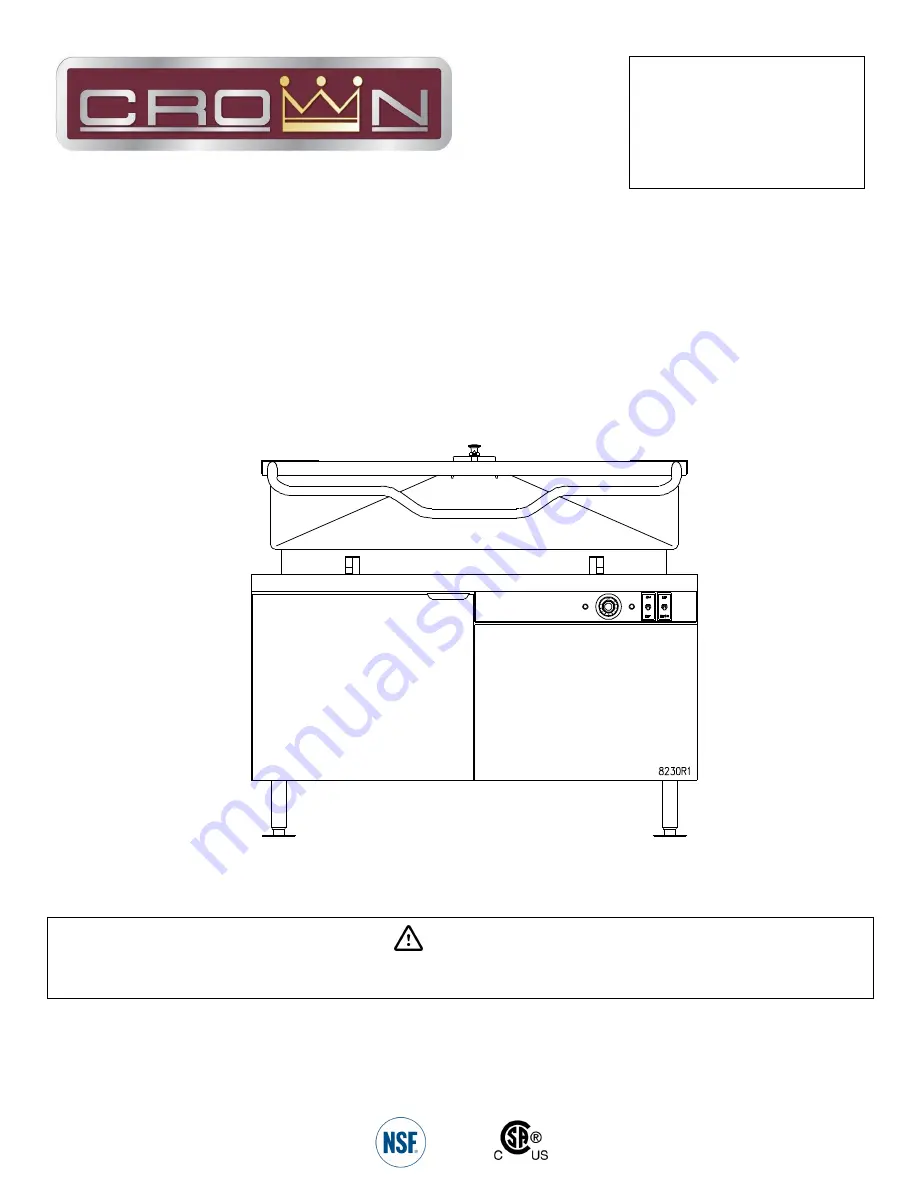
MANUAL
10
130
R
3
INSTALLATION & OPERATION
MANUAL
Electric
Modular
Skille
t
s
E
M
TS-30 E
M
TS-40
EMTS-60
WARNING
Improper installation, adjustment, alteration, service or maintenance can cause property damage, injury or death. Read
the installation, operating and maintenance instructions thoroughly before installing or servicing this equipment.
IMPORTANT FOR FUTURE REFERENCE
Please complete this information and retain this
manual for the life of the equipment:
Model #: ___________________________
Serial #: ___________________________
Date Purchased: ____________________
CROWN FOOD SERVICE EQUIPMENT
Division of Middleby Canada Company Inc
.
70 Oakdale Road, Downsview (Toronto) Ontario, Canada, M3N 1V9
Telephone: 919-762-1000 www.crownsteamgroup.com
Printed in Canada