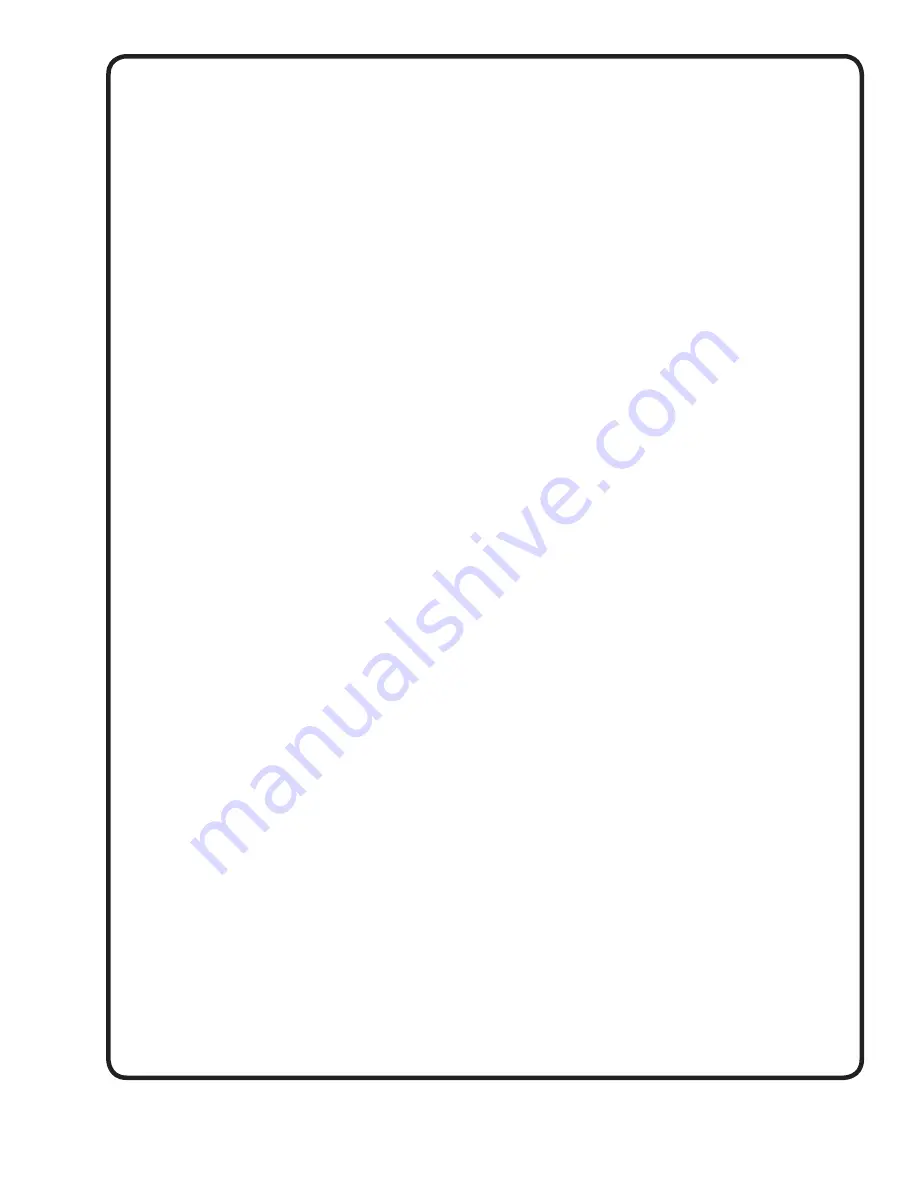
3
A - GENERAL INFORMATION
TO THE PURCHASER:
Congratulations! You are the owner of one of the
fi
nest
pumps on the market today. These pumps are products
engineered and manufactured of high quality components.
With years of pump building experience along with a
continuing quality assurance program combine to produce
a pump which will stand up to the toughest applications.
Check local codes and requirements before installation.
Servicing should be performed by knowledgeable pump
service contractors or authorized service stations.
RECEIVING:
Upon receiving the pump, it should be inspected for
damage or shortages. If damage has occurred,
fi
le a claim
immediately with the company that delivered the pump.
If the manual is removed from the crating, do not lose or
misplace.
STORAGE:
Short Term -
Pumps are manufactured for ef
fi
cient
performance following long inoperative periods in storage.
For best results, pumps can be retained in storage, as
factory assembled, in a dry atmosphere with constant
temperatures for up to six (6) months.
Long Term -
Any length of time exceeding six (6) months,
but not more than twenty four (24) months. The units
should be stored in a temperature controlled area, a roofed
over walled enclosure that provides protection from the
elements (rain, snow, wind blown dust, etc..), and whose
temperature can be maintained b40 deg. F and
+120 deg. F. Pump should be stored in its original shipping
container and before initial start up, rotate impeller by hand
to assure seal and impeller rotate freely.
SERVICE CENTERS:
For the location of the nearest Weinman Service Center,
check your Weinman representative or Crane Pumps &
Systems, Inc., Service Department in Piqua, Ohio, telephone
(937) 778-8947 or Crane Pumps & Systems Canada, Inc.,
Bramton, Ontario, (905) 457-6223.
B - INSTALLATION
These pumps are designed for pumping raw or treated
sewage, light sludge, Industrial wastes, drainage and
similar liquids containing solids.
MOUNTING:
The pump has been assemble, adjusted and lubricated
at the factory before shipment. Refer to “Lubrication” for
proper lubrication of the shaft seal and motor bearings.
Pumps may be installed on any suf
fi
ciently solid support
since pump and motor are rigidly aligned. The Fig. 7171-
7172 series pumps may be mounted in a vertical position,
with the motor above the pump liquid end, if vertical
mounting is preferred.
PIPING:
Suction and discharge piping should be direct with as
few
fi
ttings as possible. Pipe and
fi
ttings must be properly
supported near the pump so their weight does not
cause strain on the pump
fl
anges.
DO NOT
pull pipes
into position with
fl
ange bolts as this may cause pump
misalignment. Flexible connectors should have limiting
bolts to contain hydraulic forces.
PUMP ROTATION:
Pumps may be furnished for right hand (clockwise) or left
hand (counter-clockwise) rotation when viewed from above
the motor. See rotation arrow and pump name-plates.
Connect power leads to motor according to motor wiring
diagram and jog starter testing for rotation. If rotation is
incorrect, rotation may be reversed by interchanging any
two main power leads at starter (3 phase only).
PRIMING:
It is important that all trapped air be removed from the
suction pipe and pump casing before operating the pump.
A. On Fig. ULL remove the pipe plug (216) at the top
of the casing (1)
B. On Fig. ULL-VM remove pipe plug (208) from
adapter (71). Replace pipe plug after the liquid rises
and displaces all air.
LUBRICATION:
These pumps are normally
fi
tted with a double mechanical
shaft seal. The seal chamber of the adapter (71) must be
pressurized with a clean, compatible liquid to cool and
lubricate the seal faces.
For optimum service, the liquid should be circulated thru
the seal chamber at a pressure equal to or 15 to 20 PSI
higher than the maximum pressure at the pump discharge.
Lubrication may be provided by one of the following
methods.
A. With liquid from the pump discharge to the seal
chamber thru a
fi
lter assembly having a 25 micron
fi
lter.
B. With clean compatible liquid, under pressure, from
an outside source.
C. With water seal unit to provide clean water, under
pressure, from a potable source of supply.
Motor bearings should have periodic lubrication and
inspection according to the motor manufacturer’s
recommendations.
Summary of Contents for Weinman ULL - 7181
Page 12: ...Notes ...