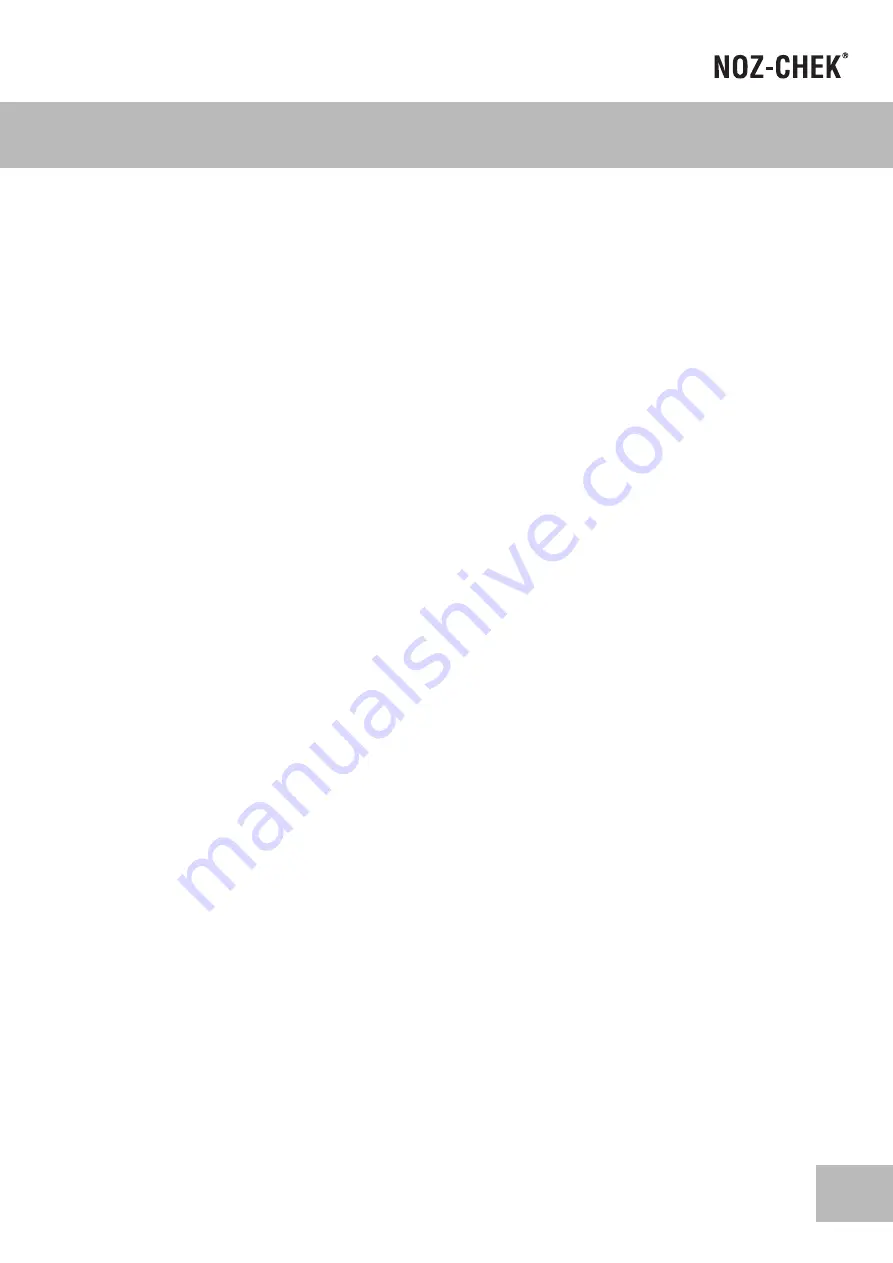
3
www.cranecpe.com
NOZ-CHEK
®Cryogenic
Installation, Operation & Maintenance
NOZ-CHEK
®Cryogenic
Installation, Operation & Maintenance
2.0 INITIAL COMMISSIONING
A Crane Stockham Valve Noz-Chek® check valve is a
precision built product, specifically designed for the
operating parameters of your system.
Please observe the following recommendations:
2.1 INITIAL / COMMISSIONING PROCEDURE
(a) Valves will be packed in accordance with our ESB 2155
APP20, Packing, preservation and site storage procedure
for cryo valve products.
(b) Care should be taken not to damage any paint work,
while lifting and moving valves.
(c) Care should be taken not to damage flange / mating
faces of valves.
(d) Care should be taken to avoid mechanical damage
to cable / junction box of the Position Switch during
installation of valve and throughout its working life, (if
applicable).
(e) Care should be taken to prevent contanmination of
the valve from dirt,dust or any other foreign bodies from
entering the valve internals.
(f) Remove any desiccants that have been placed in bore
of valve prior to installation.
2.2 STORAGE
The valve shall be stored within a sealed polyethylene bag
to prevent any contaminants from entering the valve.
3.0 INSTALLATION
(a) Direction of Flow
The direction of flow should coincide with the flow
direction indicated by the cast ‘arrow’ on the body of the
Noz-Chek®.
(b) Operating Orientation
Ensure that the mounting position is in the operating
orientation as advised on the Service specification for
each valve when ordered i.e. horizontal, vertical upwards
or downwards flow.
(c) Line positioning
Ideally the check valve should have 5 diameters of
straight pipe before and 6 diameters after the valve. For
practical reasons this is often not possible. The valve
should have as a minimum, 2 diameters of straight
pipe before and after its location. The valve will under
normal circumstances still function as a non-slam check
valve if fitted closer to other equipment than the stated
guidelines; however this will normally result in increased
pressure loss and wear of components. This phenomenon
is not exclusive to Crane equipment, and should be
applied to any pipe layout as good practice.
The pressure loss of any piece of piping equipment
in a system will be affected by the presence of other
equipment. Pressure loss is an unrecoverable energy loss
and is the measured decrease in pressure. Measuring
the pressure drop immediately before and after piping
equipment will give a higher reading than measuring a
sufficient distance before and after the piping equipment.
This is due to pressure recovery after the equipment as
the flow returns to the full flow area of the pipe. Standard
flow loop testing requires two diameters of straight pipe
before the equipment and six after. Most of the pressure
recovery will occur in the first three diameters after a
nozzle check valve and a significant amount after two
diameters.
Two diameters before the piping equipment will allow
for the pressure recovery of the upstream equipment.
The flow will also lose the increase in turbulence caused
by the disruption of the flow by the equipment. Placing
equipment too close together will amplify any disruption
to the flow and make the overall pressure loss to the
system more than the sum of the individual pressure loss
of the equipment.
Insufficient straight pipe before the piping equipment
can also cause a significant increase in the wear of the
components and reduce the life of the equipment.
Research has shown that typically five diameters are
required to stop the effects of accelerated wear with
the affects increasing in an exponential curve. With the
geometry of the nozzle check valve it has been shown
that two diameters is sufficient to make the affects of the
accelerated wear minimal.
(d) Lifting and Flange Assembly
Always lift the valve by the lifting eyes provided, or
alternatively a well padded sling.
Ensure that no external pipeline stresses are imposed on
the valve prior to tightening bolts and pipework mating
flanges are parallel.
Ensure bolts are tightened correctly. Always tighten in
a diagonally opposing bolt sequence, to ensure that all
bolts apply a uniform load, with the gaskets properly
installed.