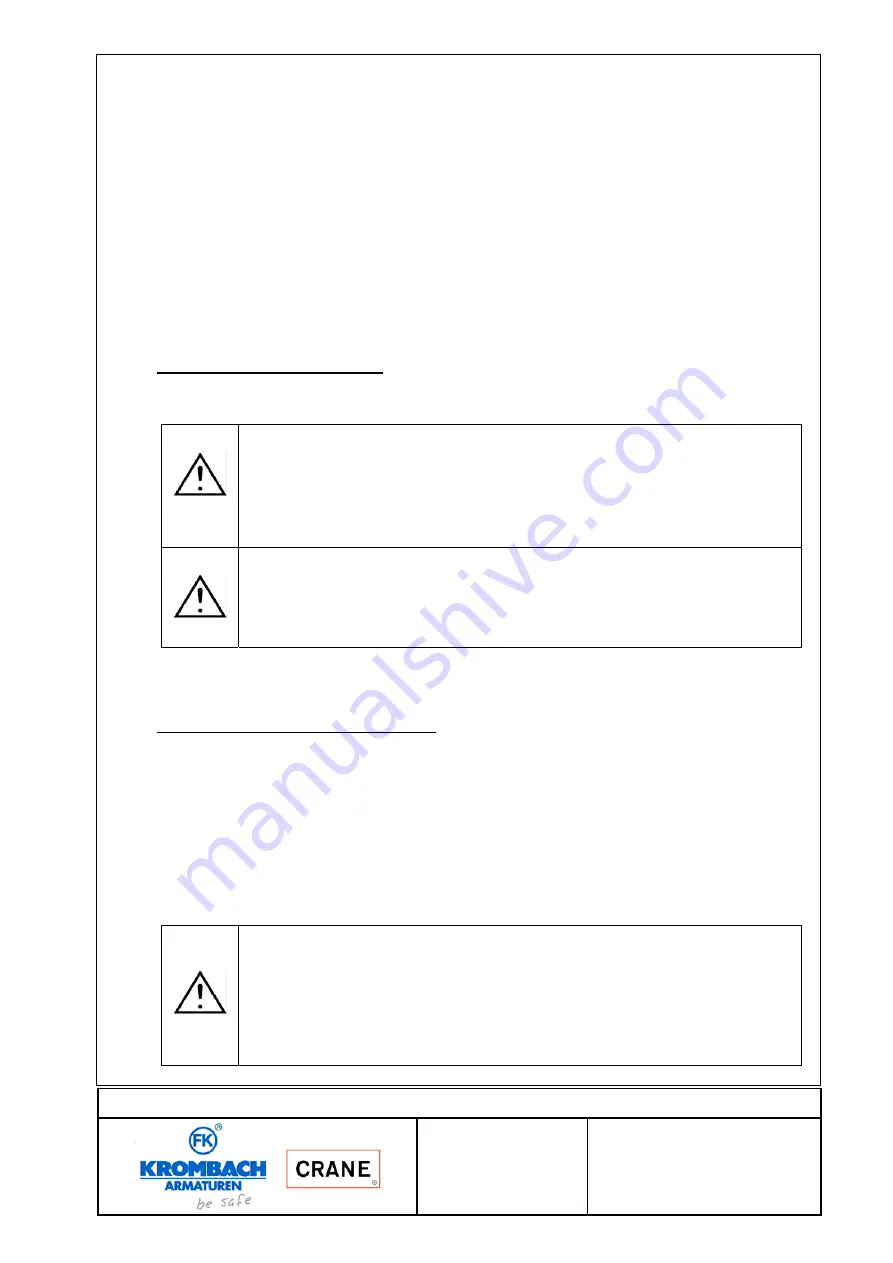
Tilting Disc Type Check Valves
Date:
prepared:
approved:
Page:
22.03.2005
C.Wied
H.Six
6 of 14
Operating instruction No.:
BUW-510/1-E
6.3. Installation
position
and direction of flow
⇒
The check valve has to be mounted so that the arrow on the valve body coincides with the
expected flow direction through the pipe.
⇒
The check valve has to be mounted with horizontal located shaft.
6.4.
Steps for installation
⇒
When inserting the armature (and the flange sealing) into a previously installed pipeline, the
distance between the ends of the pipeline must be measured such that all connection surfaces
(and sealings) remain undamaged.
However, the gap must not be larger than necessary, in order not to generate any additional
stresses in the pipeline.
Only check valves with flanges:
⇒
The counterflange of the pipeline must be straight and coplanar.
Important
Check Valves with flange ends:
The sealing surfaces on housings with flange ends of the check valve are formed
such that the flange sealings can be used in accordance with EN1514-1 or ANSI
B16.21. The counterflange must have smooth sealing strips, e.g. Form C or D or E
in accordance with the standard EN 1092 or Stock Finish in accordance with ANSI
B16.5. Other flange forms must be agreed with KROMBACH.
Important
Check valves must be inserted into the gap between the pipeline ends with the
valve disc closed, otherwise the valve disc could become damaged and the
armature no longer sealed.
⇒
Flange check valves must be centred when installing by means of the flange screws on the
counterflange before the screws are tightened.
Only check valves with butt weld ends:
⇒
The butt weld ends of the armature must be straight and coplanar and must be of the same kind
as the pipe materials - see Material specification in the type plate of the armature.
Opposite butt weld ends must match each other in diameter and joint form.
⇒
Welded cables may not be attached to the armature: they must be attached to the pipeline.
⇒
It must be ensure through correct welding that no significant stresses are created in the pipeline
section or are transferred to the armature, and that the butterfly valve does not become damaged
by the effects of heat. Only temperatures of <300°C measured at the housing wall are
permissible.
⇒
Check valves >DN300:
Important
When welding the valve into the pipeline, the welding procedure must be controlled
in such a way that the heat energy applied is limited and that the valve housing
does not become distorted. For example, the welding should be carried out
“crosswise” in order to avoid tension on the armature housing.
Failure to observe these requirements can cause distortion of the valve housing.
Distortion remaining in the seat area (the whole area near the position supports)
can make the armature unusable.