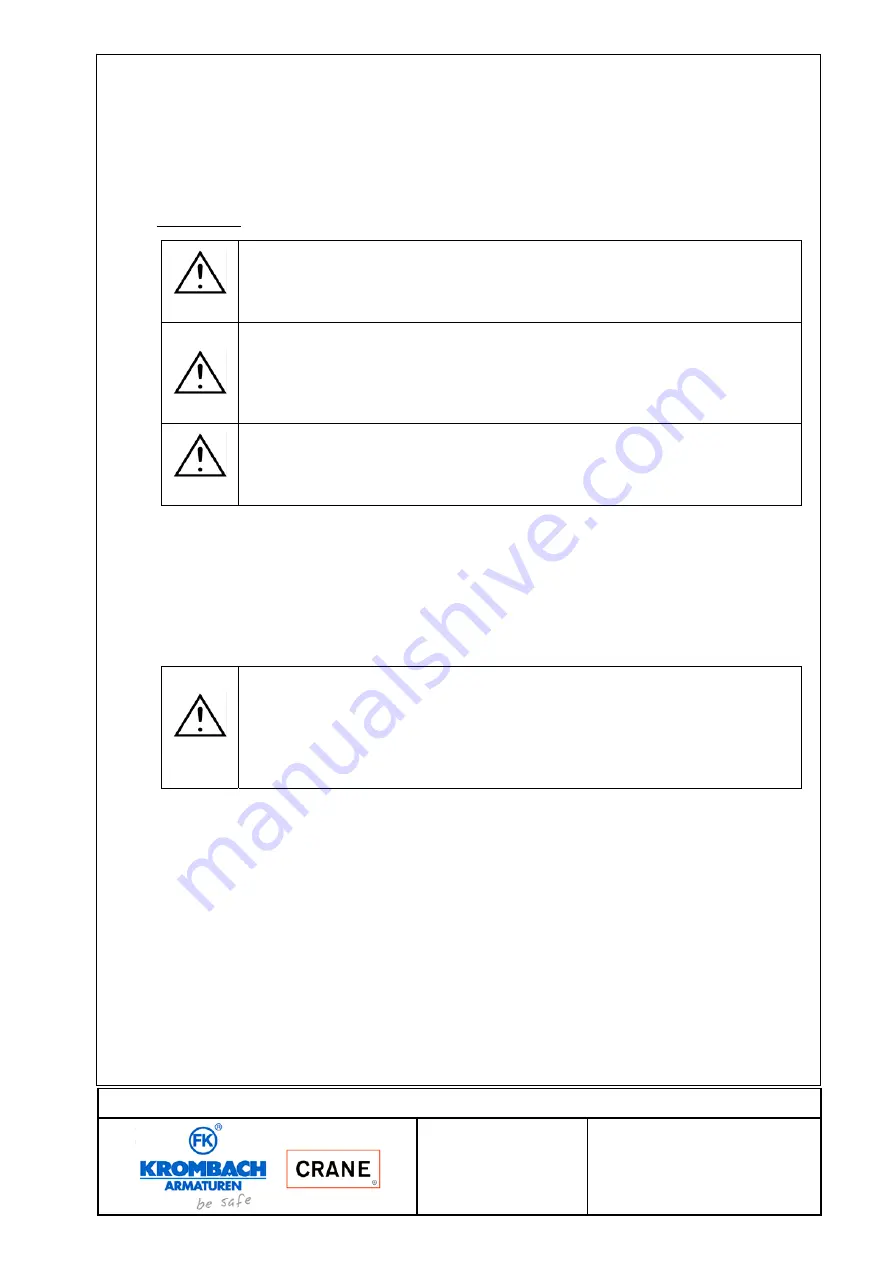
Tilting Disc Type Check Valves
Date:
prepared:
approved:
Page:
22.03.2005
C.Wied
H.Six
5 of 14
Operating instruction No.:
BUW-510/1-E
6. Installation into the pipeline
6.1. General
The same instructions apply for the installation of armatures into a pipeline as for the connections
of pipes and similar elements of the pipeline. For armatures, the following instructions apply
additionally
. Section 5 must also be observed for transportation to the installation site.
Important
Butterfly valves must be
transported and installed with the valve disc closed
.
Otherwise the disc could become damaged and the valve no longer sealed.
Important
There is a danger of crushing from check valves that have not been installed:
the drive (if ordered) must not be connected and activated
until the butterfly
valve has been installed into the pipeline
.
Note
The check valve is configured from works for the sealed closed position:
This setting of the end stops "CLOSED"
in the valve body may not be changed.
6.2.
Preparation for installation
⇒
Ensure that no armatures are installed whose pressure class, type of connections and connector
dimensions do not correspond to the service conditions. See type plate on the armature. The
connection data for the drive must agree with the data of the control system. See type plate on
the drive.
Danger
to life
Armatures whose pressure / temperature range (= “Rating”) is not sufficient for the
operating conditions must not be operated: the permitted value can be read from
the type plate of the armature. It is mandatory to obtain approval from KROMBACH
where the armature is to be used outside these ranges.
Failure to observe this requirement can lead to danger to life and limb and
cause damage in the pipeline system.
⇒
Examine valve and oil brake for transport damage. Do not install damaged valves, oil brakes or
other mounting parts.
⇒
There has to be sufficient space in the pipe before and behind the valve for the disc in open
position (for example no shut-off valve mounted before and behind the check valve) so that the
disc is not damaged during the opening and opens completely.
⇒
Before installation, the armature and the subsequent pipeline must be carefully cleaned of soiling,
particularly of hard foreign bodies.
⇒
It is recommended that the pipeline is flushed before installing the armature.
⇒
Connection ends of the armature and inner sealing surfaces are lubricated with a thin film of
grease. Before installation, carefully remove the grease conservation with a suitable solvent and
clean the interior of the armature with compressed air.