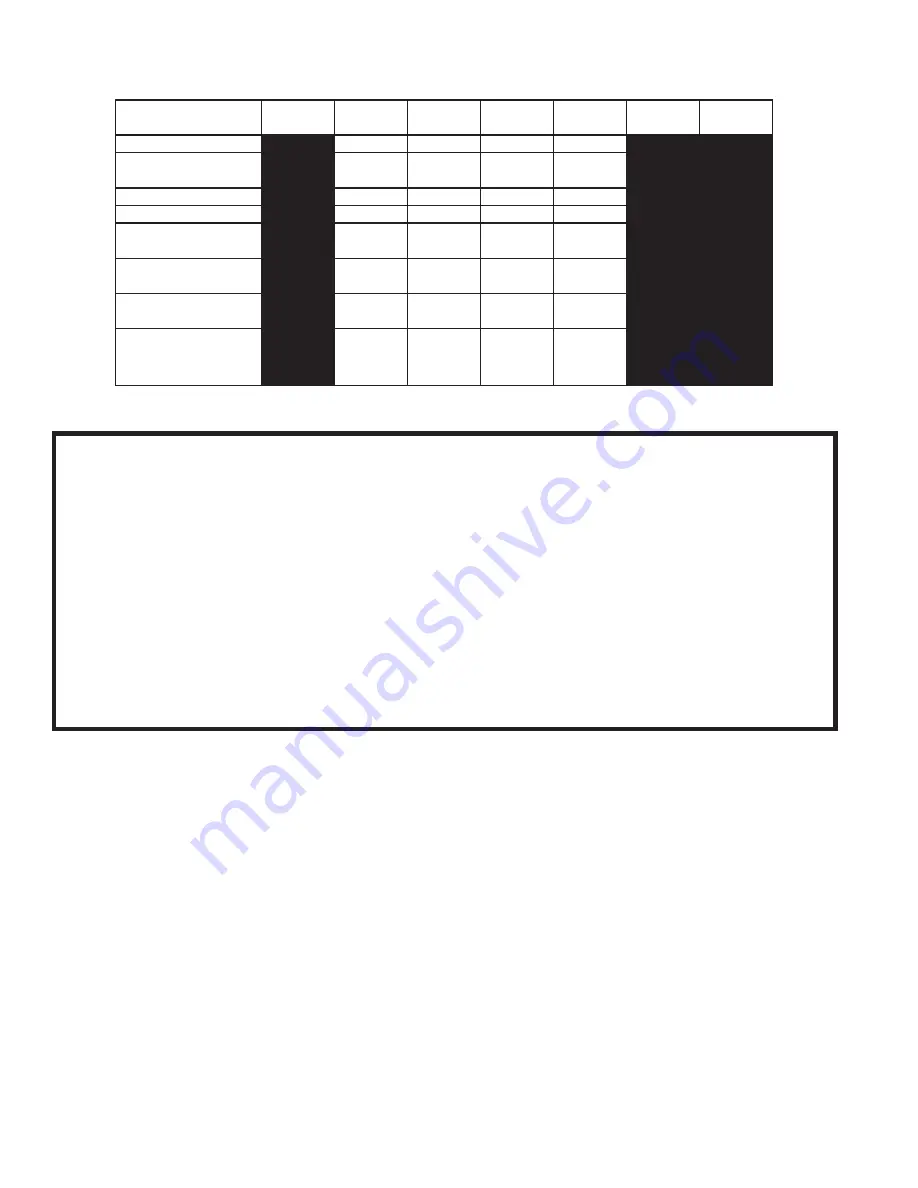
34
XIII Service and Maintenance
The following procedure should be performed on a weekly basis:
For boilers equipped with a float low water cut-off, blow down the low water cut-off following the low water cut-off
manufacturer’s instructions. During this blow down, the low water cutoff should shut down the burner. If it does not, the low
water cut-off should be replaced immediately.
The following procedure should be performed on an annual basis:
1) Turn off electrical power and oil supply to the boiler.
2) Inspect the Hydrolevel CG450 low water cut-off - Remove and inspect the probe for scale and sediment buildup. Clean
any sediment or scale from the probe with a scouring pad or steel wool. Consult the Hydrolevel CG450 manual for any
additional maintenance information. Test the low water cut-off before placing the boiler back into service.
3) Allow the boiler to cool to room temperature and drain the boiler. Remove the 1-1/2” plug from the unused return tapping.
Use a flashlight to inspect the bottom row of pushnipples for accumulated scale or mud. If a significant amount is present, use
the following procedure to clean the inside of the heat exchanger:
TABLE 12.0c: RIELLO BURNER CONFIGURATION AND SETUP DATA
BURNER MODEL
40F5
40F5
40F5
40F5
40F10
40F10
STANDARD
DEL
DEL
DEL.
DEL
HAGO
DEL
NOZZLE
0.60/60A 0.85/60W 1.00/60A 1.25/60B 1.35/45B 1.65/45B
PUMP PRESS (psi)
150
150
150
150
150
150
TURBULATOR
0
2
3
3
1.5
2
AIR
SHUTTER SETTING
2.60
2.85
3.8
4.5
3
3.8
DRAFT OVER FIRE
(in w.c.)
MAX. SMOKE
(bacharach scale)
FLUE CO
2
(%)*
MIN.
11.0
11.0
11.0
11.0
11.0
11.0
MAX
13.0
13.0
13.0
13.0
12.5
12.5
-0.02
#1
#1
#1
#1
BOILER MODEL
KSB200
KSB065
KSB075
KSB100
KSB125
KSB150
KSB175
#1
#1
-0.02
-0.02
-0.02
-0.02
-0.02
* Also see
NOTICE
below
NOTICE
Smoke and CO
2
levels may vary over time as the result of factors such as fuel chemistry, air
temperature, and combustion air contamination. To minimize soot production, and thereby help
assure continued efficient, reliable operation, observe the following precautions:
• Never leave the boiler in operation at a smoke level exceeding #1, even if this means that
the boiler must be operated at a CO
2
level below the maximum shown Table 12.0.
• Never leave the boiler in operation with a CO
2
outside the range shown in Table 12.0, even
if the smoke level at this CO
2
is zero and burner operation otherwise appears OK.
• In cases where field conditions are known to vary significantly, a good practice is to
provide a CO
2
“cushion” between the CO
2
corresponding to a #1 smoke and that at which
the burner is left in operation. The size of this cushion depends on local experience, but is
typically 0.5% - 1.0%. For example, using a 1.0% cushion, if the burner reaches a #1 smoke
at 13.5%, the burner would be left in operation with a CO
2
at or below 12.5%.