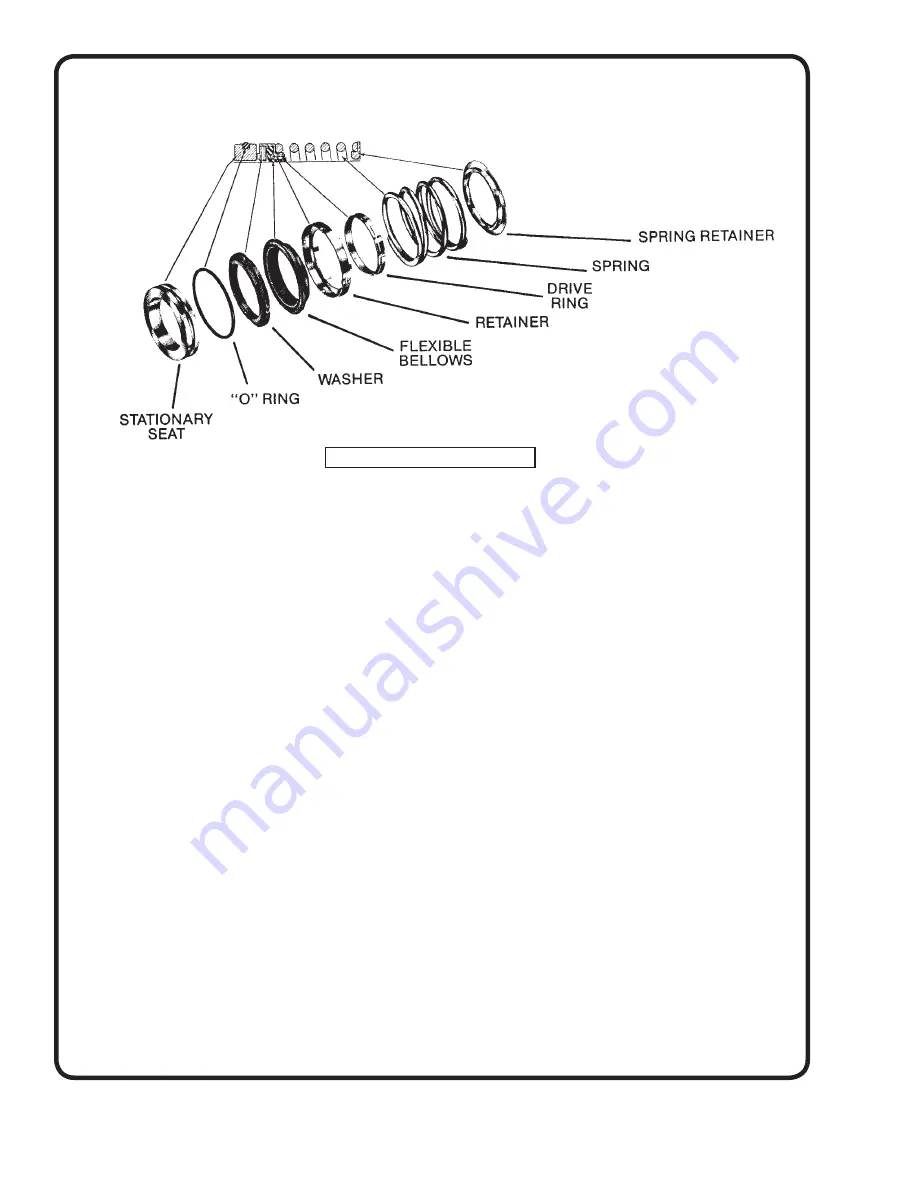
4
REASSEMBLY
Reassembly will generally be in reverse order of
disassembly. If disassembly was not complete, use only
those steps related to your particular repair program.
1.
The sleeve must be checked for abrasion, damage
during disassembly, or corrosion that can occur
when
fl uid residue penetrates between the seal (80)
and sleeve (14). The sleeve under the seal should
be lightly polished to a 32 RMS fi nish before
reassembly.
Do not
reuse a pitted or damaged
sleeve. Slide the sleeve (14) on the motor shaft (6).
2.
The mechanical seal (80) (See Figure 2) cannot be
installed as an assembly. It is necessary to have the
seal seat properly in place before the balance of
parts can be added. Thoroughly inspect the seal
cavity in the bracket for burrs or nicks which could
damage the seat of the seal. Apply a fi lm of soap
paste
or
fl ax soap
(Do not use oil or grease)
to
the seal seat and install, taking care to seat it evenly
and
squarely.
NOTE:
If it is not possible to insert seal with fi ngers, place
cardboard protecting ring furnished with seal over lapped
face of seat and press into place with a piece of tubing
having end cut square. The tubing should be slightly larger
than diameter of the shaft. Remove cardboard after seat is
fi rmly in place.
3.
Position casing cover (11) on the motor and secure
with capscrews (83). Tighten screws evenly to
assure proper alignment.
4.
Wipe the sealing faces of the seat and seal washer
clean. Oil these surfaces with a clean light oil. Lightly
oil the shaft sleeve (14). Slide the entire mechanical
seal rotating assembly onto the sleeve.
5.
Press wearing rings (25) and (27) into the casing
(1) and casing cover (11). Rings should not be
hammered into place. Use a press, or clamp the
parts in a bench wise, using wooden blocks to
protect the rings. It may be necessary to pin or
dowel the rings after assembly if the insert or casing
has had rings replaced before, since each
reassembly can stretch or tear metal and thereby
loosen
the
fi ts.
6.
Assemble key (32) and impeller (2) to motor shaft.
Secure impeller (2) to motor shaft. Secure impeller
(2) with washer (28) and impeller screw (26).
7.
Install all drain plugs in the casing. Position the
gasket (73) and casing (1) against the casing cover
(11) and secure with screws (82).
8. Repalce
all
fl ushing or drain lines. Connect
discharge piping and suction piping if required,
making sure to install gaskets on the fl anged
connections. Connect electric power to motor.
STARTING PUMP AFTER REASSEMBLY
Do not pump until all air and vapor has been bled. Make
sure that there is liquid in the pump to provide the neces-
sary lubrication, (Without the fl uid around it, the seal may
be ruined in a few seconds of operation). It is possible that
the mechanical seal may drip during the fi rst few minutes
to one hour of operation.
Figure 2 - MECHANICAL SEAL
Summary of Contents for WEINMAN 6012CV
Page 8: ...Notes ...