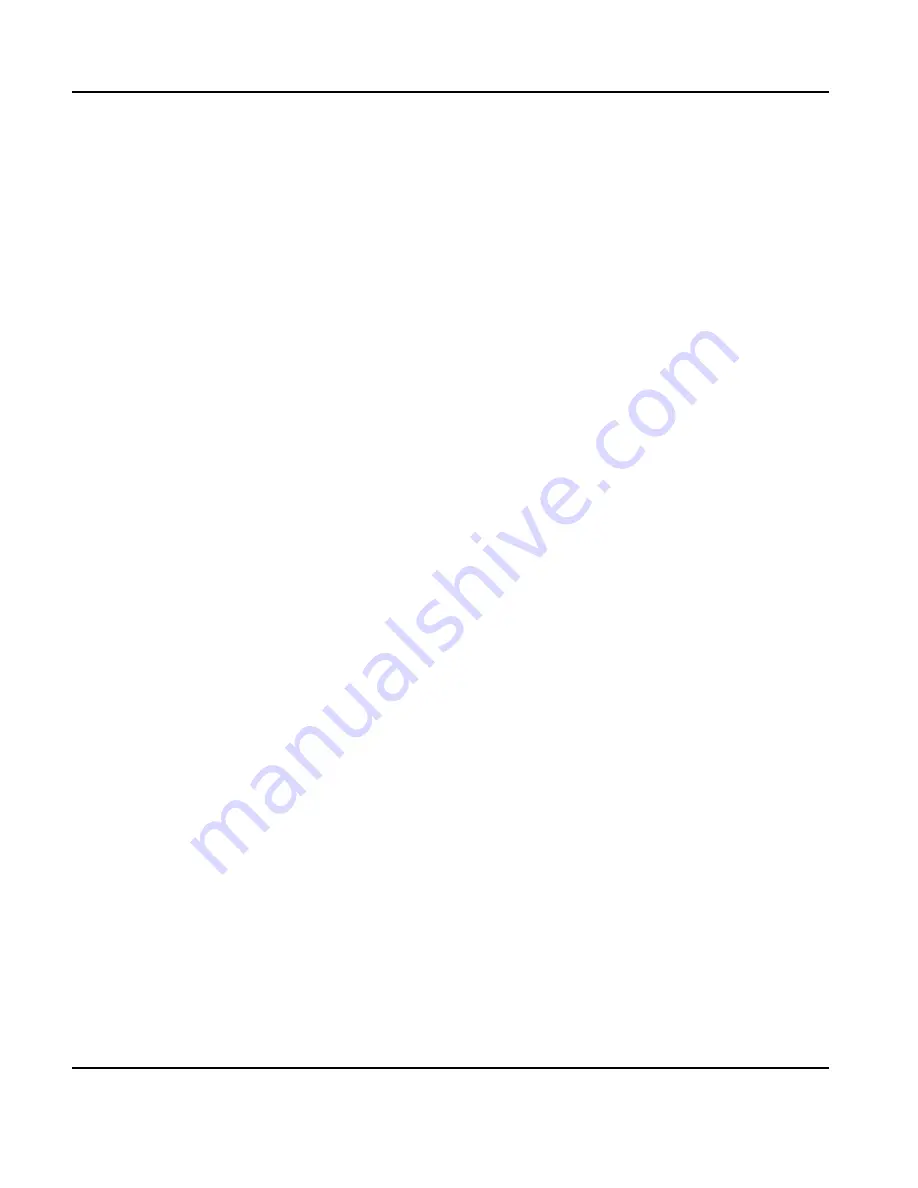
MityDSP-L138 Carrier Board Design Guide
March 5, 2014
Page 16 of 17
Document Revision: 1.7
– MityDSP-L138 Revision 4A
Critical Link reserves the right to make corrections, modifications, enhancements, and other changes to this document at any time and without notice.
5
Board Layout Recommendations
The following sections discuss topics for successful board layouts incorporating any module.
5.1
Placement
Placement of the module site is crucial to a successful carrier board layout. Because the module connector
footprint is fine-pitch and dual-row, it is generally best to place the connector fairly centered in the overall board
layout. This placement allows traces to be routed out from both sides of the connector, using mainly top-side
copper tracks. The use of less signal layers, and therefore less vias, generally results in a more compact design
with better signal integrity than a board using many layers and vias. Of course, ideally central placement is not
always possible because of other mechanical constraints.
Mechanically, enough space must be allocated for the full extension of the module. Although it is possible for a
module to hang over the edge of its carrier board, this may not be desirable if additional mechanical attachment
methods are desired for ruggedness, as discussed in sections 4.3 and 4.4. Another thing to keep in mind with
placement on the carrier board and in enclosures is the cam-in action of the MityDSP modules into their
respective sockets. The modules are generally installed at an angle of about 25° to 30° before swinging down to
locked position. Enclosure designs should accommodate this motion.
5.2
Pin-out and Routing
Care must be taken when routing the SOC high speed interfaces – specifically the USB 1.0 and 2.0 OTG ports and
the SATA ports. Please refer to the specific SOC device specification for guidance related to these pins.
5.3
Access issues
Given that it is possible and often desirable to make best use of available space by placing components
underneath the MityDSP module (refer to section 4.2), hardware and software engineers who will be debugging
code on the platform could find themselves in a tough situation if the component they need to access is blocked
by the installed MityDSP module. Because of these situations it is advisable to either not use the space under
the MityDSP module for active components that might need live probing with the MityDSP in-circuit, or only
place circuits there that are already tried and tested by engineers on other platforms. In the event that an
obscured circuit does need to be probed, it may be necessary to solder temporary wires onto probe points. An
even better solution would be to design the board with bottom-side test points, at least in the MityDSP region, if
this is possible on a given design.
5.4
PCB/PCA Technology
MityDSP modules do not have any specific requirements about the PCB technology used for its carrier board.
The required socket connectors are available as RoHS compliant, and may be used in both leaded and lead-free
assembly processes. The only recommendation is to fabricate the carrier board thick enough to rigidly support