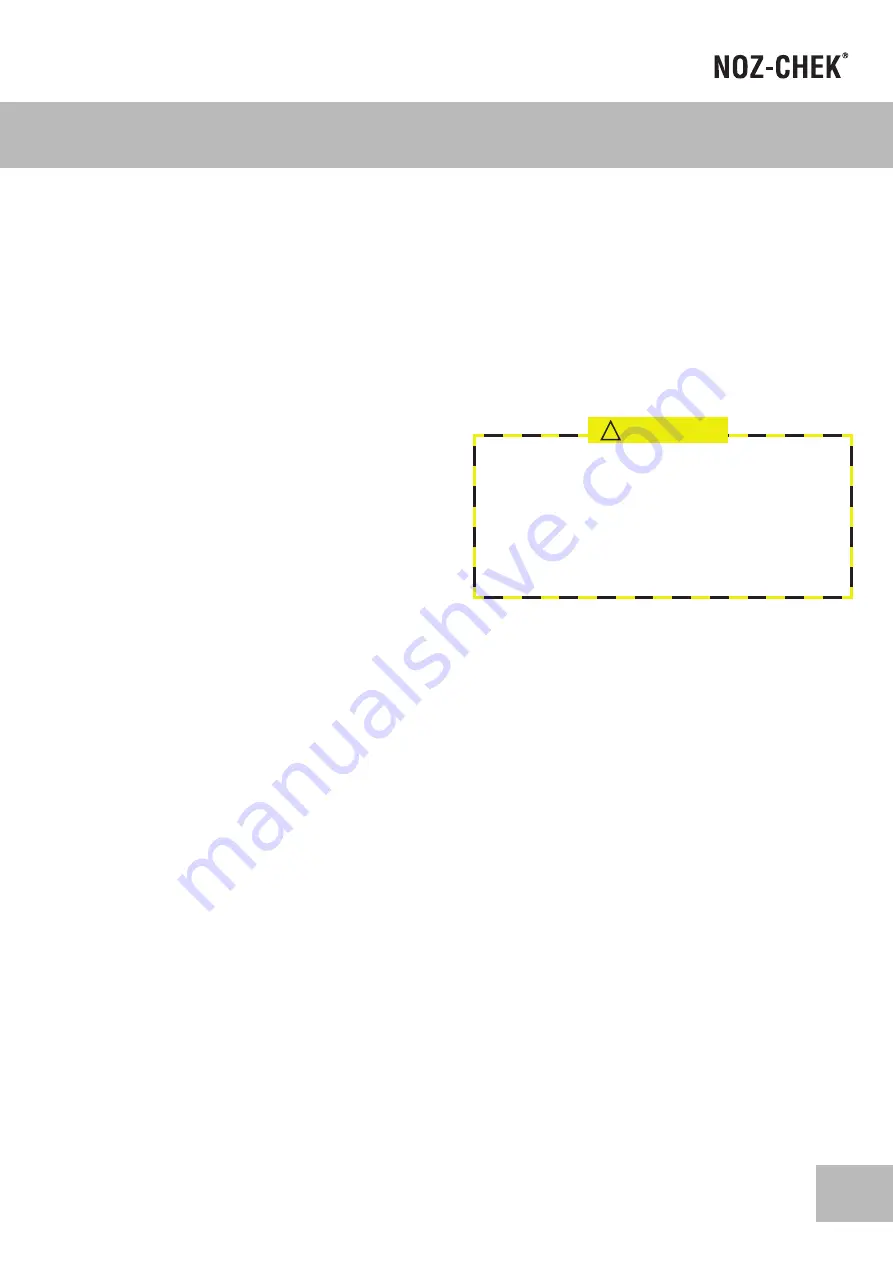
5
www.cranecpe.com
NOZ-CHEK
®Cryogenic
Installation, Operation & Maintenance
NOZ-CHEK
®Cryogenic
Installation, Operation & Maintenance
5.0 MAINTENANCE
5.1 GENERAL
Depending on the severity of the application (e.g. flow
velocity, cycling, location of valve) maintenance can be
scheduled accordingly. A suggested duration is in the
range of 5-10 years under average conditions.
This product was built and tested to exacting standards.
The following maintenance procedure must be followed
with a great deal of care.
If a detailed inspection is required, we can provide a kit of
spares and special tools:
Standard Design:
Spares: Spring Energized Seal–(10)–(See figure 1)
Alternative Seal Design:
Spares: Metal C-seal
Special Tools: Seat Extractor (See Figure 2)
Disc Extractor (See Figure 2)
Plus tools normally carried by standard maintenance
team.
5.2 POSITION SWITCHES (IF APPLICABLE)
The sensing surfaces of the magnet housing and switch
housing should be checked for deposits that could effect
the operation of the switch and cleaned if necessary.
Also, the magnet housing and switch housing should be
checked to ensure that they have not become loose, and
the cable checked for wear or damage and replaced if
necessary.
The switch (21) may be checked or replaced without
removing the switch housing (20) from the valve (1). This
will eliminate the need for draining the valve prior to
disassembly. Simply unscrew the cable gland (22), whilst
preventing the switch housing (20) from moving. The
switch spacer (27) and switch (21) may then be removed
for inspection. See Figure 3A.
5.3 VALVE DIS-ASSEMBLY (TYPICAL) – SEE FIGURE 1
Ensure that area upstream of seat (2) is clean and free
from scale.
Valve should be resting on downstream side (ensuring no
damage to sealing face)
Valve may need to be secured to avoid rotation when dis-
assembling.
a)Remove seat screw (13) and insert the Seat Extractor
tool into the slots in the seat to unscrew the Seat (2)
counter clockwise (See Figure 2).
b) Remove set screw (12) and screw the Disc Extractor tool
into the tapped hole in the top of the disc (3) to withdraw
it (see Figure 2).
c) Remove compression springs (8). Then using a suitable
hex head socket, remove the guide housing (4) by turning
counter clockwise.
d) Remove retaining rings (6) and extract guide bushes (5)
HEALTH & SAFETY
Caution should be exercised when removing disc as
compression of springs could cause ejection of the disc (a
weight should be placed upon the disc to avoid injury).
Ensure the appropriate Personal Protective Equipment is
used such as safety glasses, gloves and safety shoes.
Ensure surrounding lighting is adequate.
5.4 REPAIRS
Minor repairs can be performed on Seat, Seal and Bushes
– lightly emery to remove any bruising. Remove all
deposits and debris.
Major repairs such as Seal replacement, Seat Machining
etc. would require special equipment. Contact your Crane
Stockham Valve representative for further advice.
Spare discs for metal seated valves should be lapped into
the mating seat in order to achieve low leakage rates.
Disc Seal Replacement – Disc seals employ a specialist
process of applied heat and pressure for bonding rubber
to metal and can only be replaced by Crane Stockham
Valve.
CAUTION
!