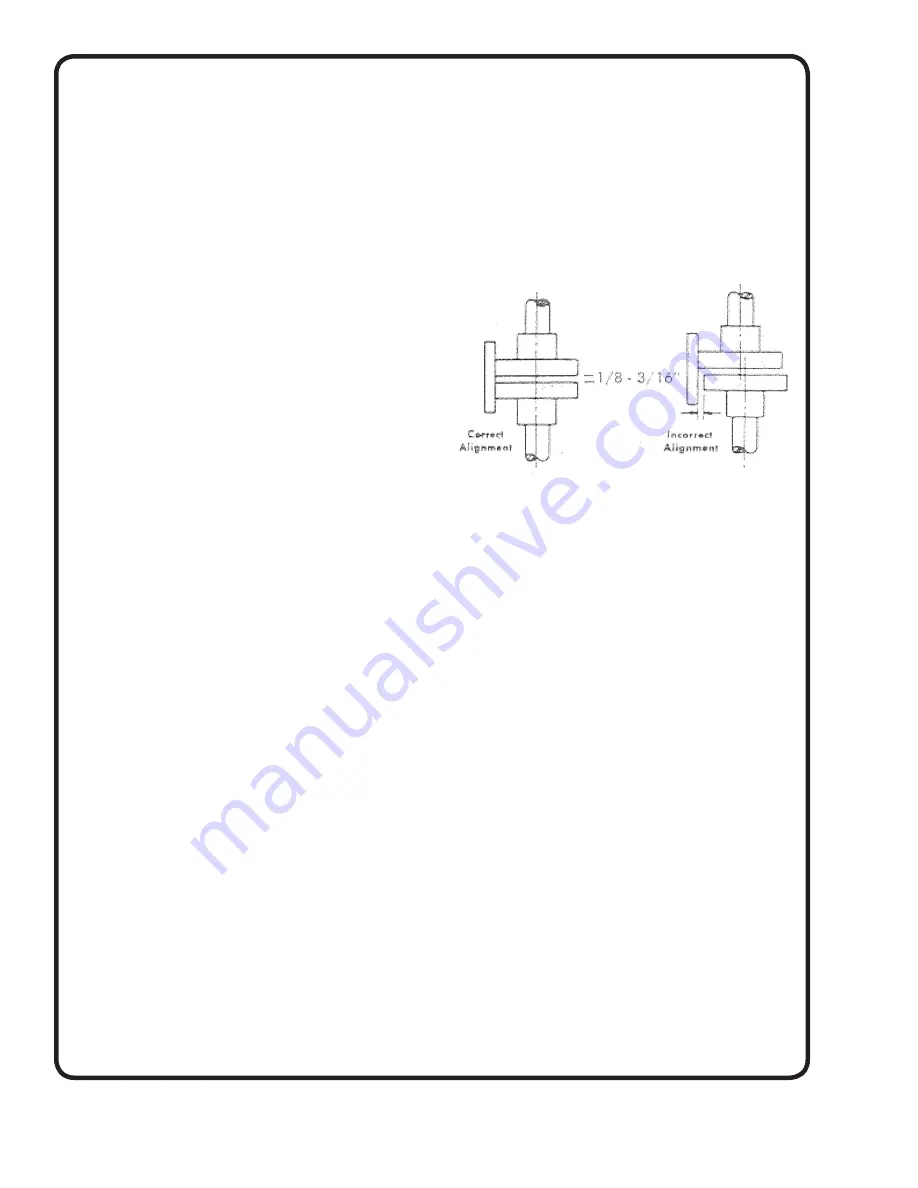
4
A - GENERAL INFORMATION
TO THE PURCHASER:
Congratulations! You are the owner of one of the
fi
nest
pumps on the market today. These pumps are products
engineered and manufactured of high quality components.
With years of pump building experience along with a
continuing quality assurance program combine to produce
a pump which will stand up to the toughest applications.
Check local codes and requirements before installation.
Servicing should be performed by knowledgeable pump
service contractors or authorized service stations.
RECEIVING:
Upon receiving the pump, it should be inspected for
damage or shortages. If damage has occurred,
fi
le a claim
immediately with the company that delivered the pump.
If the manual is removed from the crating, do not lose or
misplace.
STORAGE:
Short Term -
Pumps are manufactured for ef
fi
cient
performance following long inoperative periods in storage.
For best results, pumps can be retained in storage, as
factory assembled, in a dry atmosphere with constant
temperatures for up to six (6) months.
Long Term -
Any length of time exceeding six (6) months,
but not more than twenty four (24) months. The units
should be stored in a temperature controlled area, a roofed
over walled enclosure that provides protection from the
elements (rain, snow, wind blown dust, etc..), and whose
temperature can be maintained b40 deg. F and
+120 deg. F. Pump should be stored in its original shipping
container and before initial start up, rotate impeller by hand
to assure seal and impeller rotate freely.
SERVICE CENTERS:
For the location of the nearest Deming Service Center,
check your Deming representative or Crane Pumps &
Systems Service Department in Piqua, Ohio, telephone
(937) 778-8947 or Crane Pumps & Systems Canada, Inc.,
Bramton, Ontario, (905) 457-6223.
B - INSTALLATION
Standard pumps are completely assembled, carefully
adjusted and lubricated at the factory before shipment.
1. Carefully lower the pump into position. The base plate
(023) must be level and rest evenly at all points where
it will be bolted. If necessary, use metal shims as
required to level plate.
IMPORTANT ! - The alignment between the motor
and pump must be carefully checked before pump is
started.
In spite of careful assembly at the factory, alignment
may change during shipment due to handling. Hold
a straight edge on the coupling so that it extends
over both halves. The straight edge should rest evenly
across both rims of the coupling halves. Any
misalignment may be corrected by adjusting the set
screws in the lugs under the chair bracket, or possibly
metal shims under the motor feet. Chair bracket
mounted units should be checked for alignment every
other day during the
fi
rst week of operation, then once
a week until alignment remains constant.
2. The weight of the suction and discharge pipes and
fi
ttings must be supported independently of the pump
to eliminate any strain on the pump support plate or
pipe. A check valve and gate valve should be installed
in the discharge line close to the pump.
3. Rotate shaft by hand checking for impeller rubbing on
high spots. If either is noted check for (A) pipe strain,
(B) caps misalignment, (C) improper impeller
adjustment.
4. Connect discharge line to pump discharge pipe and
close gate valve. Connect power line to motor in
accordance with wiring diagram on the motor. Jog
motor control to test for rotation, standard pumps
rotate clockwise looking down on the motor. (Left hand
pumps operate in reverse direction.)
5. The pump should operate smoothly. If the pump
vibrates, there is severe distortion of the pump as a
result of excessive installation strain of the support
plate, pipe strain or misalignment between motor and
pump, improper impeller adjustment or a combination
of
these.
C - LUBRICATION
1. Pump bearings are properly lubricated at the factory
before shipment. Periods of subsequent lubrication
depend on local conditions, hours of operation, load,
speed, temperature, etc. It is recommended that
bearings (016) and (018) be periodically inspected and
lubricated.
Summary of Contents for DEMING 5411 Series
Page 7: ...7 ...