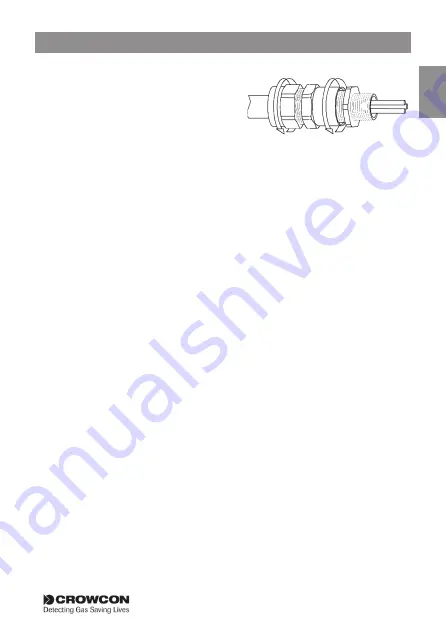
Installation
17
English
Clamping Ring. If armour/braid not
clamped, repeat assembly.
6.
Remove Entry and refi t Inner Seal,
replace Entry and re-assemble Middle
Nut onto the entry component.
Tighten up the Middle Nut by hand
then using a wrench/spanner a further
1 to 4 turns until fully tight.
Notes:
1. These instructions are provided for general guidance only. It is essential
that the instructions provided by the cable gland manufacturer are strictly
adhered to.
2. Only cable glands ATEX and IECEx certifi ed Exd Flameproof may be used
with
Xgard Bright
.
3. Cable glands must have a minimum ingress protection rating of IP66.
Summary of Contents for Xgard Bright
Page 2: ......
Page 4: ......
Page 9: ...Introduction 5 English 1 6 Exploded view Diagram 3 Xgard Bright exploded view...
Page 34: ......
Page 35: ......