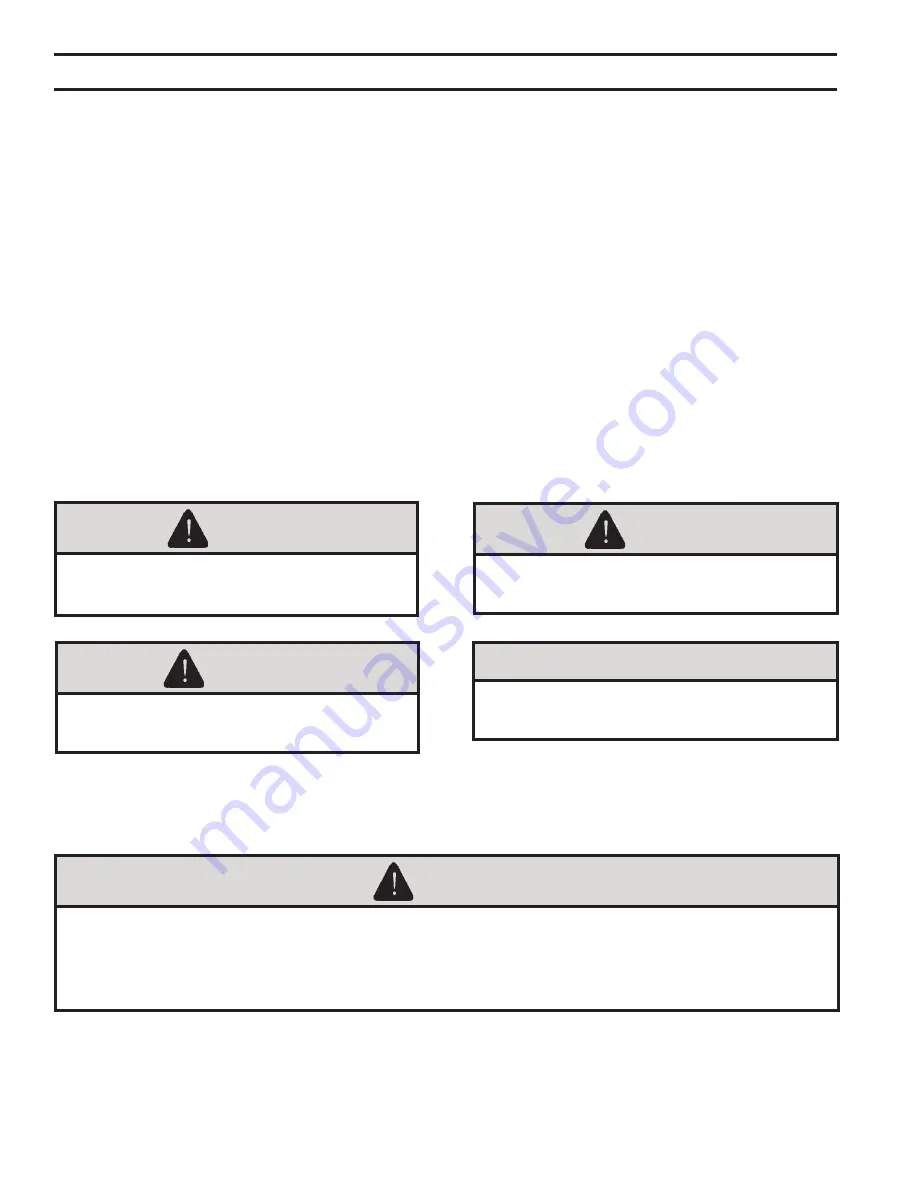
2
IMPORTANT INFORMATION - READ CAREFULLY
NOTE: The equipment shall be installed in accordance with those installation regulations enforced in the area where the
installation is to be made. These regulations shall be carefully followed in all cases. Authorities having jurisdiction
shall be consulted before installations are made.
All wiring on boilers installed in the USA shall be made in accordance with the
National Electrical Code
and/or local regulations.
All wiring on boilers installed in Canada shall be made in accordance with the
Canadian Electrical Code
and/or local regulations.
The following terms are used throughout this manual to bring attention to the presence of hazards of various risk levels,
or to important information concerning product life.
The City of New York requires a Licensed Master Plumber supervise the installation of this product.
The Massachusetts Board of Plumbers and Gas Fitters has approved the Phantom™ Series boiler. See the Massachusetts Board
of Plumbers and Gas Fitters website, http://license.reg.state.ma.us/pubLic/pl_products/pb_pre_form.asp for the latest Approval
Code or ask your local Sales Representative.
The Commonwealth of Massachusetts requires this product to be installed by a Licensed Plumber or Gas Fitter.
DANGER
Indicates an imminently hazardous situation
which, if not avoided, will result in death, serious
injury or substantial property damage.
CAUTION
Indicates a potentially hazardous situation
which, if not avoided, may result in moderate or
minor injury or property damage.
WARNING
Indicates a potentially hazardous situation
which, if not avoided, could result in death,
serious injury or substantial property damage.
NOTICE
Indicates special instructions on installation,
operation, or maintenance which are important
but not related to personal injury hazards.
WARNING
Explosion Hazard. DO NOT store or use gasoline or other flammable vapors or liquids in the vicinity of this
or any other appliance.
If you smell gas vapors, DO NOT try to operate any appliance - DO NOT touch any electrical switch or use
any phone in the building. Immediately, call the gas supplier from a remotely located phone. Follow the
gas supplier’s instructions or if the supplier is unavailable, contact the fire department.
Summary of Contents for PHNTM399
Page 53: ...53 VIII Electrical continued Figure 26 Ladder Diagram...
Page 54: ...54 VIII Electrical continued...
Page 55: ...55 Figure 27 Wiring Connections Diagram VIII Electrical continued...
Page 113: ...113 THIS PAGE LEFT BLANK INTENTIONALLY...
Page 114: ...114 XIII Repair Parts continued PHNTM399 and PHNTM500...
Page 118: ...118...
Page 119: ...119...