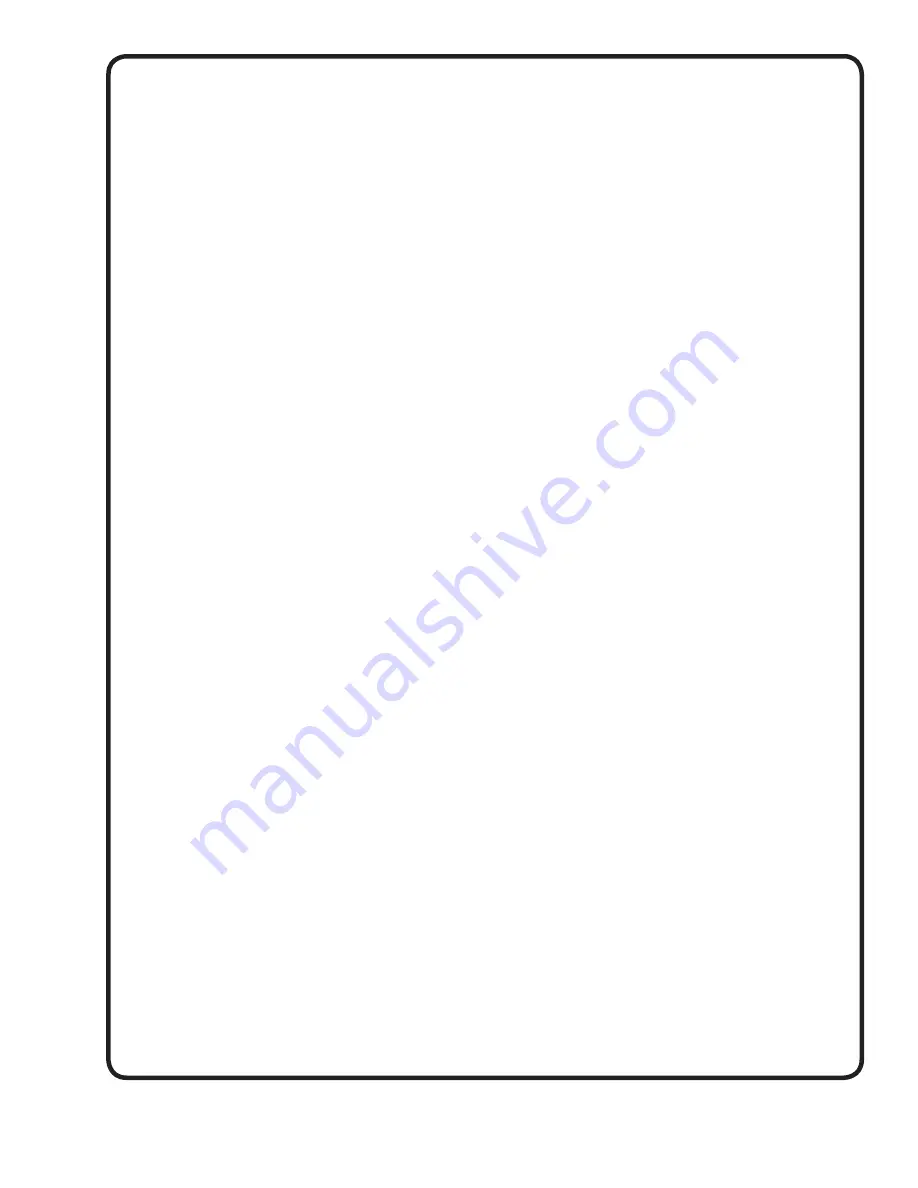
5
GENERAL MAINTENANCE AND REPAIR
E - PROPER ADJUSTMENT OF IMPELLER
To adjust the impeller, unscrew the two set screws in
bearing collar (123). Push shaft forward until impeller
vanes touch the casing wear faces, then back off the shaft
slightly. Secure set screw on bearing collar. Rotate the
shaft by hand to make certain the impeller does not rub on
the casing wear face.
F - TO REMOVE OR REPLACE IMPELLER
Remove casing cap screws (212) and casing (1), also take
off casing gasket (73) which must be kept moist while out
of the pump. Remove impeller nut (24) and thread impeller
(6) from shaft in counter-clockwise direction. To install new
impeller, thread impeller (2) completely onto shaft and lock
in position with nut (24). Replace casing and gasket.
DO NOT
attempt to make impeller adjustment by threading
impeller only partially onto shaft. Thread completely on. If
impeller adjustment is necessary, follow procedure outlined
in Section “E”.
G - DISMANTLING
1. Drain pump, disconnect suction and discharge piping.
2. Remove casing cap screws (212) and casing (1). Also
take off casing gasket (73) which must be kept moist
while out of pump.
3. Unscrew impeller nut (24). Unscrew impeller (2) by
turning
counter-clockwise.
4. Remove mechanical seal (89) from shaft (6).
5. To remove shaft (6), remove machine screws (213), lock
washers (229) and bearing cover (123). Brace support
head and tap lightly with babbit or plastic hammer on
impeller end of shaft. Shaft (6) and bearings (16) and
(18) should be removed as a unit.
6. If it is necessary to replace the ball bearings (16) and
(18) mark the positions of the ball bearings on the shaft.
Unscrew the set screw from bearing collars, then push
the collars and bearings from the shaft.
7. To replace ball bearings, remove from bearing collars.
8. Extreme care should be taken in keeping parts clean.
Special precaution should be taken to keep ball
bearing dirt-free in or out of the pump. Any parts which
are excessively worn or deteriorated should be replaced
with new parts from the factory.
IF IT IS MORE CONVENIENT TO DISMANTLE THE
PUMP WITHOUT DISCONNECTING THE SUCTION AND
DISCHARGE LINE, IT IS POSSIBLE TO DO SO, AS
FOLLOWS:
1.
Drain
Pump
2. Remove cap screws (212) from casing (1).
3. Pull the frame (19) carefully away from the
casing (1). Remove casing gasket (73) which must be
kept moist while out of pump.
4. Proceed with number 3 under Dismantling.
H - REASSEMBLING
1. If the ball bearings have been removed from the shaft,
replace them on shaft (6) in the same position marked
on the shaft before dismantling. Replace set screws in
bearing collars and secure to the shaft.
2. Replace shaft (6) with ball bearings (16) and (18) as
a unit through coupling end of frame (19) and slip
the rubber slinger over the shaft before it enters the seal
chamber. Replace bearing cover (123), lock washer
(229), machine screws (213) and secure to support
head.
3. Install seal as explained under “Mechanical Seals”.
4. Install impeller (2) and locknut (24) as explained under
“To Remove and Replace Impeller”.
5. Replace casing gasket (73), casing (1) and secure to
support head with cap screws (212).
On Figure 3914 “A” size pumps only, studs are used to
secure casing (1) to frame (19). If these studs (216) are
removed from casing (1), apply sealant or thread compound
to threads before reinstalling in casing to prevent leakage
around stud threads.
I - MECHANICAL SEAL
.
NOTE:
ALL
seal parts
MUST
be kept
CLEAN
.
DO NOT
drop seal face carbons, or fl oating seats, nor
scratch the lapped faces of these parts. Seals are
available as a complete assembly only.
Special precautions must be observed when handling a
mechanical seal. To replace the seal, procede as follows:
1. Follow steps 1 thru 5 under “Dismantling”.
2. Reach through bearing openings and push ceramic seat
(2) and seat rubber (3) out of support head.
3. Thoroughly clean seal seat position of frame (19)
Summary of Contents for Deming 3904 Series
Page 10: ...Notes ...