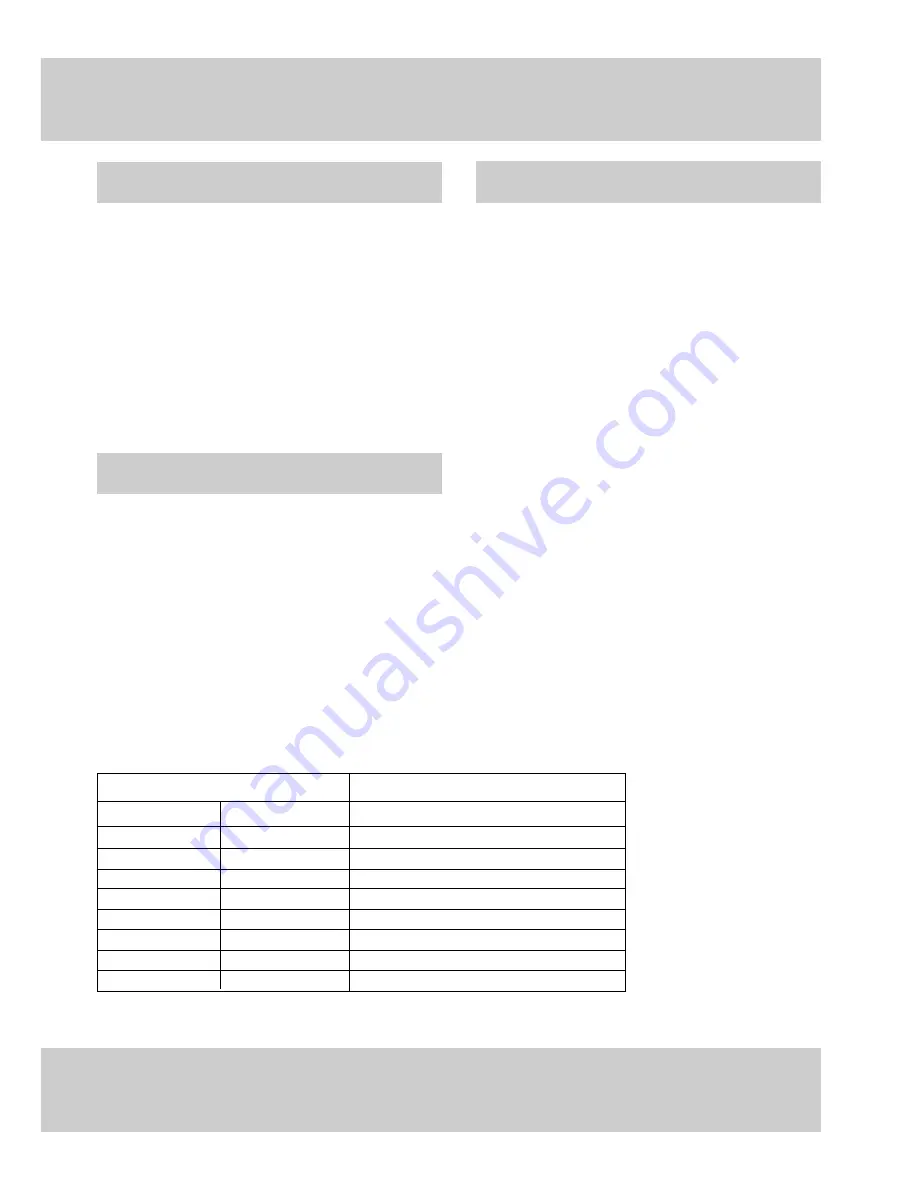
SETTING FACILITY
The valve setting at which the required flow rate
may be achieved may be retained by loosening
the memory stop screws and sliding the
memory stop up until it contacts the grey plastic
sleeve protruding from the hand wheel.
Retighten the screws.
The valve is now set and may be closed and
reopened to the set point. A Hex. wrench is
provided for this adjustment. Sizes up to DN
150 require a 3mm wrench, and larger sizes a
4mm wrench.
VALVE ISOLATION
Tight valve shut off at high working pressures
will require closing torques which are higher
than can be obtained manually with the hand
wheel, and will require the use of a closing bar
or wrench. Valve sizes of DN200 and larger
have a square cast in to the top of the hand
wheel for this purpose. A guide to the torques
required for a 16 bar pressure drop across
the valve are shown in the table. These torques
may be applied without risk of damaging
the valve.
MAINTENANCE
No routine maintenance is required, however it
is possible to tighten the gland packing should
a leak occur between stem and gland nut:
Unscrew the hand wheel nut and remove the
hand wheel. Mark the hand wheel so that it may
be replaced later in the same position relative
to the stem.
The gland nut is now revealed and may be
tightened as required . For sizes DN65 (2.1/2”)
to DN100 (4”) use a 27mm socket. For sizes
DN125 (5”) and DN150 (6”) use a 32mm
socket. Larger sizes have two M8 studs and
nuts (13mm spanner).
Only tighten the nut sufficiently to cure the leak.
Over tightening may make the valve difficult or
impossible to operate. (The balancing valves
are not provided with back seats. Under no
circumstances should the gland nut be removed
without first isolating the valve and relieving any
residual pressure.)
Replace the hand wheel and check that the
valve may be operated without requiring
excessive torque at the hand wheel.
VALVE SIZE
MAXIMUM CLOSING TORQUE
DN
NPS
NM
65
2.1/2
45
80
3
60
100
4
110
125
5
130
150
6
220
200
8
420
250
10
650
300
12
650