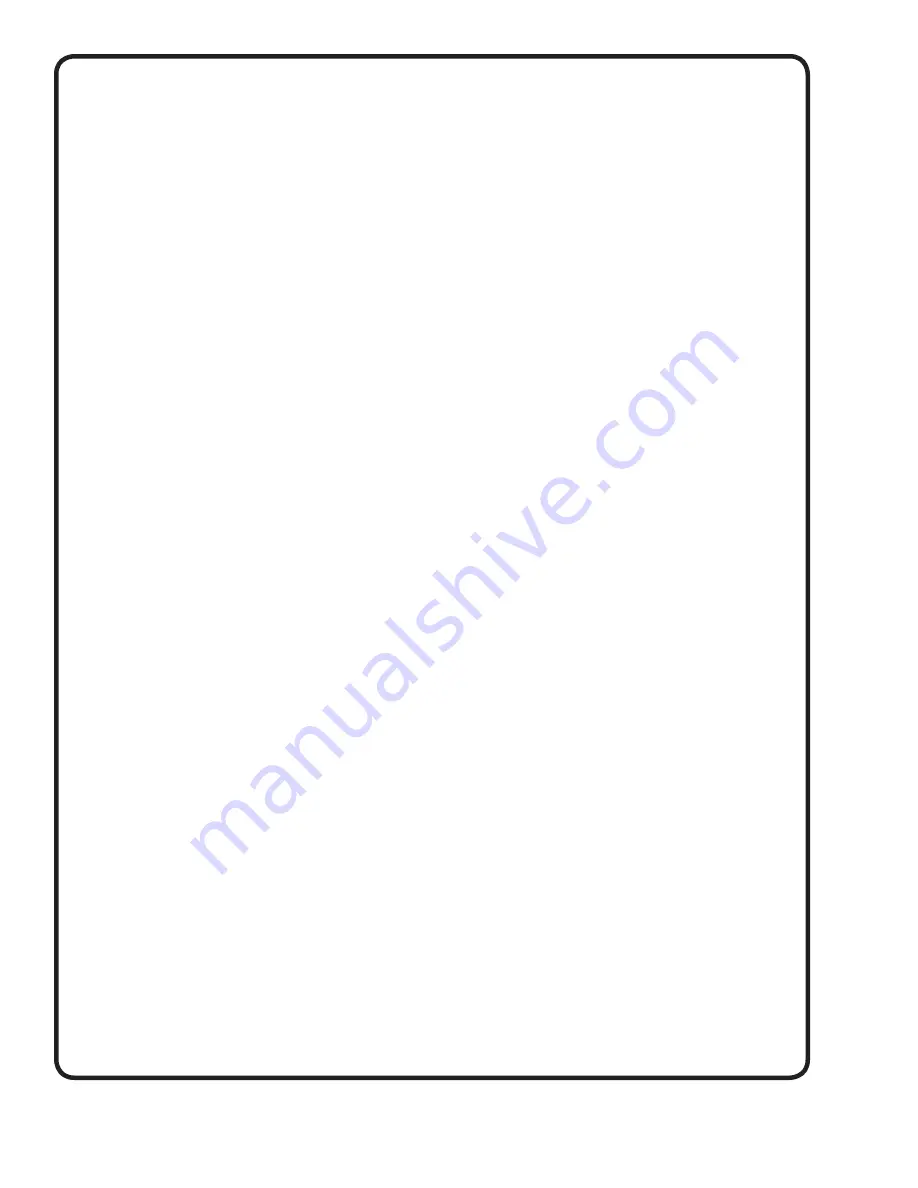
6
G - ASSEMBLY OF LIQUID END
1. Slide
de
fl
ector (040) over shaft, but do not adjust.
2. Place throttle housing (099) over end of the shaft
and
against
fl
ange of frame (019). Align bolt holes
with those of frame.
3. Position casing (001) against
fl
ange with discharge
in proper position and tighten nuts securely.
4. Replace impeller key (032) in the shaft and properly
position the impeller (002) on the shaft. Place
impeller washer (270) on shaft, then the impeller
nut (024). Tighten securely. Replace cotter pin in
shaft to prevent impeller nut from coming off.
DO
NOT USE NUT TO DRAW IMPELLER ONTO
SHAFT.
The nut is a locking device only.
5. Place gasket (073) on suction head (009) and
position suction head on casing (001). Tighten cap
screws (215) on suction head.
6. Reassemble the discharge pipe and tighten pipe
nuts being careful not put a strain on casing
discharge
fl
ange.
7. Adjust
de
fl
ector (04) so that the lower side of
de
fl
ector is about 1/8” above bearing housing (099).
With unit in vertical position and liquid end
completely
assembled.
H - IMPELLER ADJUSTMENT &
FINAL
ASSEMBLY
1. Lower unit into position in tank or sump and bolt
base plate down. Replace lower half coupling and
shaft
key.
2. Mate cam of bearing (018) with cam of bearing inner
ring. Pressing collar lightly against inner ring, turn
collar in direction of shaft rotation until engaged.
3. Tighten bearing lock nut (066) hand tight and until
shaft just turns freely by hand. Turn nut 1/2 additional
turn and bend tang of lock washer into slot of nut.
4. with drift pin in collar hole, strike in direction of shaft
rotation to lock tighten set screw in bearing collar.
5. Turn shaft again by hand and make certain shaft and
impeller turn freely. If shaft binds or impeller rubs
check for pipe strain and if required, raise impeller
an additional 1/4 turn. The correct clearance
between impeller and suction face is .020 - .030
normally 1/2 turn of nut.
6. Replace bearing cover, motor and coupling. Align
coupling and proceed with installation as described
in that section
I - LOCATING TROUBLE
1. No water delivered
a. Wrong direction of rotation
b. Impeller or pipes plugged
c. Discharge head too high
d. No water in pit
e. Pump suction to close to bottom of pit
2. Not enough water delivered
a. Discharge head higher than expected
b. Impeller or pipes partly plugged
c. Improper impeller adjustment
d. Low water level in pit
e.
Mechanical
defects
1. Impeller worn or damaged
2. Casing worn
f. Wrong direction of rotation
3. Not enough pressure
a. Air in water
b.
Mechanical
defects
c. Impeller diameter too small
d. Wrong direction of rotation
e. Impeller not properly adjusted
f. Discharge head (line friction) lower than expected
4. Pump takes too much power
a. Speed too high for required head and capacity
b. Head lower than rating; pumps to much water
c. Liquid either viscous or heaver than water or both
d.
Mechanical
defects
1. Shaft bent
2. Impeller binds in casing
e. Strain on pump caused by piping misalignment
f. Impeller not adjusted properly
Summary of Contents for DEMING 5411 Series
Page 7: ...7 ...