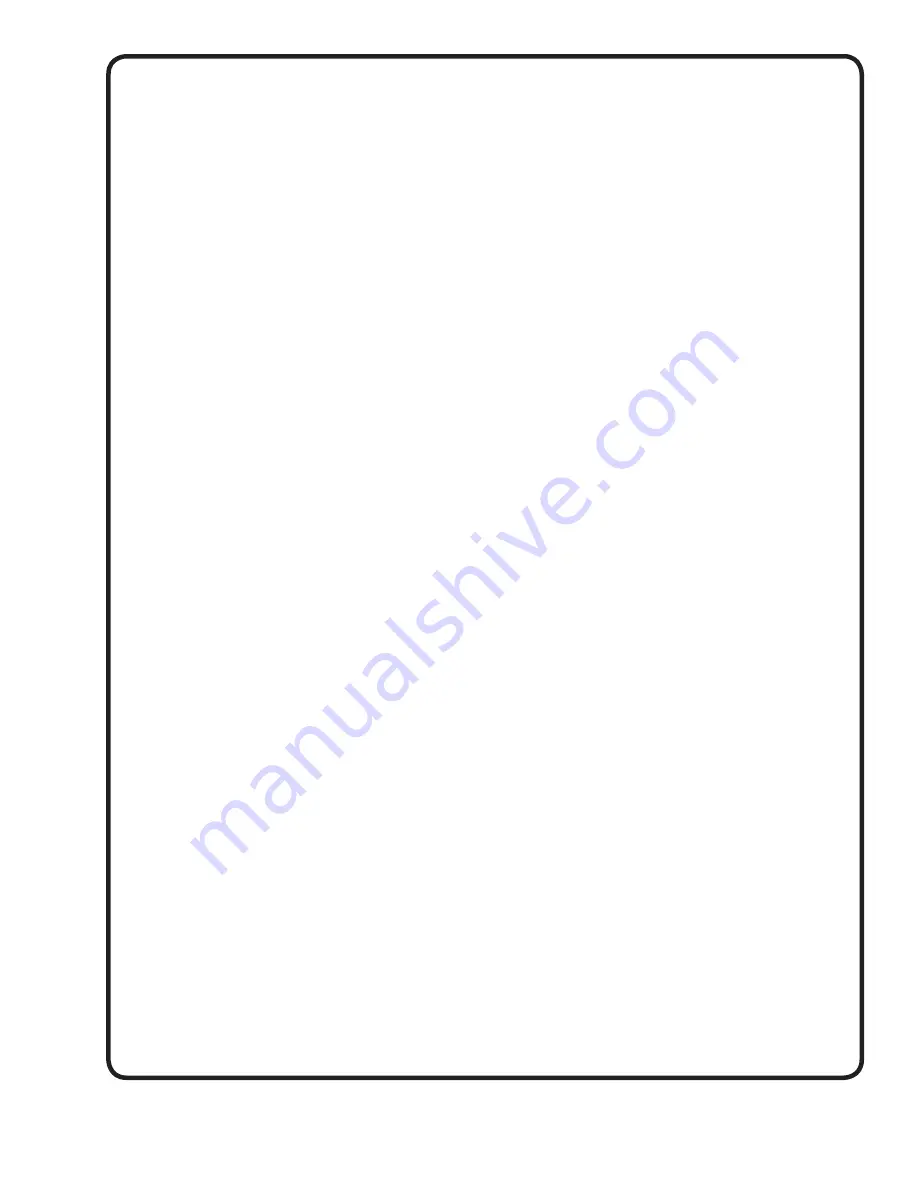
3
A - GENERAL INFORMATION
TO THE PURCHASER:
Congratulations! You are the owner of one of the
fi
nest
pumps on the market today. These pumps are products
engineered and manufactured of high quality components.
With years of pump building experience along with a
continuing quality assurance program combine to produce
a pump which will stand up to the toughest applications.
Check local codes and requirements before installation.
Servicing should be performed by knowledgeable pump
service contractors or authorized service stations.
RECEIVING:
Upon receiving the pump, it should be inspected for
damage or shortages. If damage has occurred,
fi
le a claim
immediately with the company that delivered the pump.
If the manual is removed from the crating, do not lose or
misplace.
STORAGE:
Short Term -
Pumps are manufactured for ef
fi
cient
performance following long inoperative periods in storage.
For best results, pumps can be retained in storage, as
factory assembled, in a dry atmosphere with constant
temperatures for up to six (6) months.
Long Term -
Any length of time exceeding six (6) months,
but not more than twenty four (24) months. The units
should be stored in a temperature controlled area, a roofed
over walled enclosure that provides protection from the
elements (rain, snow, wind blown dust, etc..), and whose
temperature can be maintained b40 deg. F and
+120 deg. F. Pump should be stored in its original shipping
container and before initial start up, rotate impeller by hand
to assure seal and impeller rotate freely.
SERVICE CENTERS:
For the location of the nearest Deming Service Center,
check your Deming representative or Crane Pumps &
Systems Service Department in Piqua, Ohio, telephone
(937) 778-8947 or Crane Pumps & Systems Canada, Inc.,
Bramton, Ontario, (905) 457-6223.
B - INSTALLATION
1. ROTATION
Check motor rotation before making permanent
connections to power supply. Motor should rotate
clockwise when looking down on motor.
2. LUBRICATION
See that motor bearings are supplied with lubricant. For
longest life and most carefree operation, it is suggested
that
fi
ve to ten drops of a good grade of mineral oil be
added to each bearing once a year. We recommend that
the thrust bearing (18) be periodically greased with a
quality grade of light grease.
3. IMPELLER ADJUSTMENT
The Impeller is properly adjusted when the pump leaves
the factory. If it is desired at some later date to readjust
the impeller clearance to compensate for wear this may be
done by lowering the impeller. To do so, loosen setscrew
(342) and adjusting nut (66). Loosen bearing collar. When
the impeller is seated down on the suction head strainer,
tighten the bearing collar. Tighten adjusting nut so that the
nearest tapped hole in nut is aligned with the keyslot in
the shaft. Tighten setscrew (342) into this hole. Shaft and
impeller should turn freely. If not, tighten adjusting nut to
next nearest hole.
C - DISMANTLING
1. Disconnect discharge line and motor wiring. Pull
pump.
Remove
fl
aot and switch
2. Disconnect discharge pipe from casing (1). Remove
base (53), and suction head strainer (316) from casing
(1).
3. Unscrew impeller nut (24) and pull impeller (2) from
pump shaft (6). Remove Woodruff key (32).
4. By removing motor cap screws, the top half of coupling
(42) and the motor (228) can be removed as a unit.
Remove coupling spider (42). Remove thrust bearing
snap ring (18).
5. Pump shaft (6), adjusting nut (66), thrust bearing (18)
and lower half of coupling (42) can now be removed as
a unit from the motor support (19), column pipe (101),
and casing (1). Inspect lower bearing bushing (39). If
worn, it should be replaced.
6. To replace thrust bearing (18),
fi
rst mark the shaft
where the bearing is to be located. THen remove the
lower half of coupling (42) and the shaft key (46).
Remove adjusting nut (66). Loosen bearing collar
setscrew and turn collar in opposite direction of shaft
rotation. Pull the bearing from the shaft. Follow the
reverse procedure to reassemble.
7. Do not disconnect motor support (19) or casing (1)
from column pipe (101) unless necessary. If
necessary, they can be removed by loosening
setscrews (520) and (507). Remove split cover plate
(23) (Type A only).
8. If grease seal (169) needs replace, remove it from
motor support and press in new one.
Summary of Contents for DEMING 4507 Series
Page 10: ...Notes ...