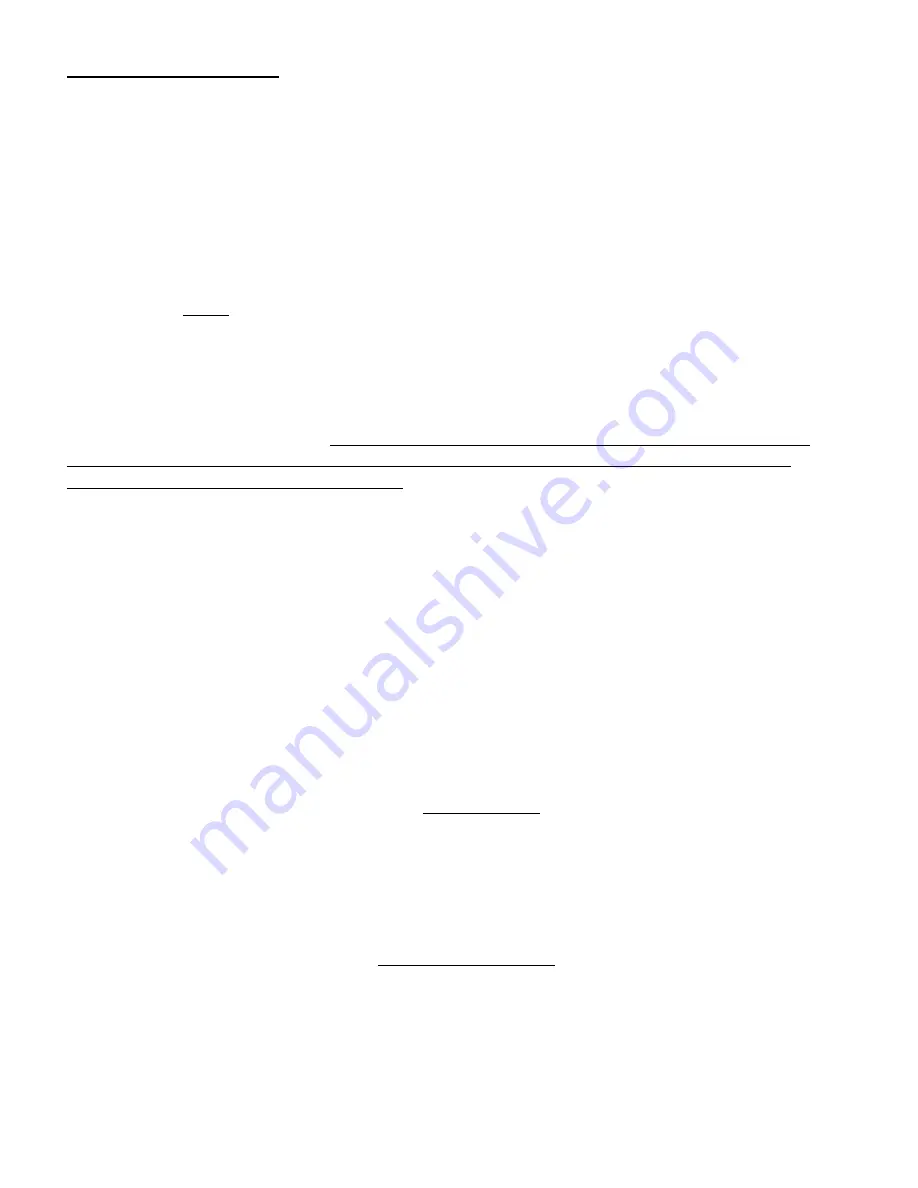
-8-
Single Phase Motor Replacement:
Connect motor leads to T1 and T3 of overload relay for single phase motors. (See wiring diagram for single phase motors
on following page) Green ground wire must be grounded to enclosure. If using type “SO” wire and plug, use a dust tight
connector through Floor Stand and a grounded plug.
Be sure to check
rotation. If a change is necessary, open the motor
box located on the motor, and switch the #8 and the #5 wires. This reverses the rotation of a single phase motor. The
blade must rotate down and to the rear on the underside of the blade (see Picture “A” on Page No. 5).
Three Phase Motor Replacement:
Connect motor line leads to T1, T2, & T3 of the overload relays. (See wiring diagram for three phase motors.) Green
ground wire must be grounded to enclosure.
Be sure to check rotation
as polarities may be different. The blade must
rotate down and to the rear on the underside of the blade (see Picture “A” on Page No. 5). If a change in rotation is
necessary, reverse any two of the incoming power wires.
Example:
If the blades are running backwards and incoming
wires are connected White L1,Black L2,Red L3, switch the Black wire with the Red so that Black is connected to L3
and Red is connected to L2. This will change the blades to rotate properly.
Electrical Installation:
The CTD N80X uses two 2 H.P. single or three phase 3450 RPM, 60 HZ TEFC (totally enclosed fan cooled) motors on
a NEMA 56Z Frame. The N90X uses two 3 H.P. or 5 H.P. three phase 1725 RPM 60 HZ TEFC motors on a 182
Frame. CTD uses a speed up drive so that the blade will run at approximately 3400 RPM for the N80X and 2800 RPM
for the N90X..
Electrical installation should be performed by a qualified and certified electrician. A lock-out or disconnect switch is
located in front of the machine. It is a rotary switch to the left front of the machine. This disconnect switch is used to shut
off power to the machine and should be used whenever the blades are changed or at any time the machine is serviced and
the blades are exposed. A Dual Magnetic Starter, located inside the left side panel of the machine protects the motor from
overheating and will not allow the motor to restart itself after power outages or undervoltage situations. The START button
turns the motors
“ON”. The STOP button turns the motor
“OFF”
.
Note
:
The STOP button must be pulled out before
the START button will activate the motors.
A safety interlock switch is located under the blade guard. The blade guard
must be in place and the safety interlock switch
must be made
or the motors
will not
turn on.
Electrical Installation of Power to Starter by a Qualified Electrician:
All wiring from the motors to the starter has been completed and tested at the factory several times.
The voltage has been clearly tagged.
DO NOT CONNECT ANY VOLTAGE THAT IS DIFFERENT THAN
THE TAGGED VOLTAGE, AS THIS MAY CAUSE SEVERE DAMAGE AND DANGER.. CONSULT
FACTORY IF ANY CHANGES ARE NEEDED.
Bring incoming power lines to the rear of the machine on left side using hard wire and dust proof connectors. Attach
incoming power lines through Floor Stand to the rotary disconnect switch. Connect to terminals 2 & 4 for single phase
motors, and to terminals 2,4 & 6 for three phase motors. Always ground the green wire (See wiring diagram on Page No.
9). The blade must rotate down and to the rear on the underside of the blade (see Picture “A” on Page No. 5). If a
change in rotation is necessary, reverse any two of the incoming power wires.
Example:
If the blades are running
backwards and incoming wires are connected White L1,Black L2,Red L3, switch the Black wire with the Red so that
Black is connected to L3 and Red is connected to L2. This will change the blades to rotate properly.
Summary of Contents for N80X
Page 19: ... 19 ...
Page 20: ... 20 N80 Exploded View Notching Configuration ...
Page 21: ... 21 N 8 0 E x p lo d e d V ie w P a rts L ist ...
Page 22: ... 22 N90 Floor Stand and Blade Guard Exploded View ...
Page 23: ... 23 ...
Page 24: ... 24 ...